Discover the fascinating world of yarn spinning as we delve into its various types and techniques, perfect for beginners and experienced spinners alike.
Are you a yarn enthusiast who loves to experiment with different textures and colors? Then, you must know that the type of yarn spinning plays a crucial role in determining the final product’s quality. From worsted to woolen and from ring-spun to open-end spinning, there are various techniques used by manufacturers to create yarns with unique properties.
In this blog, we will explore the different types of yarn spinning methods and how they affect your crochet or knitting projects. So, grab your favorite cup of tea and let’s dive into the world of yarn spinning!
Spinning Processes
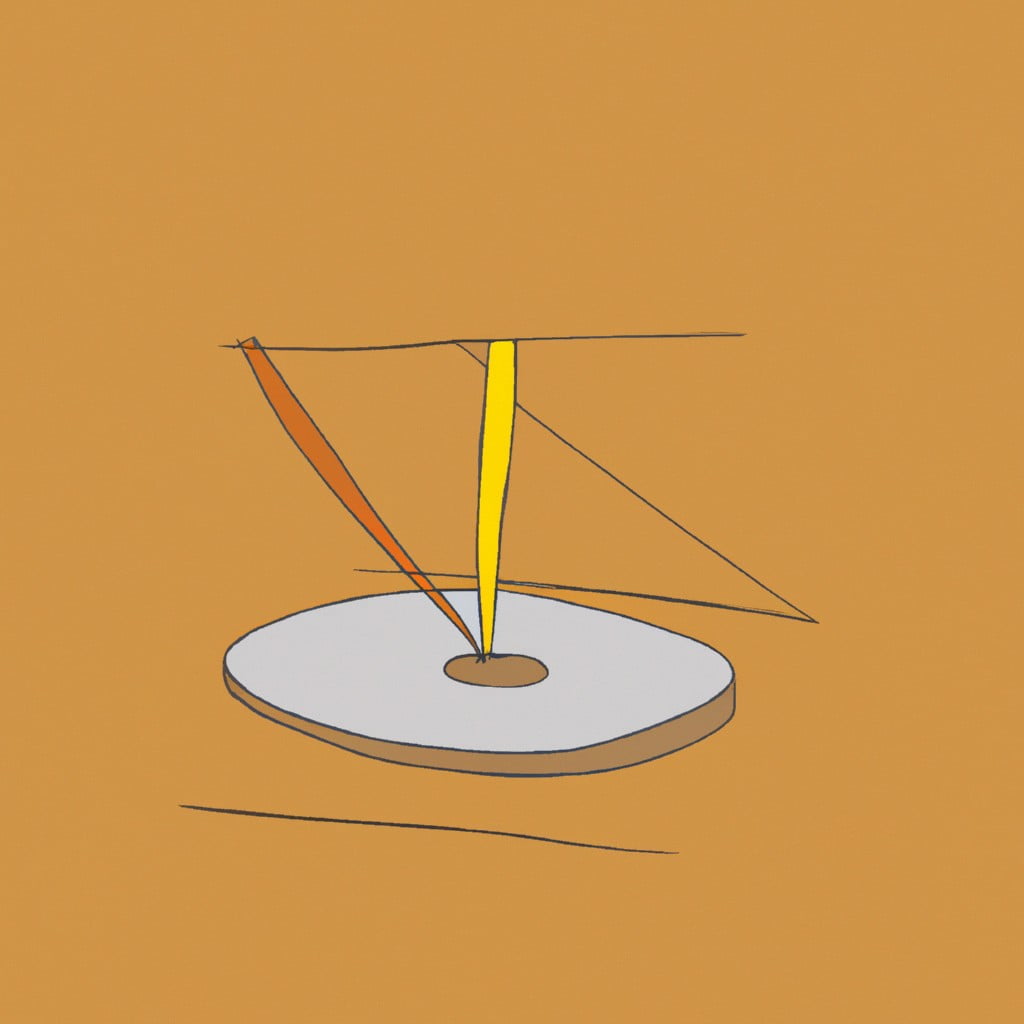
The process involves twisting and drawing out the fibers, which results in a continuous strand of yarn. There are several spinning methods available, each with its unique properties that affect the final product’s texture, strength, and durability.
