Discover the diverse world of yarn spinning mills as we delve into various types and their unique production techniques in this informative blog post.
Are you a yarn lover who is curious about the process of how your favorite yarns are made? Have you ever wondered about the different types of spinning mills and how they impact the quality of yarn? Look no further! In this article, we will take a deep dive into the various types of yarn spinning mills and their unique characteristics. From ring spinning to open-end spinning, we’ll explore each method’s advantages and disadvantages to help you better understand which type of mill produces your preferred type of yarn.
So grab your favorite cuppa, settle in, and let’s unravel the mystery behind these fascinating machines!
Yarn Spinning
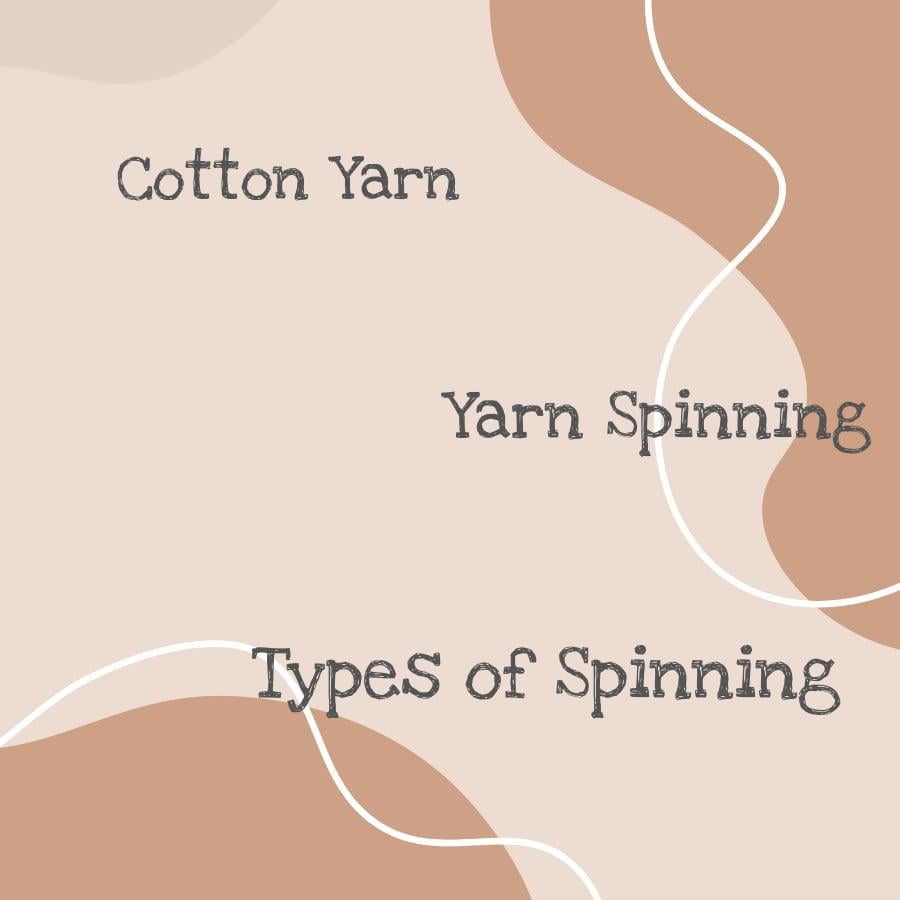
Yarn spinning is the process of creating yarn from fibers. It’s a crucial step in the production of textiles, and it determines the quality and characteristics of the final product.
There are several types of yarn spinning techniques used by mills worldwide, each with its unique advantages and disadvantages.
Ring spinning is one such technique that has been around for centuries. This method involves twisting fibers together using a spindle to create strong, durable yarns suitable for knitting or weaving fabrics.
Rotor spinning is another popular technique that uses high-speed rotors to twist fibers into thread-like structures quickly. The resulting yarns are lightweight but not as strong as those produced through ring-spinning methods.
