Discover the amazing world of yarn clearers as we dive into their different types and explore how they enhance the quality of your knitting projects.
Crocheting and knitting are not only fun hobbies but also great ways to create beautiful handmade items. However, the key to creating a masterpiece lies in choosing the right yarn.
With so many different types of yarn available, it can be overwhelming to decide which one is best for your project. Fear not! In this article, we will explore the various types of yarn and their characteristics, making it easier for you to choose the perfect yarn for your next project.
So grab a cup of tea and let’s dive into the world of yarn!
Mechanical Yarn Clearers
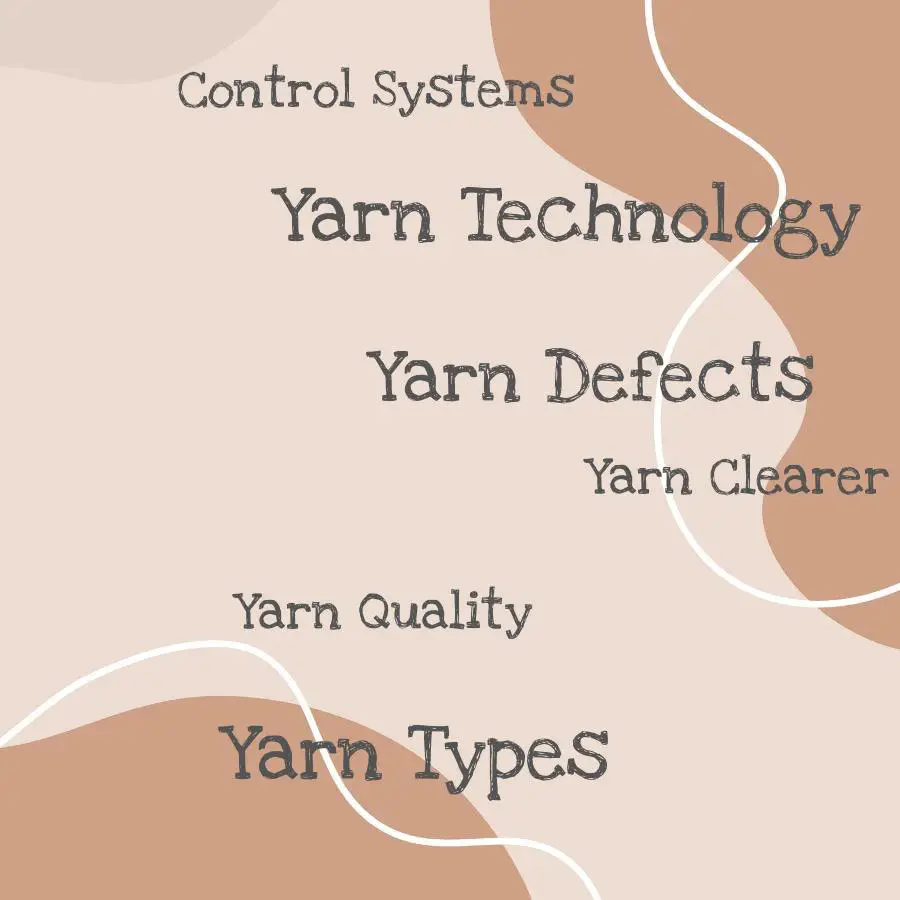
Mechanical yarn clearers are the oldest type of yarn clearer and have been in use for many years. They work by using mechanical sensors to detect any defects or impurities in the yarn as it passes through them.
These sensors then trigger a mechanism that cuts out the defective section of the yarn, ensuring that only high-quality material is used for your project.
One advantage of mechanical clearers is their simplicity, which makes them easy to maintain and repair. However, they do require regular calibration to ensure accurate detection and cutting.
Despite being an older technology compared to electronic or pneumatic clearers, mechanical clearers still play an important role in modern textile manufacturing processes due to their reliability and cost-effectiveness.