The most common spinning processes include ring-spun and open-end spinning. Ring-spun is a traditional method that produces high-quality yarns with excellent strength and softness due to their tight twist construction.
On the other hand, open-end spinning is a newer technique that uses rotor machines to produce bulkier yarns at higher speeds.
Other types of spinning processes include wet-spinning for synthetic polymer fibers like rayon or nylon; solution dry-spinning for producing acrylic or modacrylic fiber; gel-spinning for ultra-high molecular weight polyethylene (UHMWPE) fiber production; centrifugal melt electrospinning for nanofiber production from polymers such as polystyrene or polyvinyl alcohol (PVA); among others.
Conversion of Fiber to Yarn
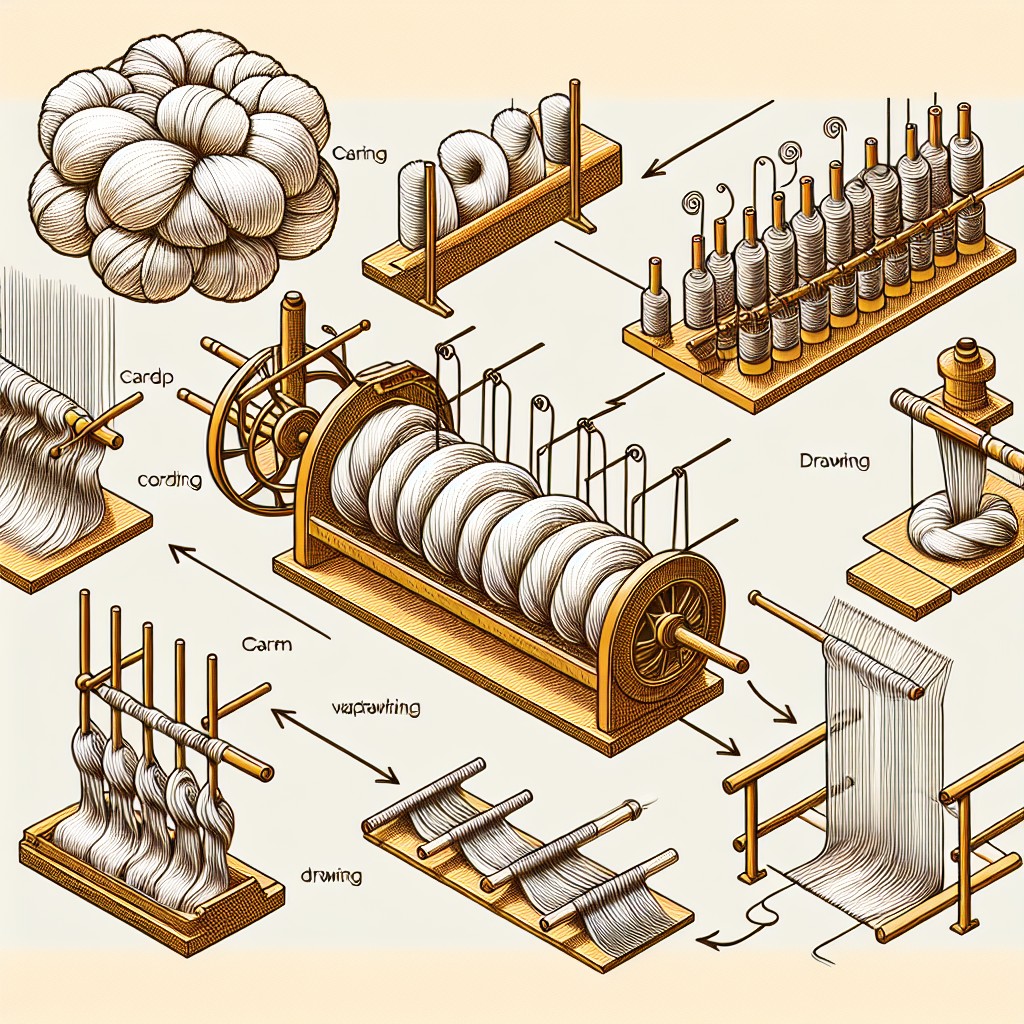
It involves several stages, including cleaning, carding, drafting, and spinning. The first stage is cleaning or scouring the raw material to remove any impurities such as dirt or grease that may affect the quality of the final product.
