Delve into the intriguing world of yarn making because understanding various tools will effortlessly take your crafting to a whole new level of creativity.
Key takeaways:
- Spinning wheels transform fiber into yarn using twist and tension.
- Drop spindles are portable and ideal for beginners.
- Fiber preparation tools like carders and combs make spinning easier.
- Blending boards allow for custom fiber blends and color experimentation.
- Choose the right wool breed for your spinning needs.
Spinning Wheels
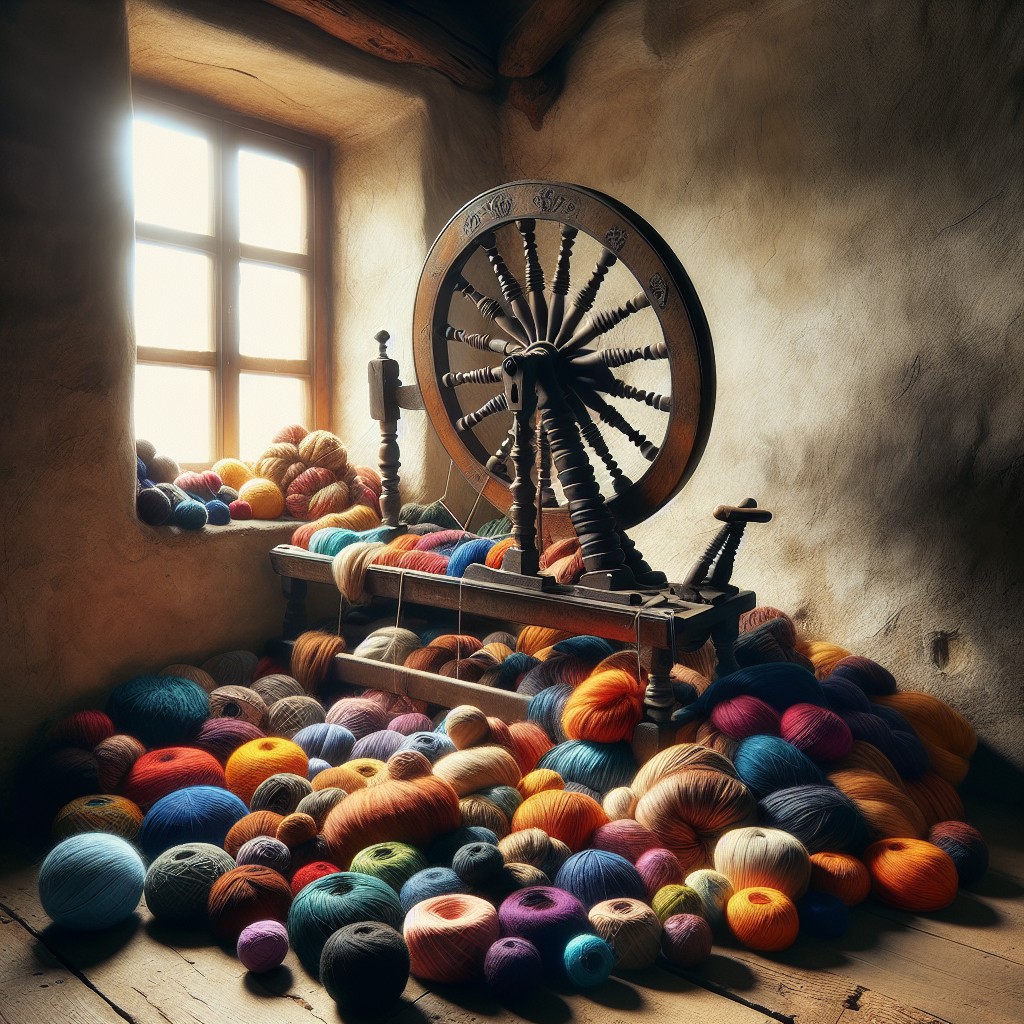
As the centerpiece of yarn making, spinning wheels transform fiber into yarn using the principles of twist and tension. The wheel, powered by hand or foot, drives the flyer to twist the fibers, while the tension system feeds it onto the bobbin at a consistent rate. Modern spinners can choose between traditional single-drive wheels, which use one drive band, or double-drive wheels, which feature two for added control over tension and twist. There are also upright or castle-style wheels that save space, and horizontal or Saxony-style ones that are more traditional.
