Dive into the intriguing world of thread spinning wheels because understanding their diverse types and unique specifications can transform your yarn crafting experience.
Key takeaways:
- Spinning wheels align fibers for consistent thickness and twist.
- Different types of spinning wheels cater to specific spinning needs.
- Understanding the parts of a spinning wheel enhances the spinning experience.
- Mastering spinning techniques allows for a variety of yarn types.
- Fiber preparation is crucial for a smooth spinning process.
Function
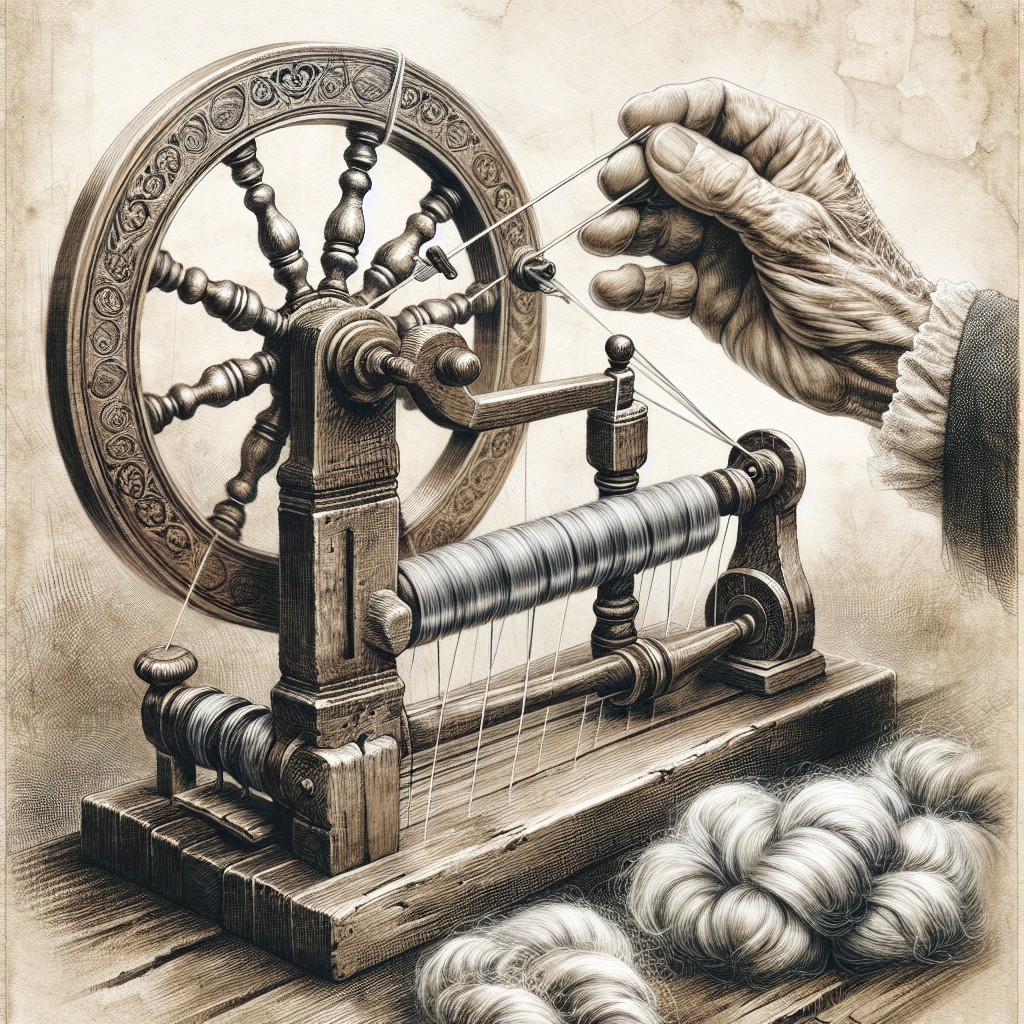
A spinning wheel transforms fiber into yarn or thread by twisting it together through a mechanical process. It enables a more efficient way of spinning than traditional hand-spindling methods.
At its core, the spinning wheel:
- 1. Aligns fibers to create a consistent thickness throughout the yarn.
- 2. Maintains a uniform twist, which gives the yarn strength.
- 3. Allows for continuous spinning, making the process faster than spindle spinning.
- 4. Provides adjustable tension, accommodating different types of fiber.
- 5. Facilitates control over yarn size and texture, from fine thread to chunky yarns.