Air-jet spinning utilizes compressed air to spin fiber strands into fine threads at high speeds while minimizing waste material during production processes.
Ring Spinning
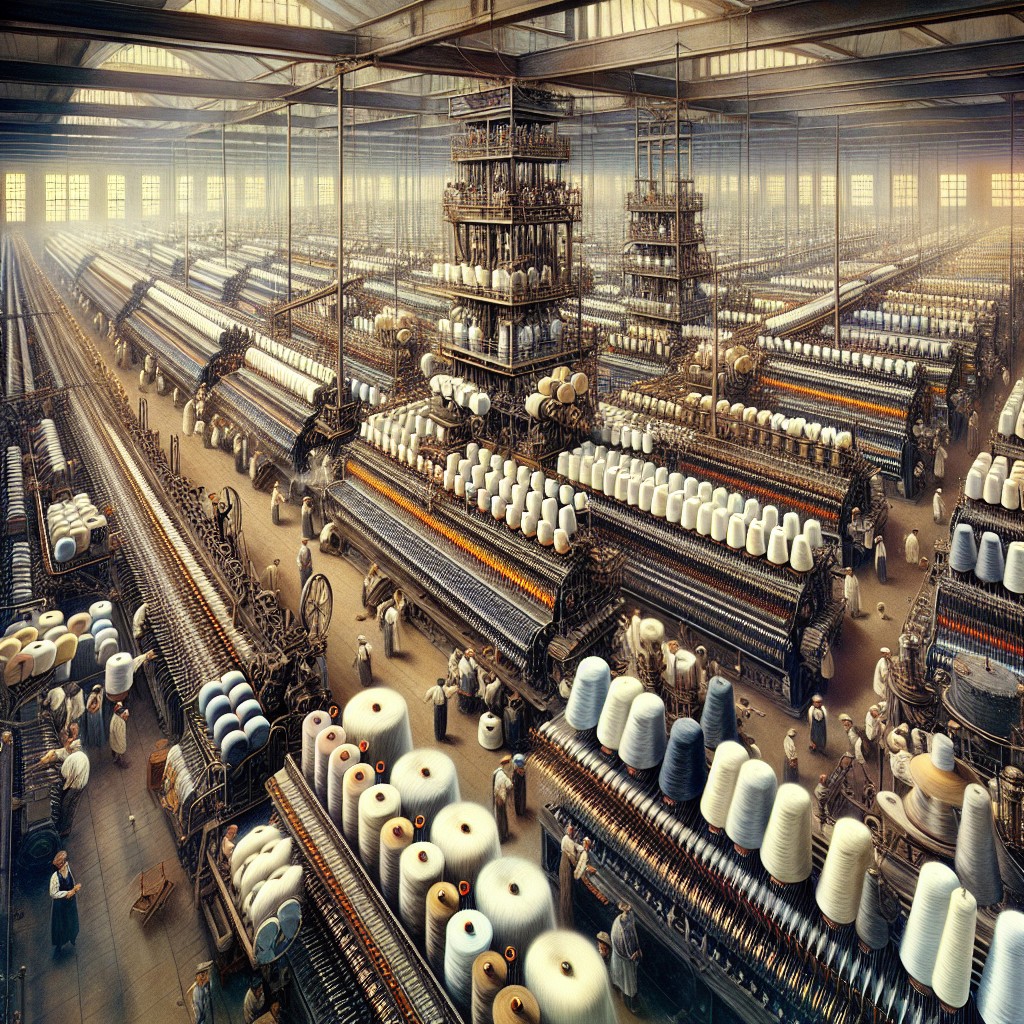
It involves twisting fibers together to create a continuous strand of yarn. The process starts with roving, which is a long and narrow bundle of fiber that has been carded and combed to align the fibers in parallel.
The roving then goes through several stages where it’s drafted, twisted, and wound onto bobbins using ring spinning machines. These machines have a spindle that rotates at high speed while simultaneously pulling out the fiber from the roving bundle.
One advantage of ring spinning is its ability to produce strong and durable yarns due to its tight twist construction. However, this method can also result in some drawbacks such as lower productivity rates compared to other types like rotor or air-jet spinning.