After cleaning comes carding where fibers are separated and aligned into thin sheets called slivers. These slivers are then drafted by pulling them through rollers with different speeds to create an even thickness throughout.
Finally comes spinning where these drafted fibers are twisted together using various methods depending on what type of yarn you want to produce – worsted or woolen for example.
Spinning Methods
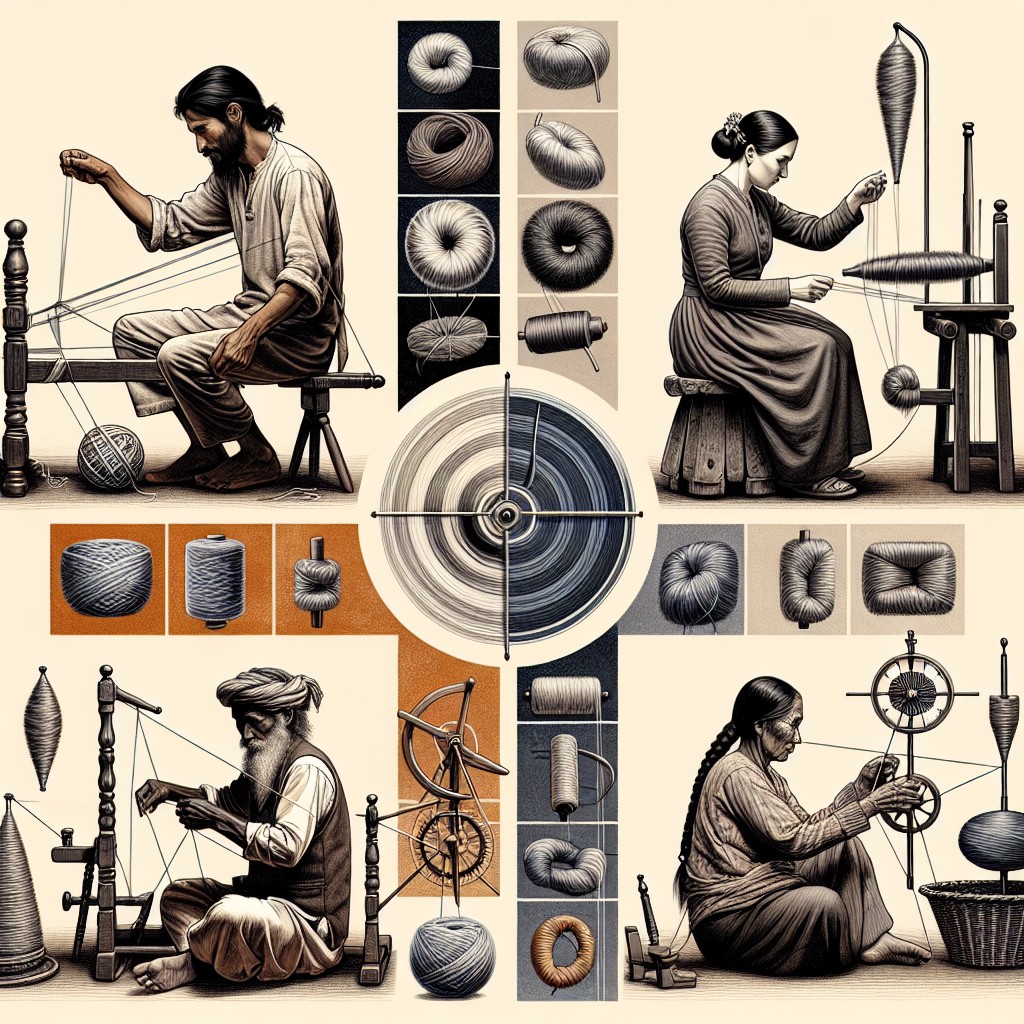
The most common ones include ring-spun, open-end, worsted, and woolen spinning.
