Discover the fascinating world of yarn dyeing machines as we delve into the various types and their unique capabilities in transforming textiles with vibrant colors and patterns.
Are you a yarn enthusiast who loves experimenting with different colors and textures? If so, you may have heard about yarn dyeing machines. These machines are used to dye yarn in various shades and hues, making them an essential tool for any crafter or textile manufacturer.
But did you know that there are different types of yarn dyeing machines available in the market? Each machine has its own unique features and advantages, which can make the process of selecting one a bit overwhelming. In this article, we’ll take a closer look at the different types of yarn dyeing machines and what sets them apart from each other.
So grab your cup of tea, sit back, and let’s explore the wonderful world of yarn dyeing machines!
Jet Dyeing Machine
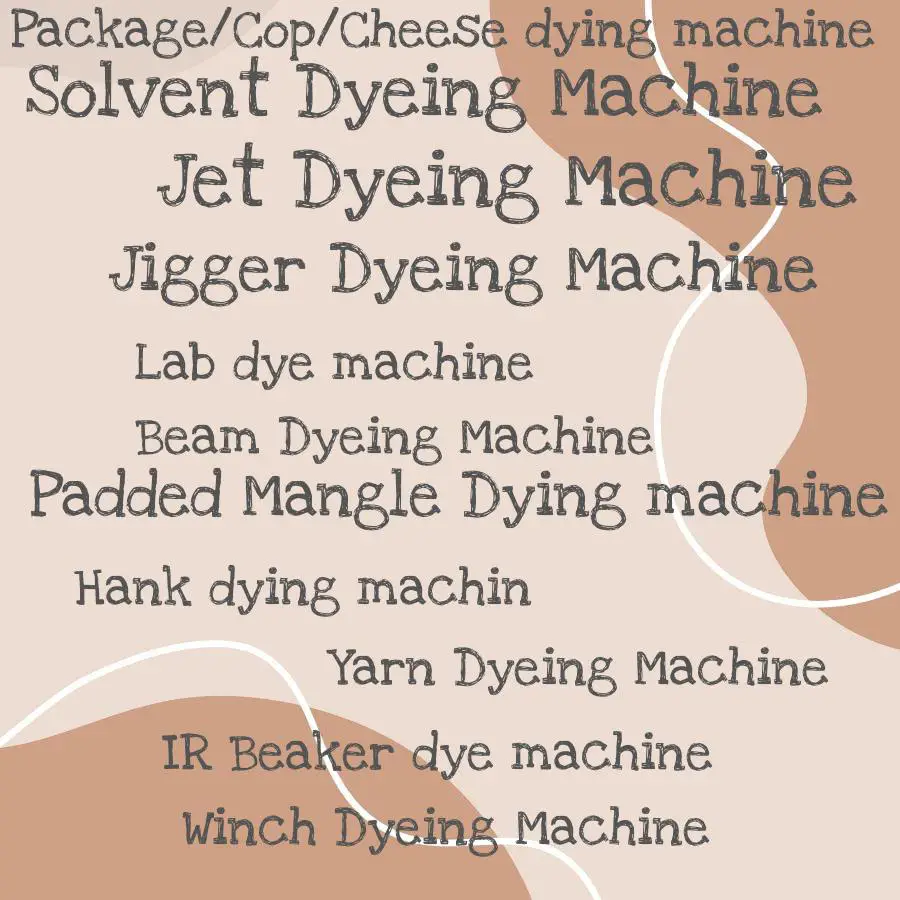
Jet Dyeing Machine is a high-speed machine that uses the principle of circulating dye liquor through the yarn package. The machine has an efficient nozzle system that ensures even distribution of dye liquor throughout the yarn package, resulting in uniform coloration.
Jet Dyeing Machines are suitable for processing synthetic and natural fibers such as cotton, wool, silk, polyester among others.
One advantage of using Jet Dyeing Machines is their ability to reduce water consumption during operation compared to other types of machines. This makes them environmentally friendly and cost-effective for textile manufacturers who want to minimize their carbon footprint while maximizing profits.
Another benefit is its fast processing time due to its high speed which enables it to handle large quantities within a short period without compromising on quality or consistency.