Rotor Spinning
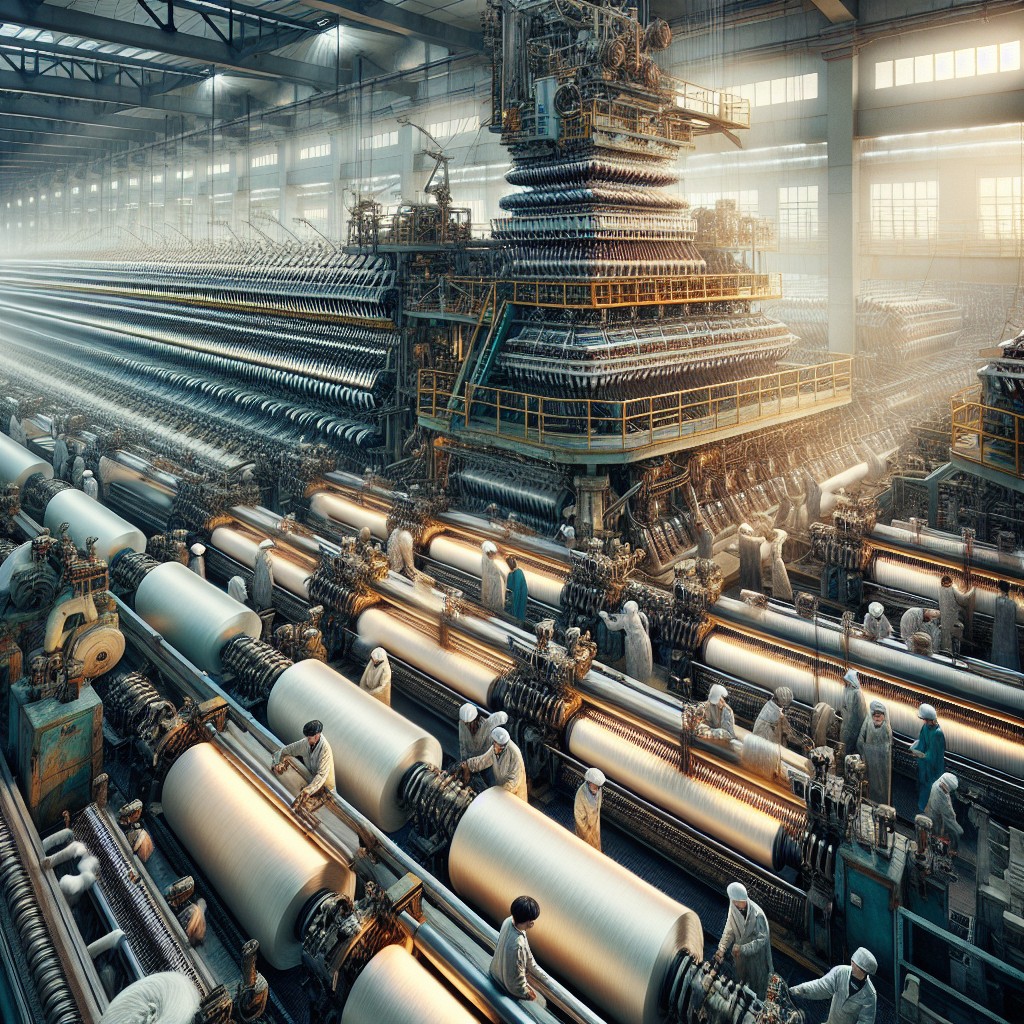
This technique involves using a rotor to twist and spin fibers into yarn, making it an efficient and cost-effective way to produce large quantities of yarn quickly.
One advantage of rotor spinning is its ability to handle various types of fibers, including cotton, wool, polyester, and acrylic. The process also produces high-quality yarn with excellent strength properties due to the tight twisting action during production.
However, there are some disadvantages associated with this method as well. Rotor-spun yarns tend to have lower quality compared to ring-spun or air-jet spun varieties because they can be less uniform in thickness and texture.