Ring-Spun: This method involves twisting the fibers tightly around a central core using a spindle or ring frame. It creates smooth and strong yarn with minimal hairiness.
Open-End: In this method, the fibers are fed into a rotor that spins at high speed to twist them together continuously. Open-end spinning is faster than ring-spun but produces weaker yarn with more hairiness.
Worsted Spinning: Worsted spun yarns have longer staple lengths and undergo combing before being twisted into tight strands for added strength and durability.
Woolen Spinning: Woolen spun yarns use shorter fiber lengths that are carded instead of combed before being twisted loosely together for softness and warmth in finished products like sweaters or blankets.
Each type of spinning has its unique characteristics that affect how it feels when worked up in crochet or knitting projects.
Wet Spinning of Synthetic Polymer Fibers
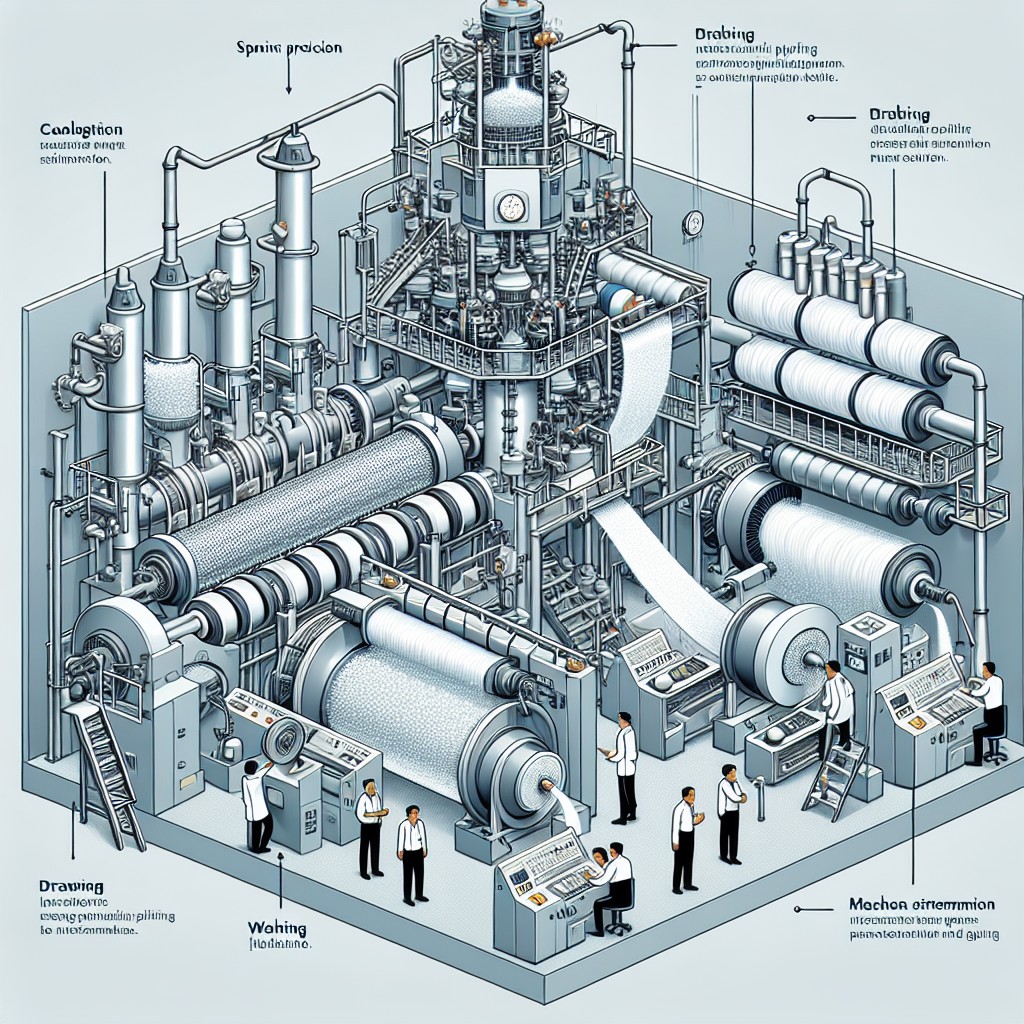
In this process, the polymer solution is extruded through spinnerets into a coagulation bath containing chemicals that solidify the fiber. The coagulation bath can be an acid or salt solution depending on the type of fiber being produced.