- 6. Can be adjusted for the spinner’s comfort, including sitting or standing positions.
The simplicity of the process encourages spinners to create unique, hand-spun yarn for various projects, blending creativity with tradition.
History
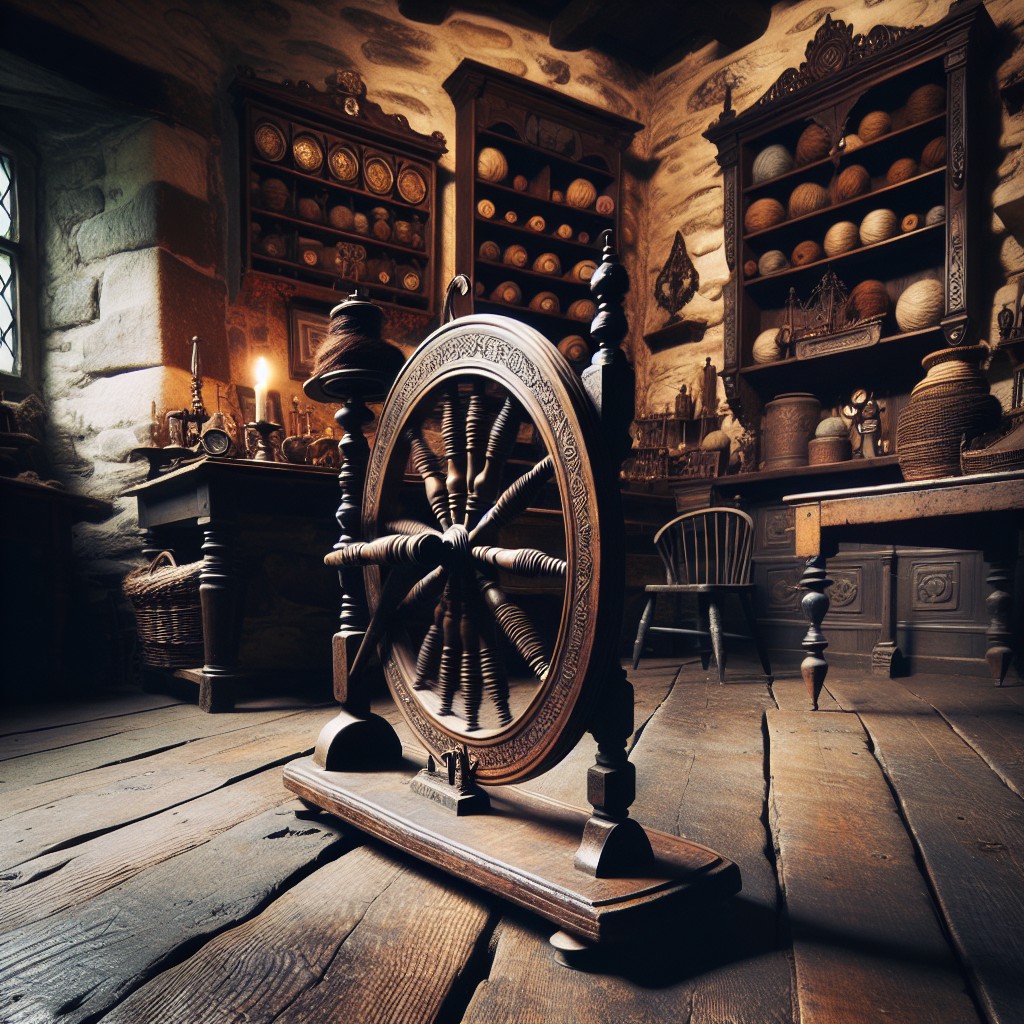
The spinning wheel’s evolution can be traced back to the Islamic world by the 11th century and later spread to Europe by the 13th century, revolutionizing textile production. Before its advent, spinning was performed using simpler tools like the spindle and distaff. A significant leap came with the invention of the treadle-operated spinning wheel in India, which allowed both of the spinner’s hands to be free to draft the fibers, which increased productivity.
With the advent of the Industrial Revolution in the 18th century, the spinning wheel was largely replaced in the industry by mechanized spinning frames, such as the Spinning Jenny and the water frame, which enabled mass production and contributed to the growth of the textile industry. Despite that, the traditional spinning wheel remains a cherished instrument for hand-spinners around the world, preserving a link to our artisanal past.