Portability is a consideration for crafters on the move; if so, consider a folding or compact wheel. Ratios are another key feature – they determine how many times the flyer rotates per pedal and affect the yarn’s twist speed. Higher ratios allow for finer yarns, while lower ratios are suitable for thicker, bulkier yarns. Each wheel type has a learning curve, and before investing, it’s wise to try out different models to find the one that feels most intuitive and comfortable for your spinning style.
Drop Spindles
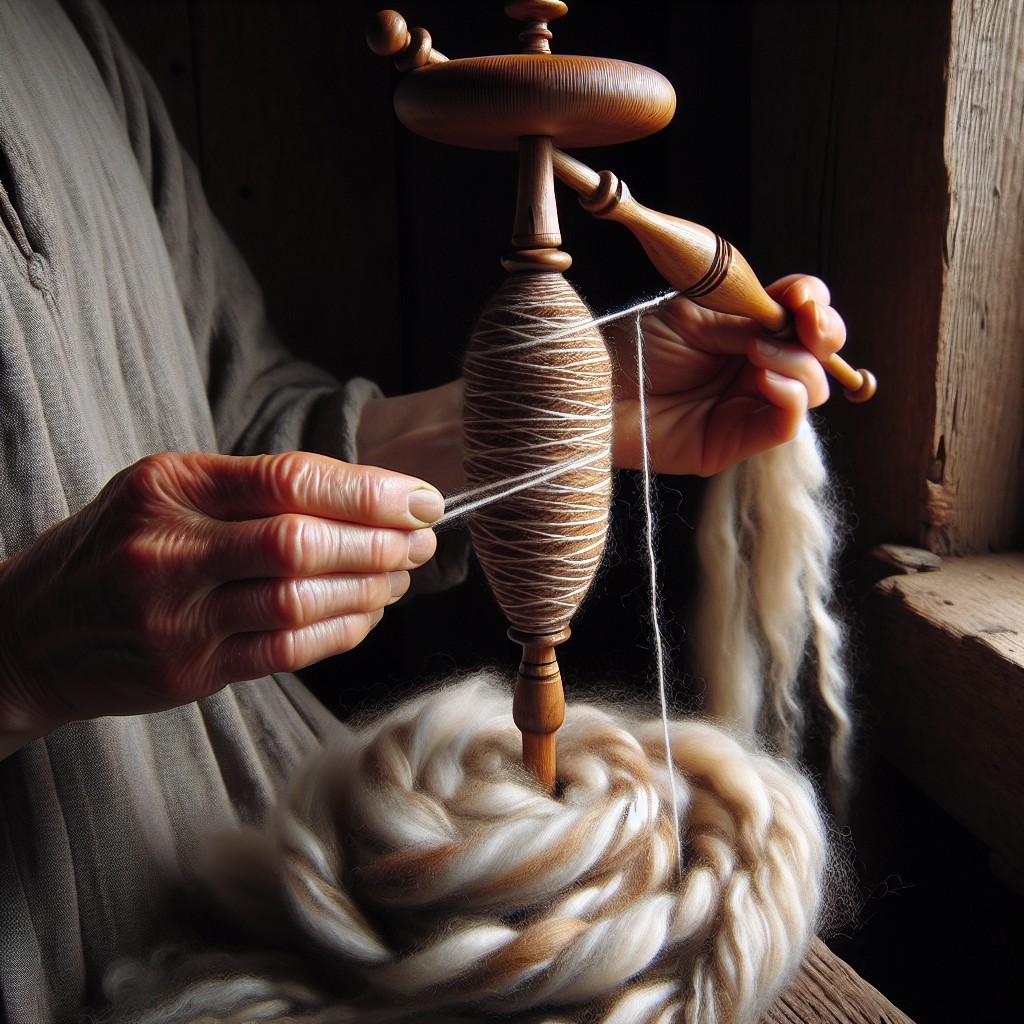
Drop spindles are an ancient and accessible tool for creating yarn. Ideal for beginners, they’re portable and affordable, offering a simple yet effective introduction to spinning.