The wet spinning process allows for precise control over fiber diameter and mechanical properties by adjusting factors such as temperature, concentration of chemicals in the coagulation bath, and speed of extrusion. This technique produces high-quality fibers with excellent strength-to-weight ratios that are ideal for use in textiles.
One advantage of wet spinning over other methods like dry spinning is its ability to produce continuous filaments without breakage or defects. It offers greater flexibility in terms of producing different types of polymers with varying chemical compositions.
Manufacturing Methods for Textile-Reinforced Concrete
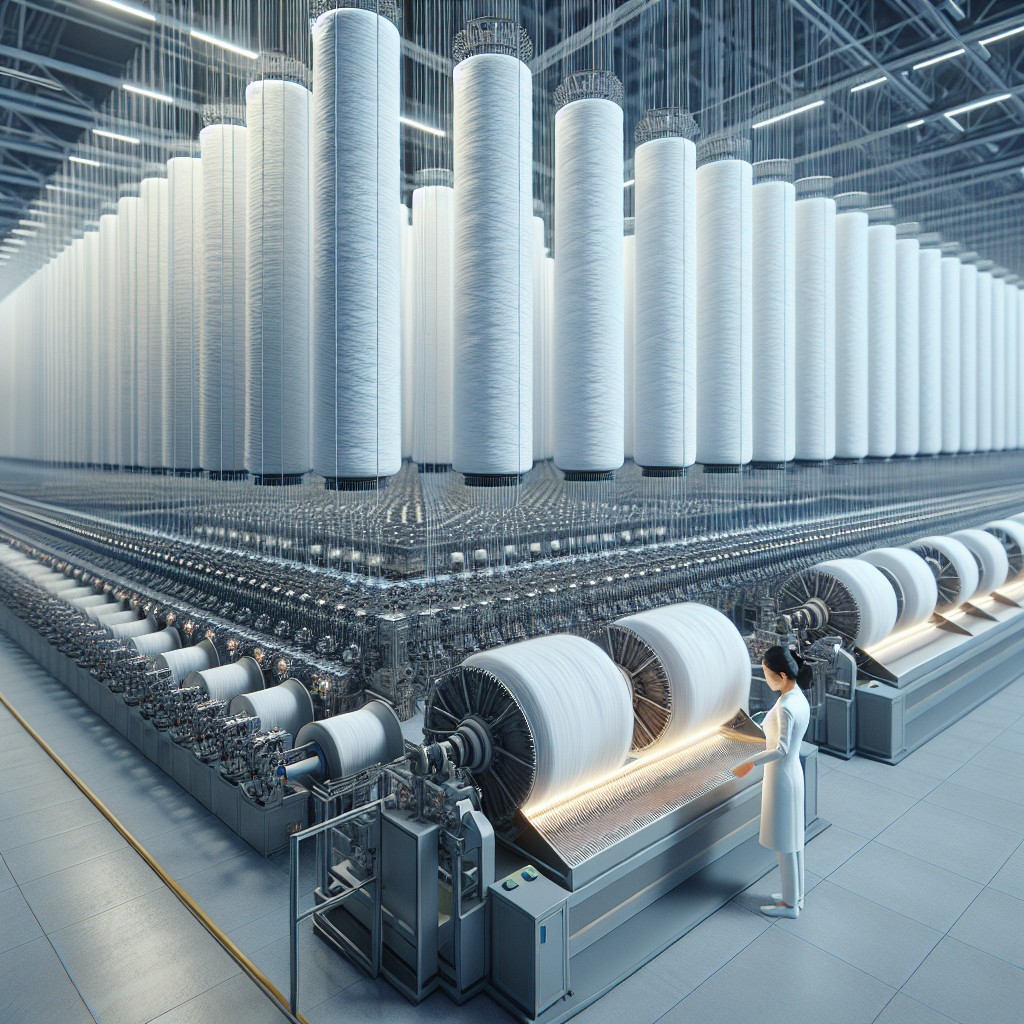
TRC has gained popularity in recent years due to its excellent mechanical properties, low weight, and ease of manufacturing. One method used for producing TRC involves impregnating textile fabrics with cementitious materials before casting them into molds.