Types of Thread Spinning Wheels
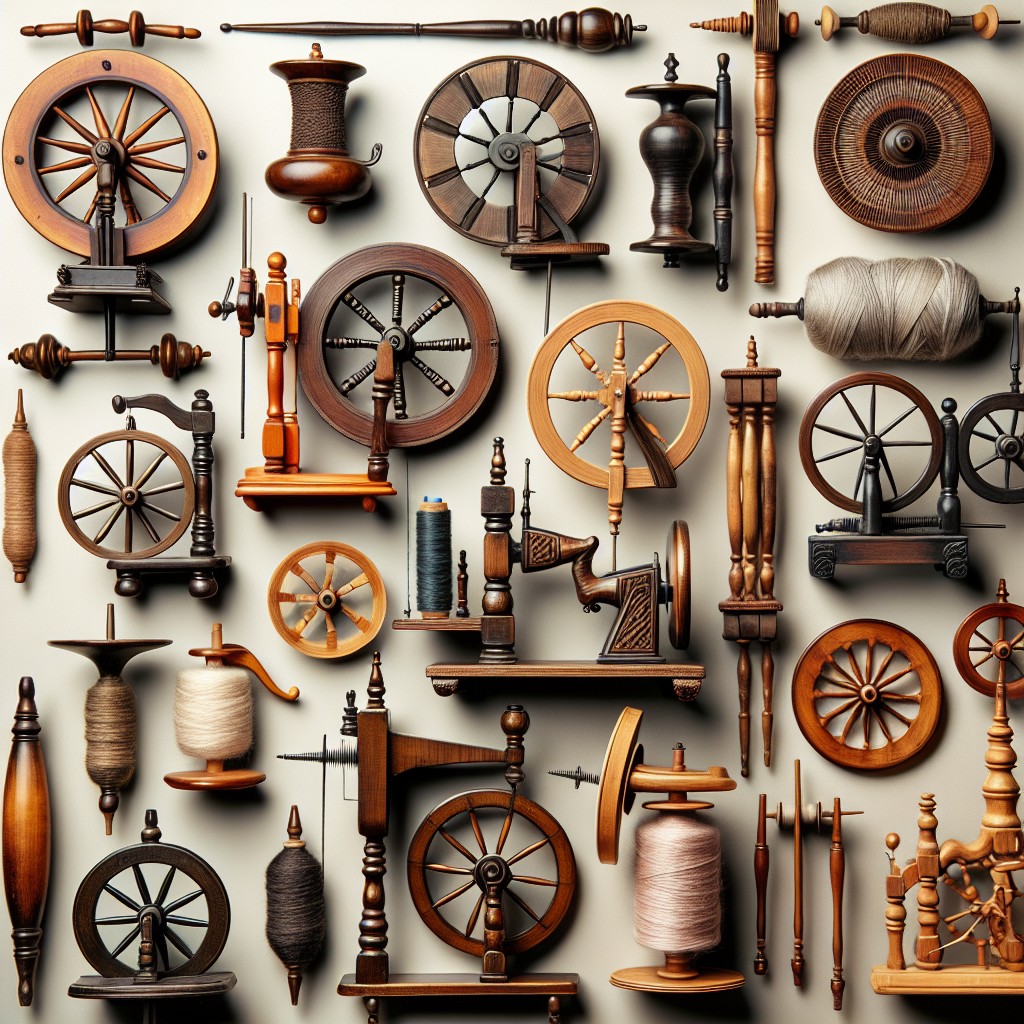
Saxony wheels, the traditional fairy-tale style design, feature a horizontal layout with the wheel at one end, and are prized for their beauty and historical appeal.
Castle wheels, known for their compact, vertical structure, are ideal for those with limited space. Despite their small footprint, they offer an efficient, comfortable spinning experience.
Modern spinning wheels have evolved to incorporate innovative features such as adjustable tensions, portability, and even electronic options, broadening the range of possibilities for contemporary yarn crafters.
Charkhas, a type of small, portable wheel originally from India, are typically used for spinning fine cotton and have gained global recognition thanks to Mahatma Gandhi, who promoted their use for self-sufficiency.
Great wheels, also known as walking wheels, demand a standing position to operate the large wheel, offering a rhythmic spinning process often associated with the production of woolen yarns.
Each type of wheel caters to specific spinning needs, including the kind of yarn being spun, the spinner’s comfort, the available space, and personal aesthetic preferences.