The spindle’s basic parts include a whorl – the weighted disc which gives it momentum – and a shaft, which the spun yarn is wound around. Drop spindles come in top-whorl, bottom-whorl, and Turkish styles, each affecting the yarn’s twist and drafting method slightly differently.
To use a drop spindle, pinch fibers from prepared wool, flax, or other materials, and twist them around the shaft to start. Spin the whorl for the twist that binds fibers into yarn, then wind the yarn onto the spindle. The process, often called “park and draft,” can be adapted to different fibers and desired yarn thicknesses.
For consistency, periodically check the spun yarn’s twist and thickness. Remember, practice refines technique, leading to more uniform results over time. Drop spindles not only teach patience and hand coordination, but they also allow an intimate understanding of yarn structure and quality.
Fiber Preparation Tools
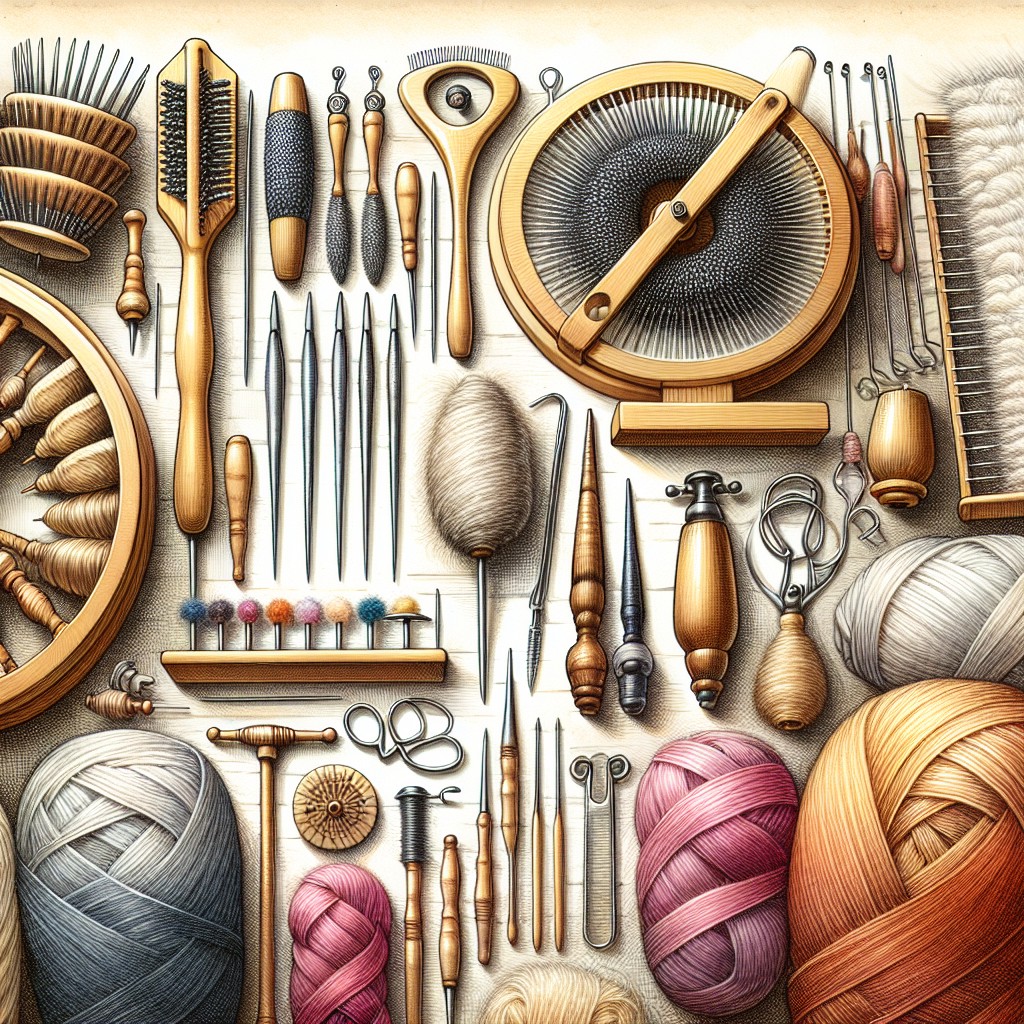
Before transforming wool or other fibers into yarn, it’s essential to ensure they are clean, untangled, and aligned for spinning. That’s where fiber preparation tools come into play. These devices are designed to organize and smooth out fibers, making them easier to spin and resulting in a more even yarn.