Electronic Yarn Clearers
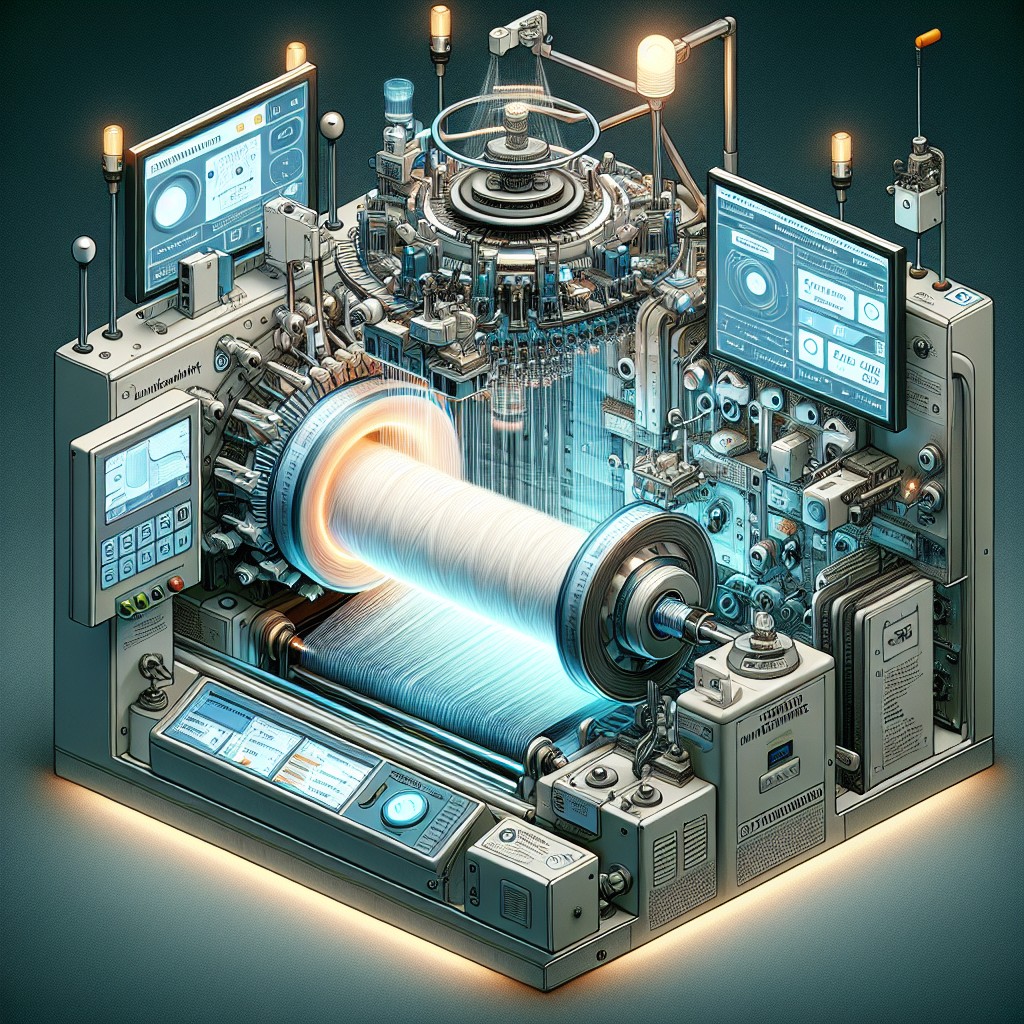
They use electronic sensors to detect and eliminate defects in the yarn during production. These sensors can detect even minor defects that may not be visible to the naked eye, ensuring that only high-quality yarn is produced.
One of the significant advantages of electronic yarn clearers is their ability to store data on different types of defects detected during production. This information can then be used for quality control purposes, allowing manufacturers to identify patterns and trends in defect occurrence and take corrective measures accordingly.
Another advantage is their flexibility when it comes to setting parameters for detecting different types of faults or variations such as thick places, thin places, neps or slubs etc., which makes them suitable for a wide range of applications across various industries.