The process can cause more fiber damage than other methods due to the high-speed rotation involved.
Air-Jet Spinning
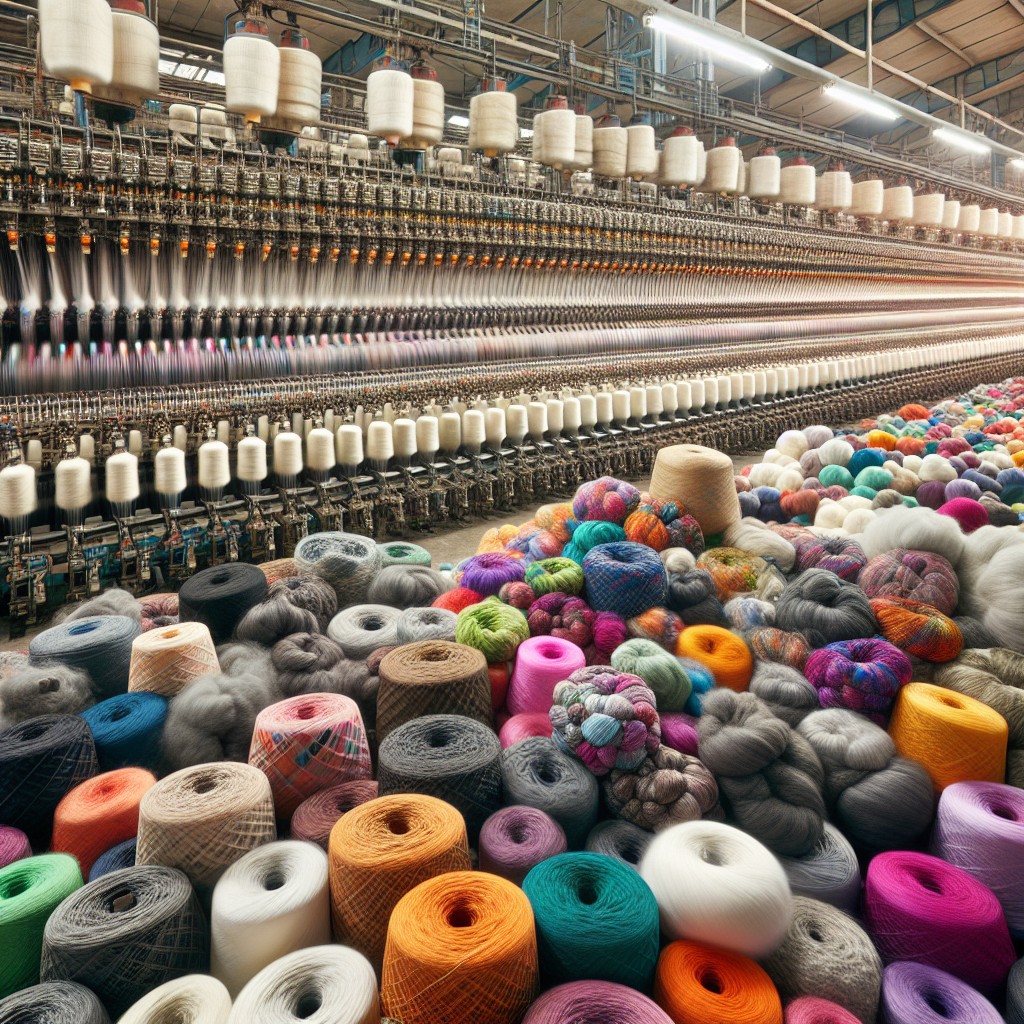
This technique uses compressed air to twist and wrap fibers into yarn, resulting in a high-quality product with excellent strength and durability. The process involves feeding the fiber through an air-jet nozzle at high speed, where it is twisted together by the force of the compressed air.
One significant advantage of Air-Jet Spinning over other methods is its ability to produce fine and uniform yarns quickly. It also requires less energy than traditional ring spinning machines, making it more environmentally friendly.
