Dive into the world of yarn count systems as we unravel various types to help you understand and choose the perfect one for your textile projects.
Are you a yarn enthusiast, or just starting out in the world of knitting and crocheting? Either way, understanding the different types of yarn count systems is crucial to creating beautiful and functional projects. From lace weight to bulky weight, each type has its own unique characteristics that can affect the outcome of your work.
In this blog post, we’ll dive into the various yarn count systems and explore their differences so you can choose the perfect one for your next project. So grab your hooks and needles, let’s get started!
Types of Yarn Count in Textile
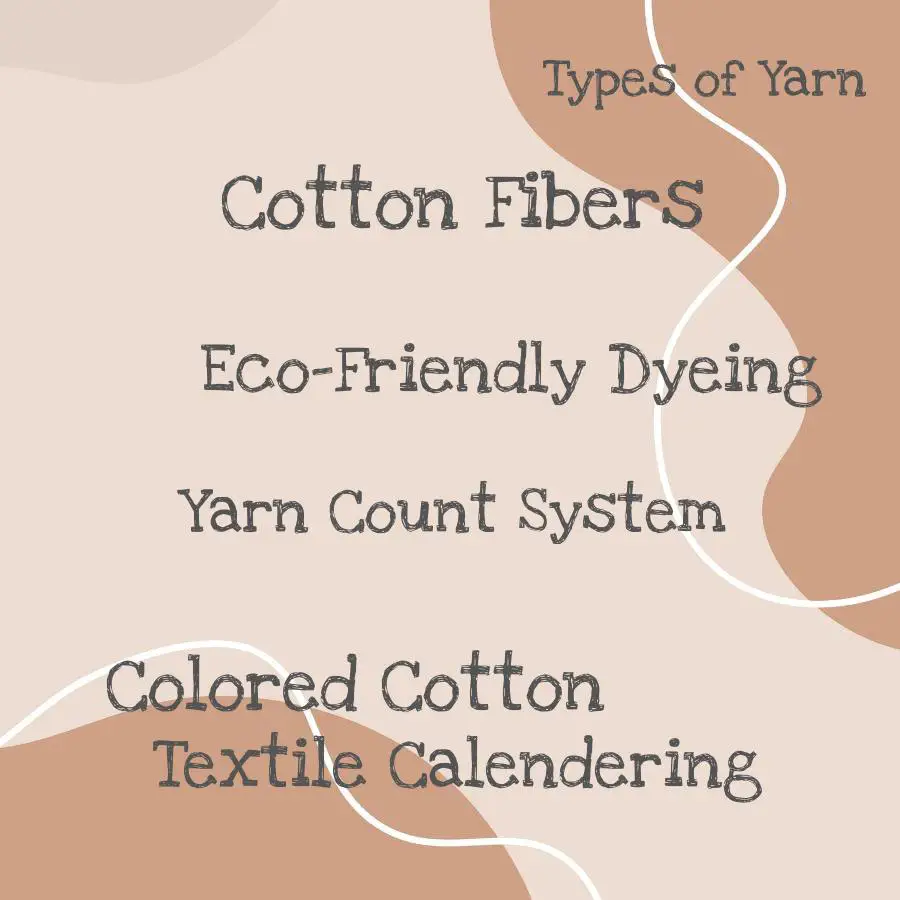
Yarn count is a crucial aspect of textile production, and it refers to the thickness or fineness of yarn. The type of yarn count system used in measuring the thickness or fineness varies depending on factors such as fiber type, end-use application, and manufacturing process.
In this section, we’ll explore some common types of yarn count systems used in textile production.
The most commonly used types are direct counting systems and indirect counting systems. Direct counting involves physically weighing a known length (usually one yard) of thread to determine its weight per unit length (such as grams per meter).
Indirect methods involve calculating the number of threads that can be placed within a specific area or volume.
Some examples include:.
- Denier: This is an indirect method that measures mass per unit length (grams per 9 kilometers).
- Tex: Another indirect method that measures mass per unit length but uses meters instead.
- Metric Count System: A direct system based on weight-per-length ratios using metric units.
- Understanding these different types will help you choose the right one for your project needs while ensuring consistency throughout your work.