Another popular technique for making TRCs is called “fabric-formed concrete.” In this process, a fabric sheet made from high-strength fibers such as carbon or glass is stretched over a mold frame. The fabric’s tension helps to hold the wet concrete in place while it sets, creating an incredibly strong structure once cured.
Both methods have their advantages depending on the application requirements; however, they share some common benefits such as reduced construction time compared to traditional reinforced-concrete structures and improved resistance against cracking under load-bearing conditions.
Textile-reinforced concretes are becoming increasingly popular due to their unique combination of strength and flexibility.
Gel Spinning
This process is commonly used in the production of bulletproof vests, ropes, and other applications where strength and durability are essential.
The gel spinning process begins with dissolving polymer materials in solvents to form a liquid solution. The solution then undergoes several stages before it becomes solidified into a gel-like state.
Once the material has reached this stage, it can be extruded through small holes or nozzles at high pressure to produce long continuous filaments.
One significant advantage of using Gel Spinning over other methods is its ability to produce ultra-high molecular weight polyethylene (UHMWPE) fibers with exceptional strength-to-weight ratios. These UHMWPE fibers have been shown to be up 15 times stronger than steel while being much lighter in weight.
Spinning of Ultra-Fine Fibers
This method involves the use of high-speed spinning machines that can spin fibers at speeds up to 100,000 revolutions per minute. The resulting yarns are incredibly strong and have unique properties such as high surface area-to-volume ratio and excellent filtration capabilities.
Ultra-fine fiber spinning has numerous applications in various industries such as medical textiles, environmental protection materials, and advanced composites. For instance, these ultra-thin fibers can be used in air filters for removing pollutants from the air or as scaffolds for tissue engineering.
Spinning of ultra-fine fibers is an exciting field that offers endless possibilities for creating innovative products with exceptional properties.
Direct Spinning
This process involves cleaning, carding, and drafting the fibers before they are spun into yarn. Direct spinning is commonly used for woolen and worsted yarns as it produces a more consistent product with fewer imperfections.
In direct spinning, the fibers are fed through rollers that align them in parallel strands called slivers. The slivers then pass through a drafting zone where they are stretched to create an even thickness throughout the length of each strand.
These strands are twisted together to form single or plied yarns.
One advantage of direct spinning is that it allows manufacturers to produce custom blends by combining different types of fibers during processing. This technique also enables spinners to control various properties such as texture, strength, elasticity and color variation in their final products.
Solution Dry Spinning
In this process, the polymer solution is first prepared by dissolving it in a suitable solvent. The solution is then pumped through spinnerets into a warm air chamber where the solvent evaporates leaving behind solidified fibers.
The advantage of Solution Dry Spinning over other spinning methods lies in its ability to produce high-quality yarns with excellent strength and durability. This method allows for greater control over fiber properties such as diameter and porosity.
Solution Spinning
In this process, the polymer is dissolved in a solvent to create a viscous solution that can be extruded through spinnerets into filaments. The solvent evaporates during the spinning process leaving behind solid fibers.
One of the advantages of solution spinning is its ability to produce continuous and uniform fibers with high strength-to-weight ratios. It allows for precise control over fiber diameter and properties by adjusting factors such as temperature, humidity levels or concentration of solvents.
However, there are also some drawbacks associated with this method including environmental concerns due to toxic solvents used in production processes which can pose health risks if not handled properly.