Pneumatic Yarn Clearers
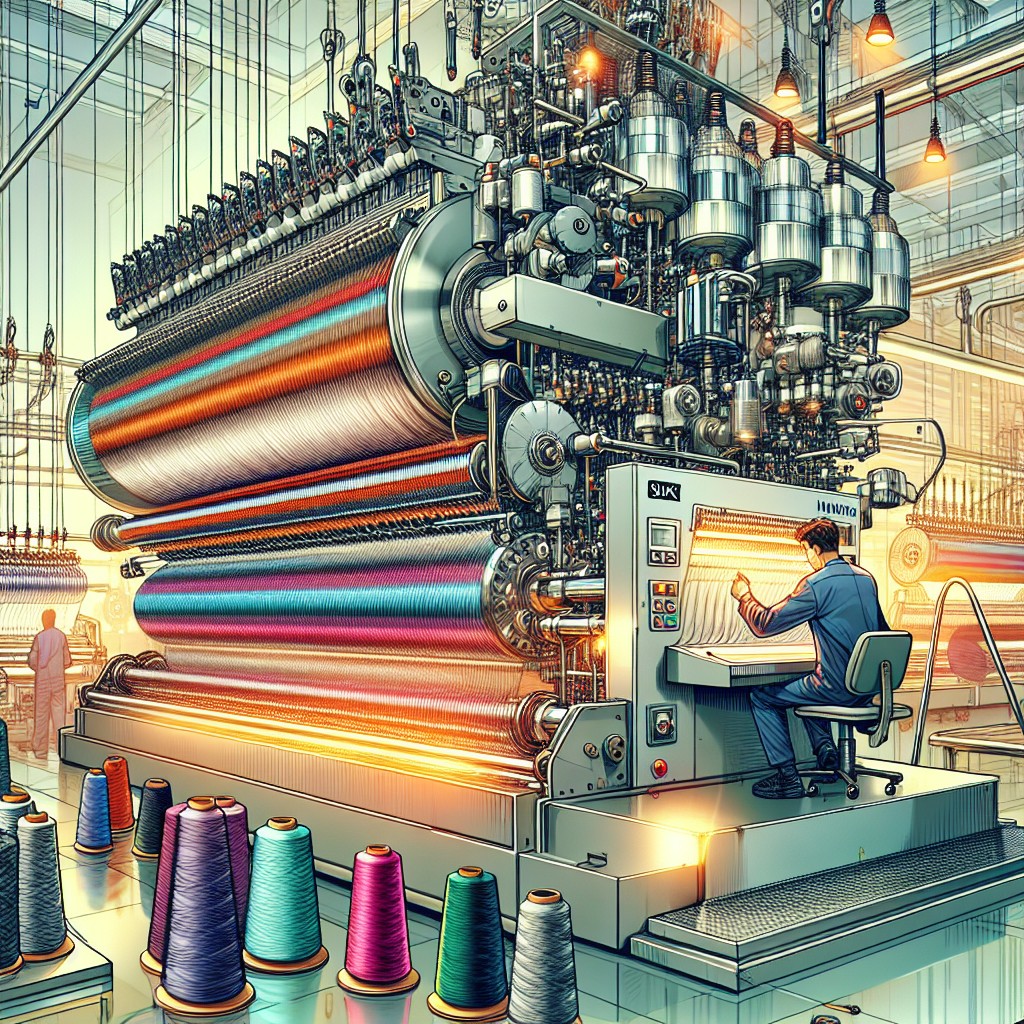
They work by passing the yarn through a sensor, which detects any irregularities such as thick or thin spots, knots, or foreign matter. Once detected, the pneumatic system activates and removes the defective portion of the yarn.
Compared to mechanical clearers that use physical contact with sensors to detect defects in yarns and electronic clearers that use optical sensors for detection purposes; Pneumatic Yarn Clearer is more efficient because it can handle high-speed production lines without causing damage to delicate fibers.
Understanding different types of yard clearers is essential when choosing one for your project.
Yarn Clearer Settings
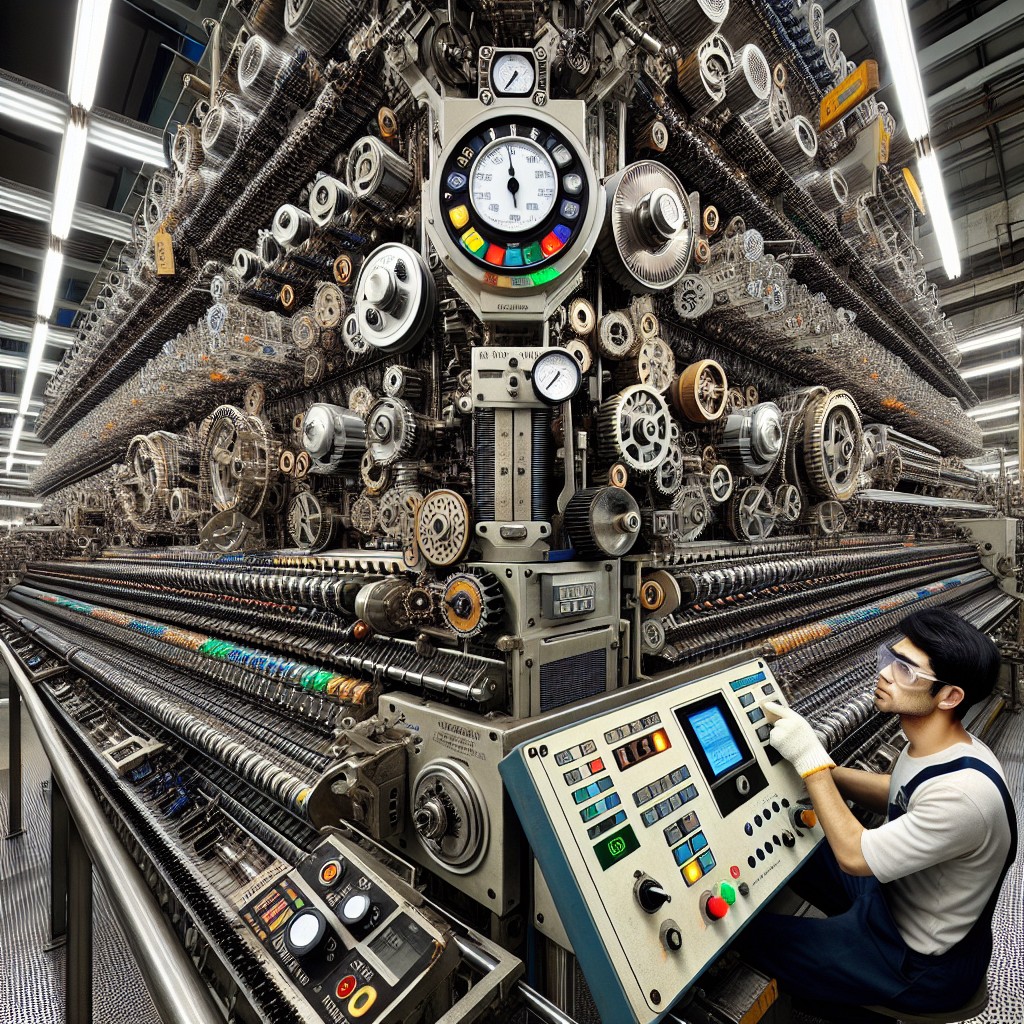