Systems of Yarn Count Measurement
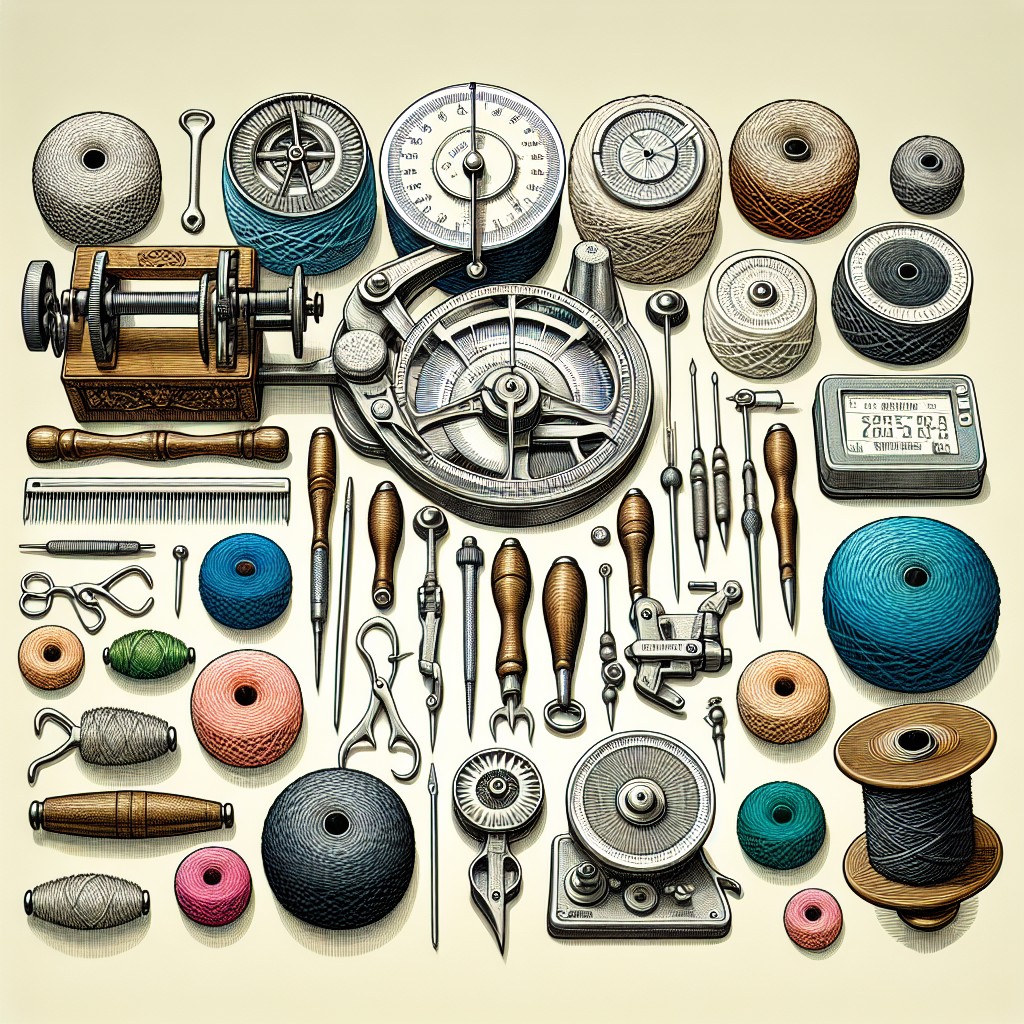
These systems help to determine the thickness and weight of a particular type of yarn, which is essential for creating high-quality textiles. The most commonly used systems include direct yarn count system, indirect or thread numbering system, and x-ray diffraction method.
The direct yarn count system measures the mass per unit length (usually in grams per meter) of a given length of yarn. This method is widely used for cotton and other staple fiber-based materials.
On the other hand, indirect or thread numbering system expresses linear density as a function of length rather than weight. It includes metric counts (numbering based on 1 km), denier (weight in grams per 9 km), tex (weight in grams per kilometer), etc.
Lastly, X-ray diffraction methods measure crystallinity index by analyzing crystal structure using X-rays that pass through fibers at different angles.