A drum carder is a popular mechanized option that can process larger quantities of fiber. Feed fleece into the carder, and it will produce batts or continuous roving. Hand carders, resembling large, wire-brushed paddles, are perfect for smaller batches or more detailed blending, allowing for custom color and fiber mixes.
For those aiming for a truly hands-on experience, a flick carder or a pair of wool combs are highly effective. Wool combs will straighten fibers and remove debris, creating a silky-smooth combed top. Flick carders are typically used to open up the tips of locks of wool, preparing them for further carding.
For adventurous spinners interested in creating unique, textural yarns, a blending board offers a canvas to play with different fibers and colors before spinning. Lay out your chosen fibers across the board’s surface, and use the brush and dowel to create a roll of fiber, known as a rolags, ready to spin into yarn.
Each tool requires practice to master, but with patience, you’ll find fiber preparation not only improves your spinning but also expands your creative possibilities.
Blending Boards
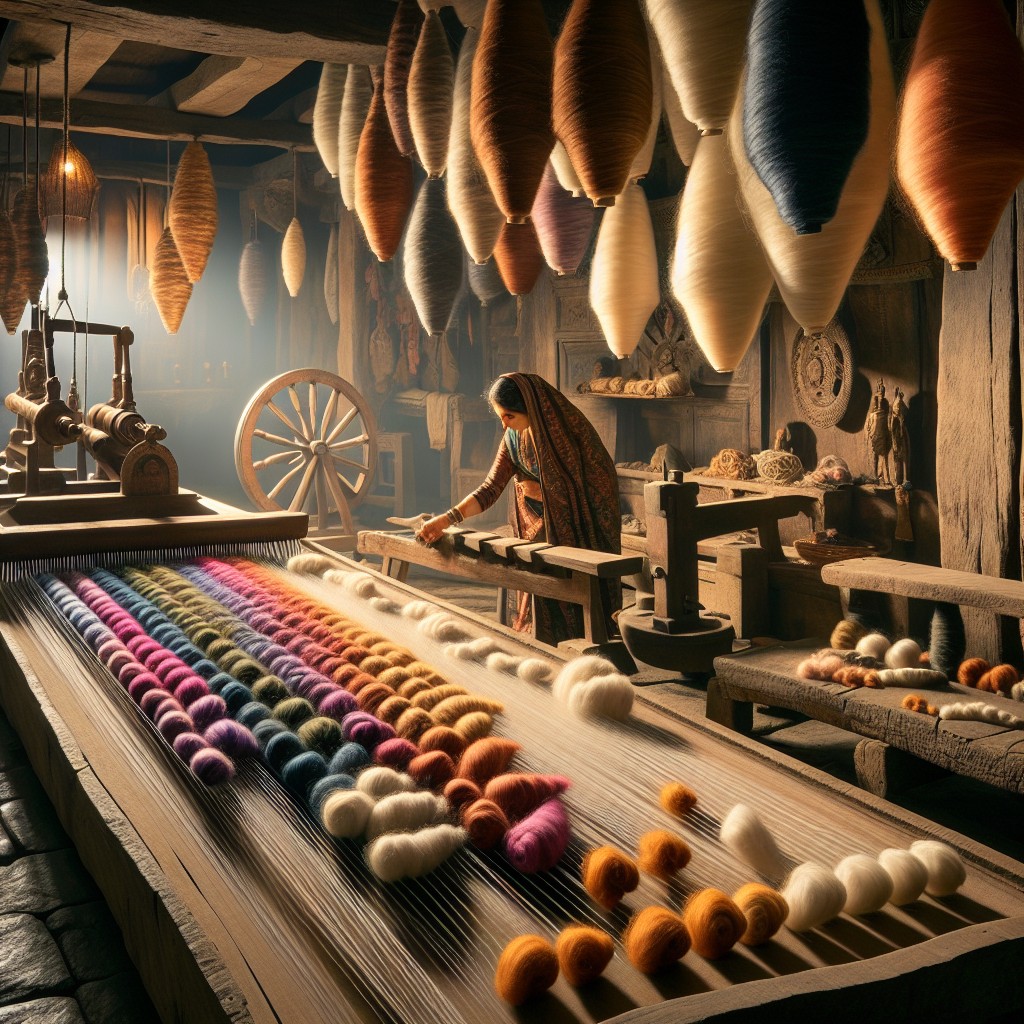
Blending boards are innovative tools designed for creating custom fiber blends and rolags for spinning. They consist of a flat surface with closely spaced teeth or pins. Here’s how they facilitate your creativity in yarn making:
1. Customization: By allowing you to mix different types, colors, and textures of fiber, you create unique blends that tailor to your spinning needs.