Yarn clearer settings are crucial in ensuring that the yarn quality meets your desired standards. The settings vary depending on factors such as fiber type, spinning process, and end-use application.
Mechanical yarn clearers require manual adjustments to achieve optimal performance. On the other hand, electronic and pneumatic clearers use sensors to detect defects automatically and adjust accordingly.
The most common parameters used in setting up a yarn clearer include sensitivity level, defect size threshold value, speed compensation factor among others. It is important to note that incorrect or inadequate settings can lead to false alarms or missed defects resulting in poor-quality output.
Types of Yarn Defects
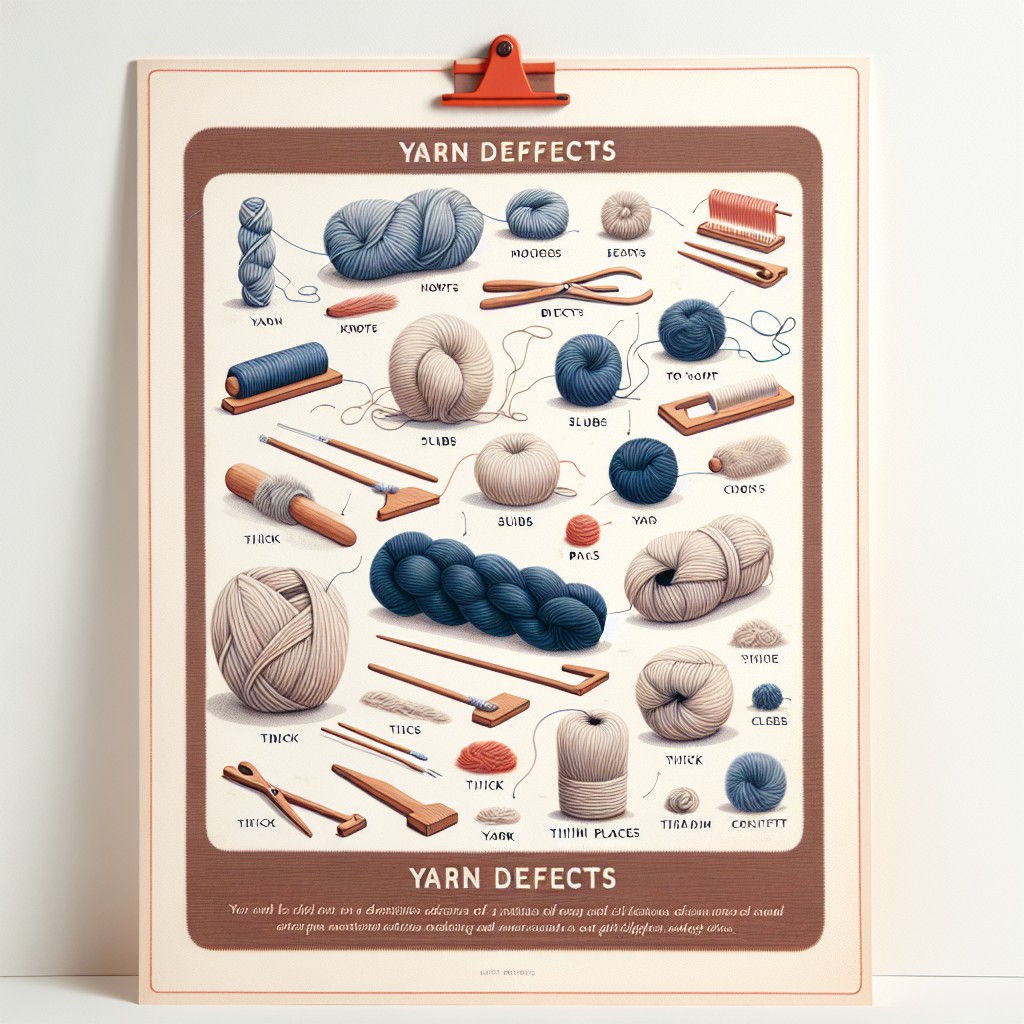
These defects can affect the quality of your finished project and may be difficult to fix. Some common types of yarn defects include knots, slubs, snags, and uneven thickness.