Direct Yarn Count System
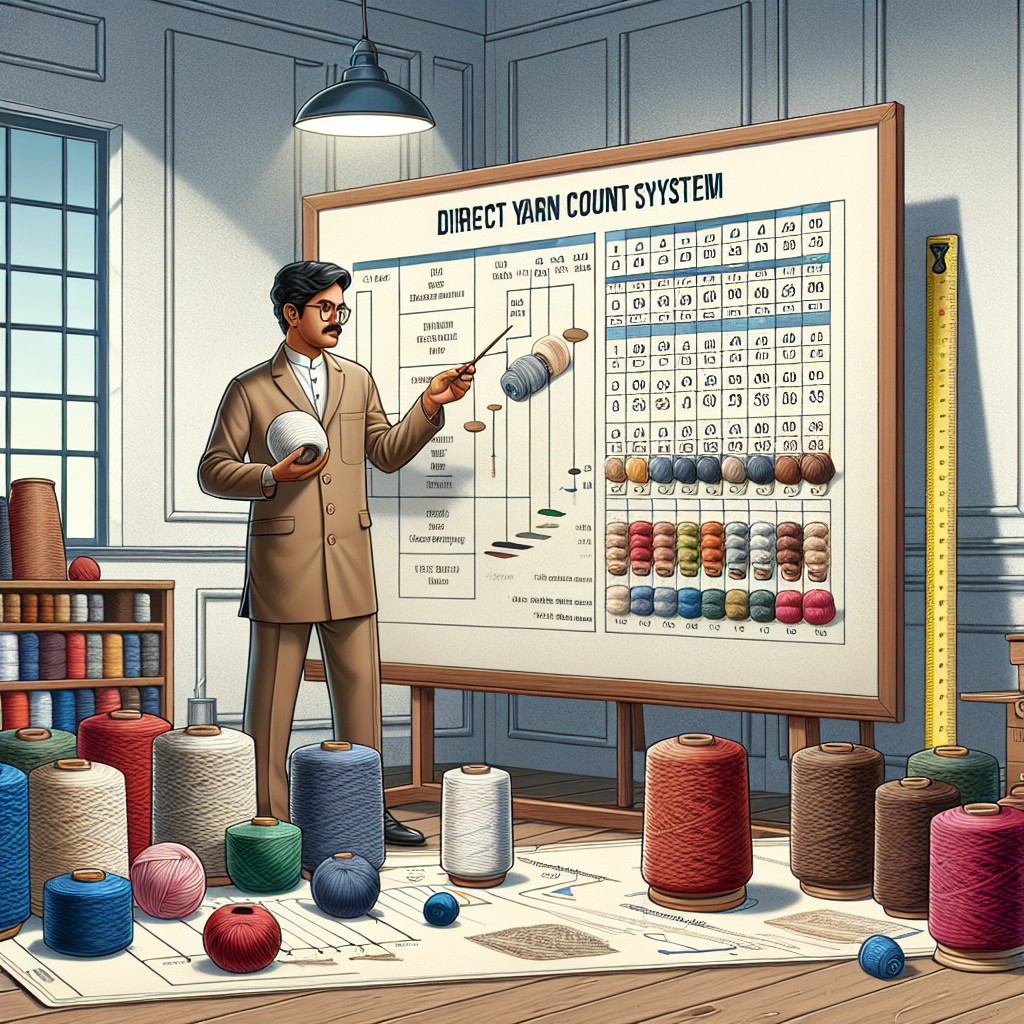
In this system, the weight per unit length (usually in meters) of a given amount of yarn is measured directly. The resulting number represents the count or thickness of that particular type and quality of yarn.
This method is particularly useful when working with natural fibers such as cotton, wool, silk, and linen because it provides an accurate measurement without having to take into account any variations in fiber diameter or density.
When choosing a direct counting system for your project, keep in mind that different materials may require different counts to achieve your desired results. For example, laceweight silk may require a higher count than bulky wool to create similar effects due to their inherent differences in texture and drape.
Thread Numbering System

It measures the weight of a thread by counting how many hanks (a length measurement) weigh one pound. The higher the number, the finer and lighter weight of yarn.
This system is widely used for cotton threads and other natural fibers such as linen or silk. However, it’s not suitable for synthetic fibers like polyester or nylon because they have different densities than natural fibers.
In this system, there are two types: direct and indirect numbering systems. In direct numbering, a higher number indicates a finer thread while in indirect numbering; lower numbers indicate finer threads.
Understanding these differences can help you choose which type to use based on your project needs. For example, if you’re making lacework that requires delicate details with fine stitches – then using a high numbered thread would be ideal since it will produce thinner strands that create intricate designs effortlessly.