Parts of a Spinning Wheel
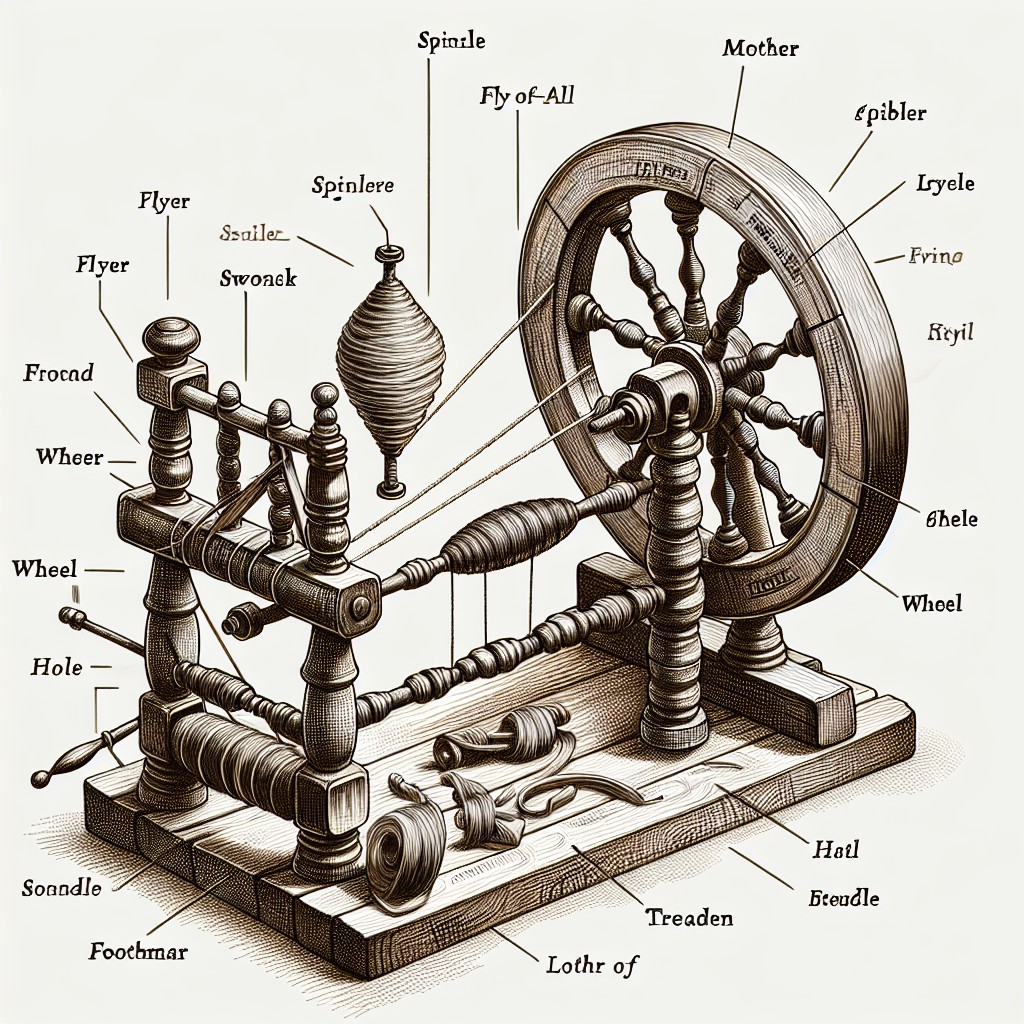
Understanding the component parts of a spinning wheel can greatly enhance your spinning experience. Here are key components you’ll encounter:
1. Flyer: This mechanism twists and winds the yarn onto the bobbin. It’s an essential part of ensuring consistent yarn thickness.
2. Bobbin: The bobbin holds the spun yarn. Most wheels come with several bobbins for multiple projects or yarn weights.
3. Drive band: A cord or belt that connects the wheel to the flyer or bobbin, transferring motion from the foot-powered treadle.
4. Treadle: The foot-operated pedal that drives the spinning wheel’s motion. Some models feature double treadles for a smoother action.
5. Maidens: These are the small vertical posts that hold the flyer and bobbin in place. Maidens can often be adjusted to manage tension and yarn thickness.
6. Mother-of-all: The part of the frame that holds the maidens and is responsible for tension adjustments, vital for consistent spinning.
7. Orifice: The small hole in the flyer through which yarn is threaded before it winds onto the bobbin, a crucial element for precise spinning.