Knots are areas where two ends of a strand have been tied together during production. They can cause interruptions in your knitting or crocheting pattern and create an unsightly bump in your finished product.
Slubs are thicker sections within a strand that result from inconsistencies in spinning fibers together. While some people like the texture they add to their projects, others find them distracting.
Snags occur when fibers become caught on something sharp or rough during production or handling. This creates small loops that stick out from the rest of the yarn strand and make it difficult to work with.
Uneven thickness is another common defect caused by inconsistent spinning techniques which results in variations throughout a single skein making it challenging for knitters who require uniformity for their patterns.
Factors Affecting Yarn Quality
However, several factors can affect the quality of yarn, making it difficult to achieve a consistent result. One factor that affects yarn quality is fiber content.
Different fibers have different properties and characteristics that impact how they behave during spinning and knitting.
Another factor affecting yarn quality is twist level. The amount of twist in a strand determines its strength, elasticity, and drapeability.
A high-twist yarn will be stronger but less flexible than a low-twist one.
Yarn thickness or weight also plays an essential role in determining its suitability for specific projects as well as its overall appearance when knitted up.
Other factors such as dyeing process, storage conditions before use or even humidity levels can all impact on the final product’s look and feel.
Yarn Technology
Today, we have access to a wide range of advanced technologies that help us create high-quality yarns with consistent characteristics. From spinning machines to electronic sensors and control systems, these technologies play an essential role in ensuring that every skein of yarn meets our expectations.
One such technology is the use of yarn clearers. These devices are designed to detect and remove any defects or impurities in the yarn during production, resulting in smoother and more uniform strands.
Mechanical clearers were among the first types developed for this purpose but have been largely replaced by electronic versions due to their higher accuracy levels.
Electronic clearers use sensors that can detect even minor variations in thickness or density along each strand as it passes through them at high speeds on modern spinning machines. They then send signals back to computerized control systems which adjust various parameters like tension settings accordingly until they achieve optimal results.
Yarn Control Systems
They help to ensure that the yarn produced is of high quality and meets industry standards. These systems work by monitoring various parameters such as tension, speed, and diameter during production.
There are different types of Yarn Control Systems available in the market today, ranging from simple mechanical systems to more advanced electronic ones. Mechanical control systems use physical mechanisms such as levers and springs to regulate tension while electronic control systems use sensors and computer algorithms for precise regulation.
The choice between these two types depends on factors like budget, production volume, desired level of automation among others.
Yarn Clearer Applications
They detect and remove any defects or impurities in the yarn, preventing them from causing problems during weaving or knitting. Yarn clearers have a wide range of applications across different stages of textile manufacturing, including spinning mills, winding machines and even knitting machines.
In spinning mills, mechanical yarn clearers are used to monitor and control the quality of spun yarns by detecting faults such as thick places or thin places. Electronic yarn clearer systems can also be used to identify more complex defects like neps (small knots) which may not be visible to human eyes.
In automatic winding machines where cones are produced for further processing into fabrics; pneumatic clearing technology is employed for efficient removal of contaminants on wound packages before they proceed downstream processes such as dyeing.
Yarn Clearer Maintenance
Regular cleaning of yarn clearers helps prevent dust accumulation, which can affect their accuracy. It’s also important to check for any signs of wear and tear on the parts such as sensors or blades and replace them promptly if necessary.
In addition to regular cleaning, it’s recommended that you schedule routine maintenance checks with a professional technician who can inspect your yarn clearer thoroughly. They will be able to identify any potential issues before they become major problems.
Properly maintaining your yarn clearer not only ensures its longevity but also guarantees consistent quality output from your knitting projects.
Yarn Clearer Innovations
Electronic yarn clearers have been a game-changer in the textile industry, providing more accurate and efficient detection of defects. These innovative machines use sensors to detect even the smallest imperfections in yarn quality and automatically stop production when necessary.