X-ray Diffraction Method
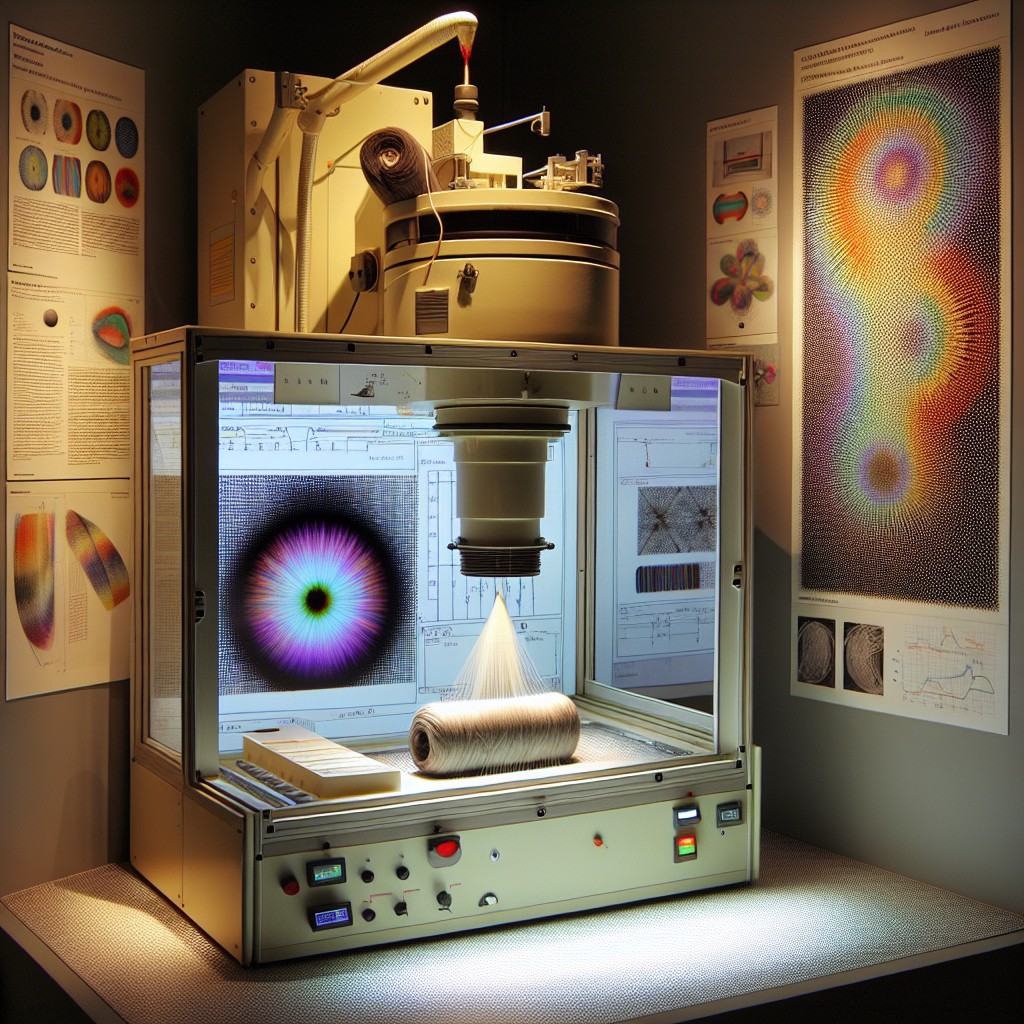
In textile manufacturing, this method is used to analyze the orientation and alignment of fibers in yarns. By analyzing the diffraction patterns produced by X-rays passing through a sample, researchers can gain insight into its molecular structure.
In terms of yarn count systems, X-ray diffraction can be particularly useful for determining fiber diameter and cross-sectional shape. This information can then be used to calculate direct yarn counts or other measurements related to thread density.
Length Parameters of Cotton Fibers
The length parameters are measured using various methods such as fiber fineness, staple strength, and uniformity index. These measurements help to determine how well cotton fibers will spin into yarns that are strong and durable.
Fiber fineness refers to the thickness or diameter of individual cotton fibers. It is measured by calculating micronaire value which ranges from 2-7 for matured cotton bolls.
Staple strength measures how much force it takes to break a single strand of fiber while uniformity index determines whether there’s consistency among different lengths within each sample.
Types of Calenders in Textiles
It involves passing the fabric between two or more rollers under high pressure and temperature. There are different types of calenders used in the textile industry depending on the desired finish for the fabric.
One type is a hot calender that uses heated rollers to produce a smooth surface on fabrics such as cotton, wool, silk or synthetic fibers like polyester. Another type is an embossing calender which creates patterns by pressing designs onto fabrics using engraved rollers.