2. Control: You decide the ratio of each fiber, giving you complete command over the qualities of the finished yarn, from warmth and strength to elasticity and drape.
3. Versatility: Whether you want to experiment with exotic fibers or make use of leftover bits, blending boards handle a wide range of fibers.
4. Portability: Typically smaller and easier to store than drum carders, blending boards can be used on any flat surface and are great for fiber artists on the go.
Using a blending board is simple: Layer your chosen fibers onto the board, use the provided tools to integrate them, and then gently roll them off to create rolags, which are ready for spinning.
Hand Carders
To transform raw, tangled fleece into smooth, workable fibers, hand carders come into play. Shaped like paddles with fine, closely spaced wire teeth, they work by aligning the individual strands into a more uniform direction—a critical step for consistent spinning.
When using hand carders, start with small amounts of fleece. This prevents overloading the carders and makes the process easier. Place the wool on one carder and gently brush against the other, as though petting a cat, to avoid felting or damaging the fibers. With practice, you’ll develop a rhythm, transferring the fiber between the carders until it’s sufficiently aligned.
The resultant product is a “rolag” – a small, tube-like bundle of fiber – which is ideal for woolen spinning techniques, often preferred for their lofty, warm yarns. Occasionally cleaning the carders ensures longevity and a residue-free path for future projects.
Niddy Noddies
Niddy noddies are essential for spinners and knitters who create their own yarn. This simple hand tool serves to wind yarn into hanks after it has been spun. Typically made of wood or plastic, it consists of a central bar with crossbars at each end, which are offset by 90 degrees from each other.
Here’s how to effectively use this tool:
- Start by securing the yarn’s end to one of the crossbars with a simple knot.
- With a fluid, rhythmic motion, wrap the yarn diagonally around the opposite crossbars.
- Count your wraps; this will help you calculate the length of the yarn.
- Once completed, tie off the yarn in several places with figure-eight ties to keep everything in place.
- Slide the resulting hank off the niddy noddy, and it’s ready for washing, dyeing, or storing.
A standard sized niddy noddy will create a two-yard loop, but different sizes are available, enabling you to make hanks of various lengths. Compact and portable, the niddy noddy is an invaluable tool for organizing handspun yarn and preparing it for the final project.
Spinning Wheel Bobbins
Selecting the proper bobbin for your spinning wheel is essential to manage yarn capacity and tension control. Bigger bobbins can accommodate more yarn, which is ideal when spinning in bulk, whereas smaller bobbins are better suited for fine threads and delicate fibers.
Materials vary, with some crafted from wood for a traditional feel and others from plastic for affordability and ease of cleaning. It’s crucial to match the bobbin type to your spinning wheel brand and model, as compatibility ensures smooth operation.
Consider the type of yarn you plan to spin. For example, a high-speed bobbin is designed for spinning thin, high-twist yarns, while a jumbo bobbin is great for plying or for creating bulkier, art yarns.
Remember that having a collection of bobbins on hand can streamline your process. Plying requires at least two bobbins of single yarn, and without extra bobbins, you would need to wind off the yarn before you could continue spinning.
Bobbin maintenance is straightforward; keep them clean and free from oil and yarn build-up. On a regular basis, inspect for any cracks or damage that could snag or break the yarn during your spinning process.