Another recent innovation is pneumatic yarn clearers that use air pressure to remove any impurities from the spinning process. This method has proven effective at removing dust particles and other contaminants that can affect overall product quality.
In addition to these advancements, there are also new developments being made with mechanical yarn clearers such as improved settings for better accuracy and control over defect detection.
These innovations have greatly improved efficiency while maintaining high-quality standards for finished products.
Yarn Clearer Types and Setting in Automatic Winding Machine
In an automatic winding machine, yarn clearers are used to detect and remove any defects or impurities present in the yarn before it is wound onto cones. There are different types of yarn clearers available for use with automatic winding machines.
Mechanical Yarn Clearers: These types of clearers work by using mechanical sensors that detect any irregularities on the surface of the thread as it passes through them.
Electronic Yarn Clearer: This type uses electronic sensors to monitor and control various parameters such as tension, speed, diameter and more. They can be programmed with specific settings depending on your requirements.
Pneumatic Yarn Clearer: Pneumatic systems use air pressure to control various aspects such as tension and speed while monitoring for defects or impurities within a given length range.
Functions of Yarn Cleaner
The primary function of a yarn cleaner is to detect and remove any defects or impurities from the yarn before it reaches downstream processes such as weaving or knitting.
The use of yarn cleaners helps to prevent costly downtime caused by machine stoppages due to broken needles, poor fabric quality, or other issues related to defective yarn. Using a high-quality cleaner ensures that only clean and defect-free fibers are used for producing textiles.
There are different types of cleaners available on the market today with varying levels of sophistication. Mechanical clearers rely on mechanical sensors while electronic ones use optical sensors for detecting defects in real-time.
Pneumatic clearers work by blowing air through each strand at high pressure which removes any debris present.
Yarn Cleaner
A yarn cleaner, also known as a yarn clearer, is an essential component in the textile industry that helps to remove any impurities or defects from the raw material before it’s spun into thread or fabric.
There are different types of Yarn Cleaners available on the market today. Some are mechanical while others use electronic sensors to detect and eliminate any defects present in the fiber.
Pneumatic cleaners use air pressure to blow out dirt particles and other contaminants from fibers.
Regardless of their type, all Yarn Cleaners work towards achieving one goal – producing clean and defect-free fibers for spinning into quality threads or fabrics.
Using a Yarn Cleaner can significantly improve your knitting projects’ overall quality by removing unwanted materials that may affect its durability and appearance.
Yarn Control Systems
They ensure that the yarn produced is of high quality and meets industry standards. These systems use various sensors to monitor different parameters such as tension, thickness, and speed during production.
The data collected by these sensors is then analyzed by a computer system which adjusts the machine settings accordingly to maintain consistent quality throughout production. Yarn control systems also help in detecting defects early on in the process, allowing for quick corrective action before it affects too much material.
In addition to improving product quality, yarn control systems also increase efficiency and reduce waste by minimizing downtime due to machine malfunctions or operator errors.
Yarn Clearer Innovations
One of the most significant advancements in yarn clearing technology is the introduction of electronic yarn clearers. These devices use sensors to detect defects in the yarn and automatically adjust settings for optimal quality control.
Another innovation is pneumatic yarn clearers, which use compressed air to remove any impurities or defects from the thread. This method ensures that only high-quality fibers are used in your project.
There has been an increase in research on developing more efficient and accurate types of mechanical yarn clearers that can handle different types of fibers without causing damage or breakage.
As technology continues to advance at a rapid pace, we can expect even more exciting innovations in this field that will revolutionize how we create our knitted projects.