However, there are some drawbacks to this method as well. The process can be noisy due to the use of compressed air, which may not be suitable for all production environments.
Air-Jet spun yarns tend to have lower elasticity compared to ring-spun varieties.
Types of Spinning
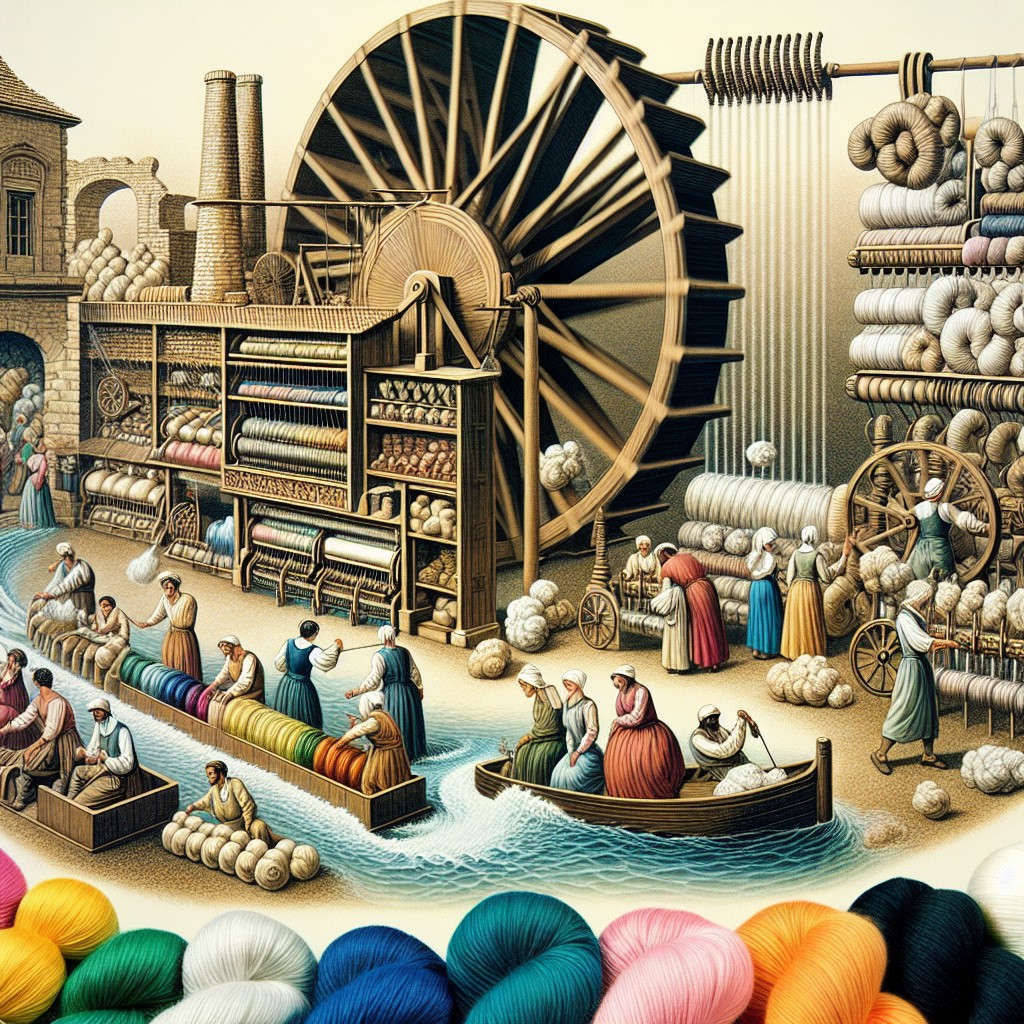
The most common types include ring spinning, rotor spinning, and air-jet spinning.
Ring Spinning: This is the oldest and most widely used method for producing yarn. It involves twisting fibers together using a spindle and a ring frame to create continuous strands of yarn.