Wool Breed Choices for Beginners
Selecting the right type of wool can significantly enhance the yarn making experience, especially for those new to spinning. Each breed of sheep produces wool with distinct characteristics that impact the feel, look, and usability of the finished yarn.
- Corriedale: Ideal for beginners, Corriedale fleece offers a favorable balance between softness and durability. Its medium staple length and crimp make it easy to spin, and it’s versatile for various projects.
- Merino: Known for its supreme softness, Merino wool is fine and can be more challenging to spin, but it is quite rewarding due to its luxurious finish, suitable for clothing worn close to the skin.
- Romney: A longwool variety, Romney is another excellent choice for those starting out. It has a longer staple length, which provides an easier grip for beginners learning to control the fiber.
- Blue Faced Leicester (BFL): BFL wool is soft with a nice luster and a longer staple, making it forgiving for new spinners and a joy to work with due to its silky nature.
- Shetland: Shetland wool ranges in softness but generally offers a good mix of manageability and softness for beginners, with its fine to medium staple making it a diverse choice for different spinning techniques.
Choosing wool from these breeds allows new spinners to practice and learn how various fibers respond to spinning without becoming frustrated by overly challenging materials. Each breed’s wool contributes uniquely to the yarn’s final texture and strength, allowing beginners to explore and find their preferred spinning experience.
Combed Top
Ideal for both beginner and advanced yarn makers, combed top is pre-processed fiber where short strands have been removed, leaving behind long, aligned fibers. This preparation results in a smoother, more uniform yarn, with fewer tendencies to pill.
When choosing combed top, consider:
- Fiber content: Wool is beginner-friendly, while luxury fibers like silk and cashmere offer a sumptuous feel.
- Staple length: Longer fibers are easier to spin and are a good starting point for novices.
- Color: Natural undyed options provide a blank canvas for dyeing, while pre-dyed tops add convenience to the spinning process.
Working with combed top also requires attention to drafting, the process of gently pulling and elongating the fibers before they are spun. Proper drafting ensures consistent thickness and prevents unwanted slubs in your finished yarn.
Maintenance Tools for Spinners
Routine maintenance ensures the longevity and performance of spinning wheels. To keep a spinning wheel in optimal condition, the following tools are essential:
- Oil and Oiler: Regular oiling of moving parts reduces friction and wear. A small bottle with a precise tip facilitates the application of oil to flyer bearings, wheel hinges, and treadle joints.
- Screwdrivers and Allen Wrenches: These are necessary for adjusting bolts and screws that may loosen over time. Keeping a set specific for your spinning wheel saves time during tuning sessions.
- Tension Gauges: Consistent spinning requires proper tension. A tension gauge helps calibrate brake bands and tension knobs to preferred settings for different types of yarn.
- Drive Bands: Having spare drive bands available prevents interrupted spinning sessions due to wear or breakage. These should be checked periodically for signs of stress.
- Cleaning Brushes or Cloths: Dust and fiber lint tend to accumulate in bobbin holders and flyer assemblies. Brushes designed for these areas, or soft cloths, help prevent buildup that can affect functionality.
Use these tools alongside the spinner’s manual to keep the equipment in top condition, ensuring a smooth spinning experience.
FAQ
What equipment is used to make yarn?
The equipment used to make yarn is commonly known as a spinning machine or a spinning wheel, with variants ranging from hand-cranked versions to modern industrial machines.
What do I need to make my own yarn?
To make your own yarn, you would need a spindle or wheel, a niddy-noddy, and a set of handcards.
What is used to spin yarn?
A spindle is used to spin yarn.
What device spins yarn?
A spinning wheel is a device utilized for creating thread or yarn from fibres.
Which types of fibers are best for yarn spinning at home?
Natural fibers such as wool, cotton, or flax are ideal for yarn spinning at home due to their manageability and forgiving attributes.
How does a spinning wheel function in the yarn making process?
A spinning wheel functions in the yarn making process by twisting the roving or raw fibers together, which adds strength and provides the desired texture to the end product.
What are the steps involved in hand spinning yarn?
Hand spinning yarn involves preparing the fibre, attaching the fibre to a spinning wheel or drop spindle, producing the spin to twist the fibre into yarn, and finally winding the spun yarn onto a bobbin or spindle.