Types of Yarn Defects
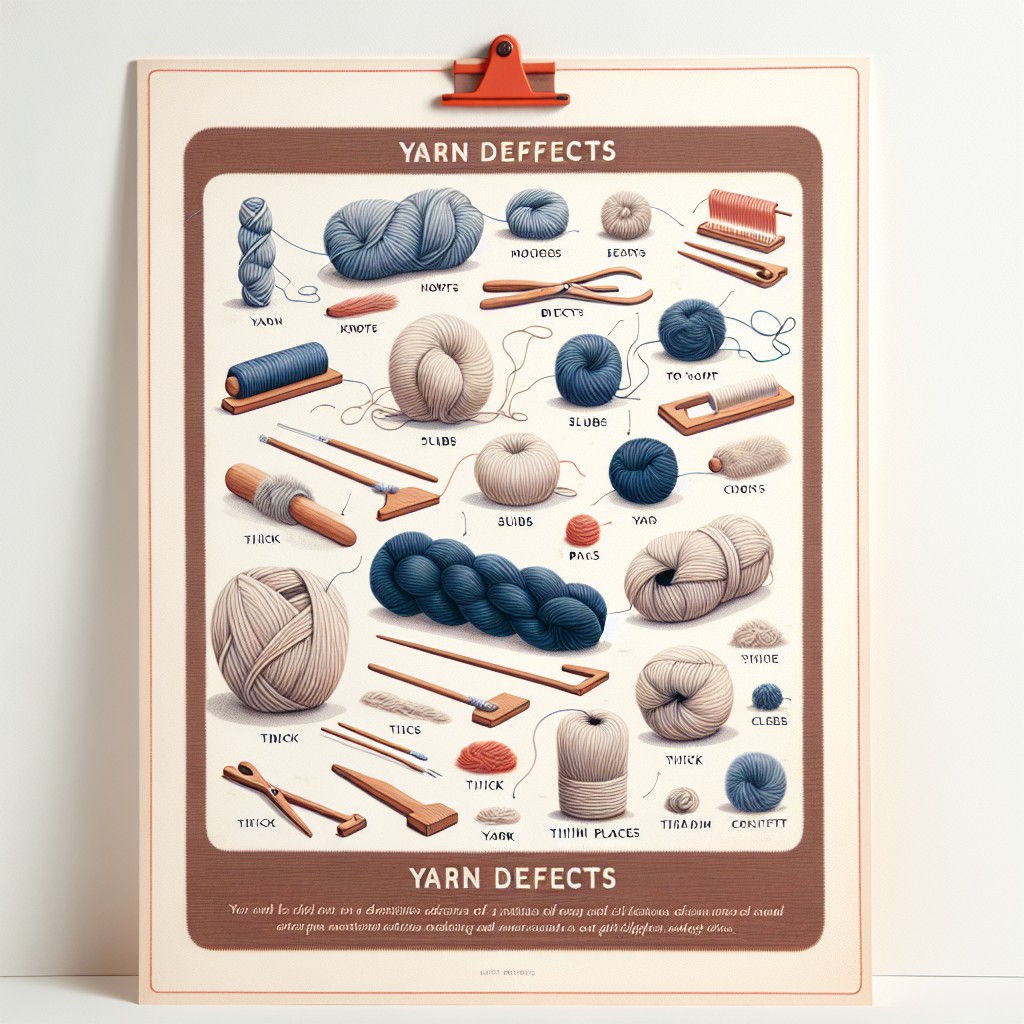
These defects can range from minor issues like knots and slubs to more severe problems such as broken filaments and uneven thickness. Understanding the different types of yarn defects is crucial in selecting high-quality yarn for your projects.
Knots are one of the most common types of yarn defect that occurs when two ends are joined together during spinning. Slubs, on the other hand, happen when there is a thick spot in a strand due to an inconsistency in spinning tension.
Another type of defect is called “neps,” which refers to small balls or clusters formed by entangled fibers that have not been properly carded before being spun into thread. Broken filaments occur when individual fibers break off from their original length while being spun into thread.
Lastly, uneven thickness happens when there are variations in diameter along a single strand resulting from inconsistent tension while spinning or twisting processes.
Factors Affecting Yarn Quality
Several factors can affect the quality of yarn, including fiber type, spinning method, and dyeing process. The fiber type determines how soft or rough the yarn feels and its durability.
Spinning methods also play a significant role in determining the texture and strength of a particular type of yarn.
Moreover, different dyeing processes can impact both colorfastness and overall quality. Some dyes may cause shrinkage or weaken fibers over time while others are more resistant to fading.
It’s essential to consider these factors when selecting your preferred types of yarn clearers as they help you achieve optimal results for each project you undertake.
Yarn Clearer Applications
They detect and remove any defects or impurities in the yarn, resulting in a high-quality finished product. Yarn clearers have various applications across different stages of textile manufacturing processes such as spinning, winding, and weaving.
In spinning mills, mechanical yarn clearers are used to remove foreign particles from raw cotton before it is spun into yarn. Electronic and pneumatic types of yarn clearer systems are also used to monitor fiber quality during carding and combing operations.
In automatic winding machines for producing cones or bobbins of thread for sewing machines or knitting needles; electronic clearing systems ensure that only clean threads pass through them by detecting knots on spools which can cause breaks during processing.
Moreover, when weaving fabrics with multiple colors like tartan patterns; electronic clearing technology helps prevent color contamination between warp (vertical) threads while they’re being woven together with weft (horizontal) ones – this ensures consistent color distribution throughout each piece produced!.
Overall these applications demonstrate how important it is to use appropriate types of Yarn Clearer Systems at every stage so as not compromise on final product quality!.