8. Wheel: The large round part you manually spin or which is spun by the treadle, it’s the most recognizable and central feature of the spinning wheel.
9. Footman: This connects the treadle to the wheel. The footman’s efficiency determines how smoothly the wheel turns.
Familiarity with these components will facilitate troubleshooting and allow more control over yarn production. Remember to maintain these parts for the best spinning results.
Spinning Techniques
Mastering two primary spinning techniques—worsted and woolen—transforms raw fibers into distinct yarn types. The worsted method involves drafting fibers parallel to create smooth, strong yarn, suitable for durable items. In contrast, the woolen technique employs a carding process that aligns fibers in a web, resulting in airy, insulating yarn ideal for cozy knitwear.
Treadling speed and rhythm directly impact twist and yarn consistency. Beginners should practice achieving a steady pace to avoid over-twisting or under-twisting the yarn. Drafting, or the technique of pulling fibers from the mass to be spun, determines thickness. Short drafts produce fine yarns, while long drafts yield thicker varieties.
Plying is another vital technique, which combines two or more yarn strands to enhance strength and balance. Z-twists and S-twists refer to the yarn’s final direction of spin; alternating these in plied yarn can produce balanced, less likely to curl end-products.
Experimentation with different fibers and drafting techniques encourages personal style and yields a wide array of textures and yarn characteristics. Regardless of technique, maintaining relaxed hands and posture reduces fatigue during extended spinning sessions.
Fiber Preparation for Spinning
To ensure a smooth and successful spinning experience, properly preparing your fibers is essential. Begin by selecting the right type of fiber for your project, taking into account its staple length, crimp, and fineness. Wool, alpaca, cotton, and flax are popular choices, each offering unique properties.
Washing the raw fiber is the next step, which removes lanolin, dirt, and grease. This can enhance the fiber’s overall quality and make it easier to work with. After washing, drying the fiber completely is crucial before proceeding to avoid mildew.
Next, the fibers may need to be carded or combed. Carding aligns the fibers and removes any remaining impurities, creating a fluffy, homogenous batt or rolags ready for spinning. Combing, on the other hand, is suitable for longer fibers, aiming to align and parallelize them while separating out shorter lengths to achieve a more consistent yarn.
Drafting, or pulling fibers into a thinner strand before they are spun, is an essential step for controlling the thickness of the yarn you’re creating. Consider practicing this technique prior to actual spinning to develop a feel for maintaining an even tension.
To enhance spinning efficiency, predrafting can further align and stretch out the fibers. This reduces drafting effort during spinning and helps in achieving an even yarn.
Remember, the time invested in fiber preparation pays off with the quality of the final spun yarn. Carefully prepared fibers lead to a more enjoyable spinning process and a finished product with a consistent texture and strength.
Common Spinning Wheel Problems and Solutions
Treadle Trouble: If the treadle of your spinning wheel becomes stiff or unresponsive, it’s often due to a lack of lubrication or accumulation of dirt. Applying a few drops of oil to the hinges and moving parts can alleviate this issue.
Drive Band Slippage: When the drive band slips or doesn’t grip well, it could be stretched out or too loose. Replacing the band or adjusting the tension will usually fix the problem.
Skipped Drafting: Skipped drafting, where the yarn isn’t being drawn onto the bobbin smoothly, can occur if there’s uneven tension in the yarn or incorrect Scotch tension/bobbin-lead settings. Regular maintenance and careful adjustment of tension should help maintain smooth yarn flow.
Bobbin Woe: Bumpy or uneven winding on the bobbin could mean that the flyer hooks are not spaced correctly or the tension is inconsistent. Ensure that yarn is guided evenly across the bobbin and adjust the tension accordingly.
Unusual Noises: Squeaks and rattles may arise from loose parts or areas needing lubrication. Tighten any loose components and apply lubricant where necessary to resolve unwelcome sounds.
Fiber Snags: If your fiber is catching on the spinning wheel, it could be due to rough spots or burrs on the flyer hooks or orifice. Sanding these areas lightly with fine-grit sandpaper and smoothing them out should correct the problem.
Wheel Imbalance: A wobbly wheel may be due to an uneven surface or an actual imbalance in the wheel structure. Ensure the spinning wheel is on a flat surface; if the problem persists, check for loose spokes or other structural issues.
Maintaining your spinning wheel with these solutions will help ensure a pleasant and uninterrupted crafting experience. Regular cleanings and tune-ups are as important as the spinning itself to create beautiful, hand-spun yarn.