Review of Spinning Methods
In this section, we will review some of the most popular spinning methods and how they differ from each other.
Ring Spinning: This is one of the oldest and most common spinning techniques used in the textile industry. The process involves twisting fibers together using a spindle and ring frame machine.
Ring-spun yarns are known for their strength, durability, and smoothness.
Open-End Spinning: Unlike ring-spinning that uses a spindle to twist fibers together continuously; open-end spinning employs rotor machines that spin fiber strands into yarn without twisting them first. Open-end spun yarns tend to be less expensive but not as strong or soft as ring-spun ones.
Worsted Spinning: Worsted woolen mills use long-staple wool fibers combed before being spun into fine worsted threads with high tensile strength suitable for weaving fabrics like suits or trousers.
Woolen Spinning: Woolen mills use shorter staple length wools carded before being spun into thicker woolen threads with lower tensile strength ideal for knitting sweaters or blankets.
Centrifugal Melt Electrospinning
This method involves the use of centrifugal force to spin molten polymer droplets into nanofibers. The process starts by melting the polymer and then feeding it through a small orifice at high speed, creating tiny droplets that are then subjected to an electric field.
As these charged droplets move towards the collector, they stretch out into thin fibers due to electrostatic forces.
This spinning method has several advantages over traditional methods such as solution spinning and melt-spinning processes. Firstly, it allows for precise control over fiber diameter and morphology while producing uniform fibers with high surface area-to-volume ratios that can be tailored for specific applications in various fields like biomedicine, energy storage devices or filtration systems.
Moreover, Centrifugal Melt Electrospinning is highly scalable since it does not require solvents or complex equipment setups like other techniques do; this makes it more cost-effective than other methods in terms of production costs per unit weight of material produced.
Melt-Spinning Process
In this process, the polymer chips are melted at high temperatures and extruded through spinnerets to form continuous filaments. The filaments are then cooled down by passing them through a quenching chamber filled with air or water.
The melt-spinning process allows manufacturers to produce fibers of different diameters and lengths depending on the application requirements. For instance, fine denier fibers can be used in clothing fabrics while thicker ones can be utilized in industrial applications such as ropes or carpets.
One of the advantages of melt spinning is that it produces uniform fiber properties due to its controlled manufacturing conditions. It’s an efficient method since large quantities of yarns can be produced quickly using automated machinery.
Advanced Polyimide Fibers
These fibers are made by spinning polyamic acid solutions into a fiber form, which is then subjected to high-temperature treatment to convert it into the final product. The resulting fiber has excellent resistance against heat, chemicals, and radiation making them ideal for use in harsh environments such as aerospace applications.
Polyimide fibers also exhibit superior strength-to-weight ratio compared to other materials like steel or aluminum alloys. This property makes them an attractive choice for lightweight structural components where weight reduction is critical without compromising on performance.
Advanced polyimide fibers offer unique advantages over traditional materials used in various industries ranging from aerospace engineering to electronics manufacturing. With continued research and development efforts focused on improving their properties further while reducing production costs simultaneously, we can expect these innovative materials’ widespread adoption soon enough!
FAQ
What are the 4 types of spinning?
The 4 types of spinning are wet spinning, dry spinning, melt spinning, and gel spinning.
What are the three types of spinning?
The three types of spinning processes are melt spinning, dry solution spinning, and wet solution spinning.
What are the three techniques of yarn spinning?
The three techniques of yarn spinning are ring spinning, open-end (rotor) spinning, and air-jet spinning.
What are the main differences between the various spinning techniques used for yarn production?
The main differences between various spinning techniques for yarn production lie in the fiber materials used, the machines involved, and the resulting texture and strength of the final yarn product.
How do different types of spinning methods impact the quality and texture of yarn?
Spinning methods impact the quality and texture of yarn by determining factors such as fiber alignment, twist tightness, and yarn uniformity, ultimately affecting the resulting yarn consistency and feel.
What are the factors to consider when choosing a spinning method for a particular type of fiber?
When choosing a spinning method for a particular type of fiber, consider factors such as fiber length, strength, desired yarn properties, cost, and production speed.