Yarn Clearer Maintenance
However, like any other machine, they require proper maintenance to function optimally. Regular cleaning and calibration of the yarn clearer can help prevent downtime due to malfunctioning or inaccurate readings.
To maintain your yarn clearer effectively, it is crucial to follow the manufacturer’s instructions on cleaning and calibration procedures. It is also important to keep a record of when you last serviced your machine so that you can schedule regular maintenance checks.
In addition to routine maintenance checks, it is advisable always to inspect your yarn clearer for signs of wear or damage before use. Any worn-out parts should be replaced immediately as they may affect its accuracy.
Properly maintaining your yarn clearer will not only ensure accurate readings but also prolong its lifespan while reducing repair costs over time.
FAQ
What is the purpose of a yarn clearer?
The purpose of a yarn clearer is to remove faults (thick places, thin places, foreign matter) from the yarn, thereby improving its quality and ensuring smooth operation of high-speed textile machinery.
What is electronic yarn clearer?
Electronic yarn clearer is a device that removes faults, such as thick places, thin places, and foreign matter, from yarn to improve its quality and weaving efficiency, primarily used in winding steps.
What is precision winding?
Answer: Precision winding is a process where successive coils of yarn are laid close together in a parallel or near-parallel manner, enabling the production of a dense package with maximum yarn storage in a given volume.
What is yarn winding?
Yarn winding refers to the process of transferring yarns from bobbins, rings, and hanks to more convenient packages like cones, pirns, and cops for both warp and weft yarns.
What is the purpose of a yarn clearer?
The purpose of a yarn clearer is to detect and remove yarn defects, such as thick and thin sections, neps, and slubs, ensuring a consistent, high-quality yarn output.
The purpose of a yarn clearer is to monitor and ensure consistent yarn quality during the winding process by detecting and removing any yarn faults, such as slubs, knots, or weak spots, that could potentially compromise the strength or appearance of the finished product
A yarn clearer’s purpose is to maintain consistent yarn quality during winding by detecting and eliminating faults like slubs, knots, and weak spots, preserving the strength and appearance of the final product.
Please provide the snippet or information related to the question for me to generate an NLP-friendly answer in one sentence.
What is electronic yarn clearer?
An electronic yarn clearer is a device that detects and eliminates yarn defects and contaminants in textile manufacturing processes.
An electronic yarn clearer is a technologically advanced device used in the textile industry for monitoring and controlling yarn quality during the winding process. It uses electronic sensors to detect faults in the yarn, such as thin or thick spots, and removes them automatically, ensuring consistent yarn quality
An electronic yarn clearer is a device in the textile industry that utilizes electronic sensors to monitor and control yarn quality during winding, detecting and automatically removing faults like thin or thick spots for consistent yarn quality.
Please provide the snippet or information for me to base my answer on.
What is precision winding?
Precision winding is a process used in various industries to ensure uniform winding of materials, like wire, thread, or film, for improved product performance and reduced waste.
Precision winding is a controlled yarn winding process that ensures even and consistent tension across the entire length of the yarn. This process helps to maintain the desired properties of the yarn, prevent yarn breakage, and simplify downstream processing, such as weaving or knitting
Precision winding is a yarn winding process that ensures uniform tension throughout the yarn, maintaining its properties, preventing breakage, and simplifying subsequent processes such as weaving or knitting.
Please provide the question and the snippet for me to generate an NLP-friendly answer in one sentence.
What is yarn winding?
Yarn winding is the process of wrapping yarn into manageable coils or spools for convenient use in textile production.
Yarn winding is the process of winding yarn from one package, such as a bobbin or cone, onto another package, typically a cone or a spool, to prepare it for further processing in textile manufacturing. Winding can serve to combine multiple strands or to align yarns with the appropriate tension and evenness required for subsequent processes, such as weaving or knitting
Yarn winding is the process of transferring yarn from one package to another, such as from a bobbin or cone onto a cone or spool, in order to combine strands, apply appropriate tension, and achieve evenness for further textile processing like weaving or knitting.
Please provide the snippet and the question for me to answer it in a single sentence in an NLP-friendly format.
Three more related but unique questions
What are three related questions about the snippet?
What are the various types of winding machines used in the textile industry?
Various types of winding machines used in the textile industry include precision winding machines, step precision winding machines, random winding machines, and drum winding machines.
How do yarn clearers contribute to minimizing production costs and reducing textile waste?
Yarn clearers contribute to minimizing production costs and reducing textile waste by eliminating yarn defects, ensuring higher quality, and reducing material wastage.
What are the key factors to consider when choosing a yarn clearer for a specific textile manufacturing process?
The key factors to consider when choosing a yarn clearer for a specific textile manufacturing process include yarn type, material quality, production speed, and desired end-product quality.