Guide to Buying a Spinning Wheel
When selecting a spinning wheel, consider the following points to find the ideal match for your crafting needs:
- Budget: Set a realistic price range, but remember that quality and longevity often correlate with a higher cost.
- Purpose: Determine if you’ll spin fine threads, chunky yarns, or a variety of textures, as different wheels are better suited to specific tasks.
- Type of Wheel: Decide between a traditional wheel with treadles, a modern electric spinner, or a portable design.
- Space: Assess your workspace and choose a model that fits comfortably, including consideration for storage.
- Comfort: Look for a wheel that accommodates your height and seating preferences to ensure ergonomic crafting sessions.
- Ease of Use: Beginners might prefer a wheel with straightforward mechanics, while experienced spinners might seek advanced features.
- Drive System: Understand the difference between single-drive and double-drive systems, as each offers a unique spinning experience.
- Construction Materials: A wheel made from durable materials like hardwood can be a lifetime investment, whereas composite or plastic wheels may offer a cost-effective alternative.
- Accessories: Verify what is included with your purchase, such as bobbins, lazy kates, or fiber starters, and what must be bought separately.
- Manufacturer Support: Ensure the manufacturer offers good customer service and availability of replacement parts.
- Community and Reviews: Seek out user reviews and recommendations from spinning communities, which can offer invaluable insight.
By carefully considering these factors, you’ll be better equipped to choose a spinning wheel that aligns with your preferences and enhances your yarn-crafting experience.
Culture and Tradition in Spinning
Spinning thread has deep roots across various cultures, often symbolizing the interconnectedness of life. Traditionally, the craft has passed down through generations, with skills and stories intertwined.
In some Asian regions, spinning is linked to spirituality and mindfulness; it’s a meditative practice. Many myths and legends feature spinning, like the tale of Arachne in Greek mythology or the spinning goddesses of the Bhutanese tradition.
Socially, spinning circles were common, fostering community bonds and allowing for the exchange of techniques among practitioners. These gatherings still occur today, with spinners sharing experiences and refining their craft collectively.
Spinning also marks important rites of passage in some societies. For instance, in some Native American tribes, learning to spin is a step towards adulthood.
Festivals and fairs often hold spinning contests to celebrate the skill, showcasing speed, consistency, and artistry in yarn creation.
By understanding these cultural nuances, spinners appreciate the craft beyond its practical application, honoring its rich historical tapestry.
Sustainable Practices in Thread Spinning
Embracing sustainable practices in thread spinning contributes positively to environmental conservation. Opt for natural fibers that require less chemical processing and water usage, such as organic cotton or hemp. Consider buying fibers locally to reduce carbon emissions associated with transportation. Furthermore, learn to prepare, dye, and finish fibers using natural, nontoxic substances to promote healthier ecosystems.
Upcycling plays a critical role in sustainability—spin yarn from old garments or textile waste, transforming what would be landfill material into valuable crafts. When spinning, be mindful of energy consumption. Use manual spinning wheels when possible to conserve electricity and enjoy the added physical activity. Implementing these measures not only helps protect the planet but also enriches the crafting experience with an eco-conscious perspective.
FAQ
What is the name of the spinning wheel with thread?
The name of the spinning wheel used to transform fibers into thread is called the Spindle wheel.
What is a thread wheel called?
In the context of turning fiber into thread or yarn, a thread wheel is commonly known as a spinning wheel.
What are the main components of a traditional spinning wheel?
The main components of a traditional spinning wheel are the drive wheel, spindle, distaff, maidens, bobbin, treadle, and footman.
How has the design of the thread spinning wheel evolved over time?
The design of the thread spinning wheel has evolved from a simple, hand-powered wooden mechanism in ancient times to contemporary electric and compact models with improved speed controls and multiple spinning options.
What is the process of spinning yarn on a wheel?
Spinning yarn on a wheel involves drafting (pulling apart) fibers to align them, attaching them to a leader on the spinning wheel, then using the wheel’s motion to twist the fibers into yarn.
Related Stories
- How to Use a Spinning Wheel: Comprehensive Instruction Guide
- Scotch Tension Spinning Wheel: An Informational Guide
- How to Make a Spinning Wheel for Yarn: A Comprehensive Guide
- Best Spinning Wheel for Beginners: Comprehensive Reviews and Comparisons
- Ashford Traditional Spinning Wheel Manual: Step-by-Step Instructional Guide