A third type of calender commonly used in textiles is called a supercalander which produces an ultra-smooth finish by passing paper through multiple nips between hard polished steel rolls at high speeds.
Each type has its own unique characteristics that can affect both quality and production efficiency during manufacturing processes.
Industrial Problems During Calendering & Troubleshooting
However, like any other industrial process, calendering can be prone to problems that may affect the quality of finished products. Some common issues during calendering include uneven fabric thickness, wrinkles or creases on the surface of fabrics and poor adhesion between layers.
To troubleshoot these problems effectively, it’s essential first to identify their root causes. For instance, uneven fabric thickness could result from improper feeding or misalignment in rollers while wrinkles may occur due to insufficient tension control during processing.
Other factors such as temperature variations across different sections of machines and inadequate lubrication can also contribute significantly to these issues. Therefore regular maintenance checks are necessary for optimal performance.
Understanding potential industrial problems during calendering is crucial for ensuring high-quality textile production consistently.
Calendering: Factors Affecting Calendering
It involves passing fabric between two or more rollers under high pressure and temperature. The factors affecting calendering are numerous, including roller diameter, surface hardness, speed of rotation, temperature of the rollers and fabric tension.
Roller diameter plays an important role in determining the degree of compression applied to the fabric during calendering. Smaller diameters result in higher levels of compression while larger diameters produce less compression.
Surface hardness also affects calendering as harder surfaces can apply greater pressure on fabrics resulting in smoother finishes but may cause damage if too hard for delicate materials.
The speed at which rollers rotate determines how much time is spent compressing each section of material before moving onto another area; slower speeds allow for more thorough treatment but take longer overall than faster ones do.
Calendering Machine Construction
The calendering machine plays an essential role in this process, as it applies pressure and heat to the fabric, resulting in a smoother surface. The construction of these machines varies depending on their intended use.
The basic structure of a calendering machine consists of two or more rollers that rotate at different speeds. These rollers are made from materials such as steel or rubber and can be heated using steam or electricity.
Some machines also have additional features like cooling systems for temperature control.
There are various types of calenders available based on their construction, including three-roll, four-roll, five-roll calenders among others. Three-roller Calenders consist of three rolls arranged vertically with one roll placed between two other rolls which rotates at different speeds than the other two.
Four-roller Calendars have four rolls arranged horizontally where both top & bottom roller rotates at same speed while middle 2 rollers rotate faster than them Five-Roller calendars include an extra roller called “Nip Roller” which helps maintain uniformity during calendaring.
Naturally Colored Cotton
Unlike traditional white cotton, naturally colored cotton does not require any dyeing or bleaching processes to achieve its color. This makes it an eco-friendly option for textile production.
The colors of naturally colored cotton are determined by the genetics of the plant and can range from light tan to dark chocolate brown. The fibers are also known for their softness and durability, making them ideal for clothing items such as t-shirts and socks.
In recent years, there has been a growing interest in using naturally colored cotton as an alternative to conventionally grown white or dyed fabrics due to its sustainability benefits. By choosing this type of fabric over conventional options that require chemical processing during manufacturing stages like dyeing or bleaching; you’re reducing your carbon footprint while supporting sustainable agriculture practices.
Zein Fibre
It is made from corn protein, which makes it an eco-friendly alternative to traditional synthetic fibres. Zein fibre has many unique properties that make it ideal for use in clothing and other textiles.
For example, it is naturally water-resistant and can be easily dyed with natural dyes.
One of the most significant advantages of zein fibre over other types of yarns is its biodegradability. Unlike synthetic fibres such as polyester or nylon, zein fibre will break down naturally over time without harming the environment.
Another advantage of using zein fiber in textiles production lies in its hypoallergenic nature; this means that people who are allergic to wool or other animal fibers can wear clothes made from this material without any adverse reactions.
Groundnut Fibre
It is derived from the shells of groundnuts, which are usually discarded as waste after harvest. The fibre has unique properties that make it suitable for use in textiles, such as its strength and durability.
In recent years, there has been an increased interest in using sustainable materials in textile production due to environmental concerns. Groundnut fibre offers a viable solution by providing an eco-friendly option that can be used for various applications such as clothing, bags and home decor items.
The process of extracting groundnut fibre involves crushing the shells into small pieces before separating them from other debris through winnowing or sieving. The resulting fibres are then washed thoroughly before being spun into yarns or woven directly into fabrics.