Rotor Spinning: In this method, fibers are fed into a rapidly rotating open-end rotor that twists them together to form yarn continuously. Rotor spun yarns tend to be coarser than those produced by other methods but can be more cost-effective for large-scale production.
Air-Jet Spinning: This relatively new technology uses compressed air jets to twist fibers into fine threads at high speeds. Air-jet spun yarns have excellent strength properties but require specialized machinery that can make them more expensive than other options.
Understanding the different types of spinning mills is essential in choosing the right type of mill for your project or product needs.
Cotton Yarn Spinning Process
The cotton fiber is known for its softness, breathability, and durability. However, the process of spinning cotton into yarn can be quite complex.
The first step in the cotton yarn spinning process involves cleaning and carding the raw cotton fibers to remove any impurities or debris. Next, these fibers are drawn out into a thin strand called a sliver.
The sliver then goes through several stages of drafting where it’s stretched out further to create an even thinner strand that will eventually become your finished thread or yarn.
After drafting comes twisting – this is where two or more strands are twisted together to form a stronger single ply thread which can then be plied again with other threads if desired for added strength.
Spinning of Cotton Yarn
The spinning process for cotton yarn involves several steps, including carding, drawing, roving, and spinning. During the carding stage, fibers are separated from impurities like seeds or leaves to create a uniform fiber length.
Next comes drawing where multiple strands are combined into a single strand to increase strength and consistency.
After that comes roving where the drawn-out fibers are twisted together into long ropes called slivers which then undergo further twisting during spinning to form cotton yarns with varying thicknesses depending on their intended use.
The quality of cotton yarn depends on various factors such as fiber length and fineness as well as how tightly it’s spun during production. Cotton can be spun using different methods such as ring spinning or open-end rotor spinning depending on desired characteristics like softness or durability.
Difference Between Spinning and Weaving
While spinning involves twisting fibers together to create yarn, weaving is the process of interlacing these yarns to form a piece of cloth or fabric.
In spinning, fibers such as cotton, wool or silk are drawn out into long strands before being twisted together using various techniques. The resulting product is then wound onto bobbins or spindles for use in knitting, crocheting or weaving.
Weaving on the other hand involves taking these spun threads (or sometimes pre-made fabrics) and interlacing them at right angles with another set of threads called weft. This creates a stable structure that can be used for clothing items like shirts, pants etc., as well as household textiles like curtains and bedspreads.
While both processes may seem similar at first glance since they involve working with thread-like materials; they differ significantly in terms of their end products’ characteristics. Spun yarn tends to have more texture than woven fabrics due to its twisty nature while woven fabrics tend towards smoothness because there’s no twist involved during production.
Understanding this difference between spinning and weaving helps us appreciate how each process contributes uniquely towards creating beautiful finished products from raw materials – whether it’s cozy sweaters made from soft woolen spun-yarns or elegant dresses crafted from intricately woven silks!.
FAQ
What are the different types of spinning processes?
Answer: The different types of spinning processes include ring-spun, rotor-spun, twistless, wrap-spun, and core-spun yarns.
What are the three types of spinning?
The three types of spinning are melt spinning, dry solution spinning, and wet solution spinning.
What are the different types of spinning wool?
Answer: The two types of spinning wool are ring spinning, similar to worsted yarn production, and mule spinning, unique to the woollen spinning industry.
What are two names of fibers that can be spun by different spinning methods?
Two names of fibers that can be spun by different spinning methods are viscose (the most common form of rayon) and synthetic polyester.
What are the various factors that affect the choice of spinning method in a yarn spinning mill?
Various factors affecting the choice of spinning method in a yarn spinning mill include fiber type, yarn count, desired yarn properties, required production capacity, and overall cost efficiency.
How do the properties of spun yarn differ between the different spinning techniques?
Different spinning techniques result in spun yarns with varying properties in terms of strength, texture, and appearance.
What is the role of technology advancements in modern spinning mills and their impact on yarn production?
Technology advancements in modern spinning mills play a crucial role in enhancing yarn production efficiency, quality, and reducing labor costs.