One advantage of using groundnut fiber is its low cost compared to other natural fibers like cotton or wool since it’s obtained from agricultural waste products that would otherwise go unused. Moreover, this material also provides income opportunities for farmers who can sell their peanut shell wastes instead of burning them off on fields contributing towards air pollution.
Surgical Gowns Using SMMMS Method
The SMMMS (Spunbond-Meltblown-Meltblown-Spunbond) method is a popular technique used to manufacture surgical gowns due to its superior barrier properties. This method involves the use of multiple layers of non-woven fabric that are bonded together using heat and pressure.
The outer layer is made from spun-bonded polypropylene, which provides strength and durability while also repelling fluids. The inner layers consist of melt-blown polypropylene fibers that act as filters for bacteria and other contaminants.
Using the SMMMS method ensures that surgical gowns meet stringent safety standards while providing comfort for healthcare workers during long procedures. These high-quality garments offer excellent protection against bloodborne pathogens, bodily fluids, chemicals, and other hazardous materials commonly encountered in medical settings.
Gearing Calculation of Tappet Loom
However, calculating the gearing ratio for a tappet loom can be tricky. The gearing ratio determines how many times the crankshaft must rotate to complete one cycle of shedding and picking.
This calculation is essential in ensuring that your fabric has an even weave structure.
To calculate the gearing ratio, you need to know several factors such as cam pitch circle diameter (PCD), number of teeth on each gear wheel, and pick density per inch or centimeter. Once you have these values at hand, you can use them in various formulas depending on your specific needs.
It’s important to note that incorrect calculations could lead to uneven tension across your fabric or even breakage during weaving. Therefore it’s crucial always double-checking all measurements before starting any project with a tappet loom.
Eco-Friendly Textile Dyeing Process
That’s where eco-friendly dyeing processes come in. Traditional textile dyeing methods can be harmful to both human health and the environment due to their use of toxic chemicals and large amounts of water.
However, with advancements in technology, there are now more sustainable options available.
Eco-friendly textile dyeing processes utilize natural dyes made from plants or other organic materials that do not contain harmful chemicals or toxins. These dyes are biodegradable and do not pollute water sources like traditional synthetic dyes.
In addition to using natural dyes, eco-friendly dyeing also involves reducing water usage by implementing closed-loop systems that recycle wastewater back into production instead of releasing it into rivers or oceans.
Lab-dip Preparation in Textile Industry
This process helps manufacturers save time and resources by ensuring they achieve their desired color before starting mass production.
To prepare lab-dips, textile professionals use various equipment such as scales, beakers, pipettes, and hot plates. They also follow strict guidelines to ensure accuracy in measurements and consistency in results.
The process starts with selecting the right dyes based on factors such as fiber type, end-use application of fabric or garment being produced.
Once selected dyes are weighed accurately using digital scales; then mixed into a solution using distilled water at specific temperatures depending on dye types used. After mixing thoroughly until all lumps dissolve completely; it’s poured onto pre-weighed fabrics swatches placed inside beakers or jars containing this mixture.
The swatches are left to soak for some time before rinsing them off under running water until no excess dye remains visible on them anymore – this ensures that only colors which have been absorbed by fibers remain intact while others get washed away during rinsing phase itself!.
FAQ
What is the system of yarn count?
The system of yarn count consists of the direct system (N = (W/l) / (L/w)) and the indirect system (N = (L/w) / (W/l)), where N represents yarn count, W represents weight, l represents the unit of length, L represents the length of the sample, and w represents the unit of weight.
How many types of count system is used in textile?
There are two types of count systems used in textile: Direct system and Indirect system.
What is the tex and Denier count system?
The tex and Denier count system are indirect systems of measuring yarn, where tex represents the weight in grams of 1,000 meters of yarn and denier represents the weight in grams of 9,000 meters of yarn, both having a constant weight and variable length.
Which yarn count is best?
The best yarn count is above 140, as it provides adequate softness to the touch.
What are the differences between direct and indirect yarn count systems?
Direct yarn count systems express yarn thickness as mass per unit length, while indirect yarn count systems express it as length per unit mass.
How does the yarn count system affect textile quality and production?
The yarn count system affects textile quality and production by determining the fineness or thickness of the yarn, which impacts the fabric’s strength, softness, and overall appearance.
What factors should be considered when selecting the appropriate yarn count for a textile project?
When selecting the appropriate yarn count for a textile project, consider factors such as fabric strength, thickness, colorfastness, desired texture, and performance requirements.