Winch Dyeing Machine
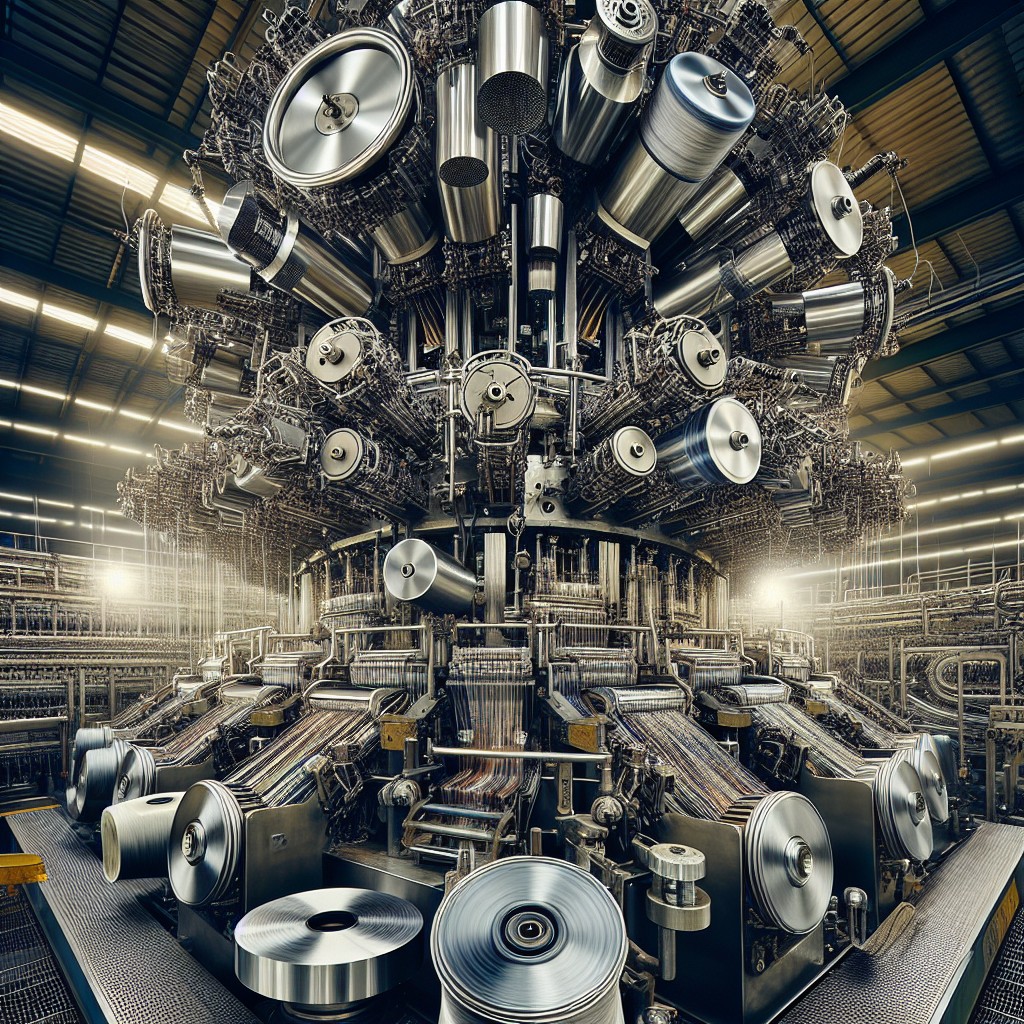
This machine is ideal for processing delicate and fragile fibers, as it allows for gentle handling during the dyeing process. The winch system ensures that each strand of yarn receives an even distribution of color, resulting in consistent and vibrant hues.
One advantage of using a Winch Dyeing Machine is its versatility in handling different types of fibers such as cotton, wool, silk or synthetic materials like polyester or nylon. It can also handle various forms such as hanks or cones.
Another benefit is its ability to accommodate small batch sizes which makes it perfect for testing new colors before scaling up production on larger machines.
However, one disadvantage with this type of machine compared to others like Jet Dyeing Machines would be longer processing times due to slower speed rates which may not be suitable when dealing with large quantities.
Beam Dyeing Machine
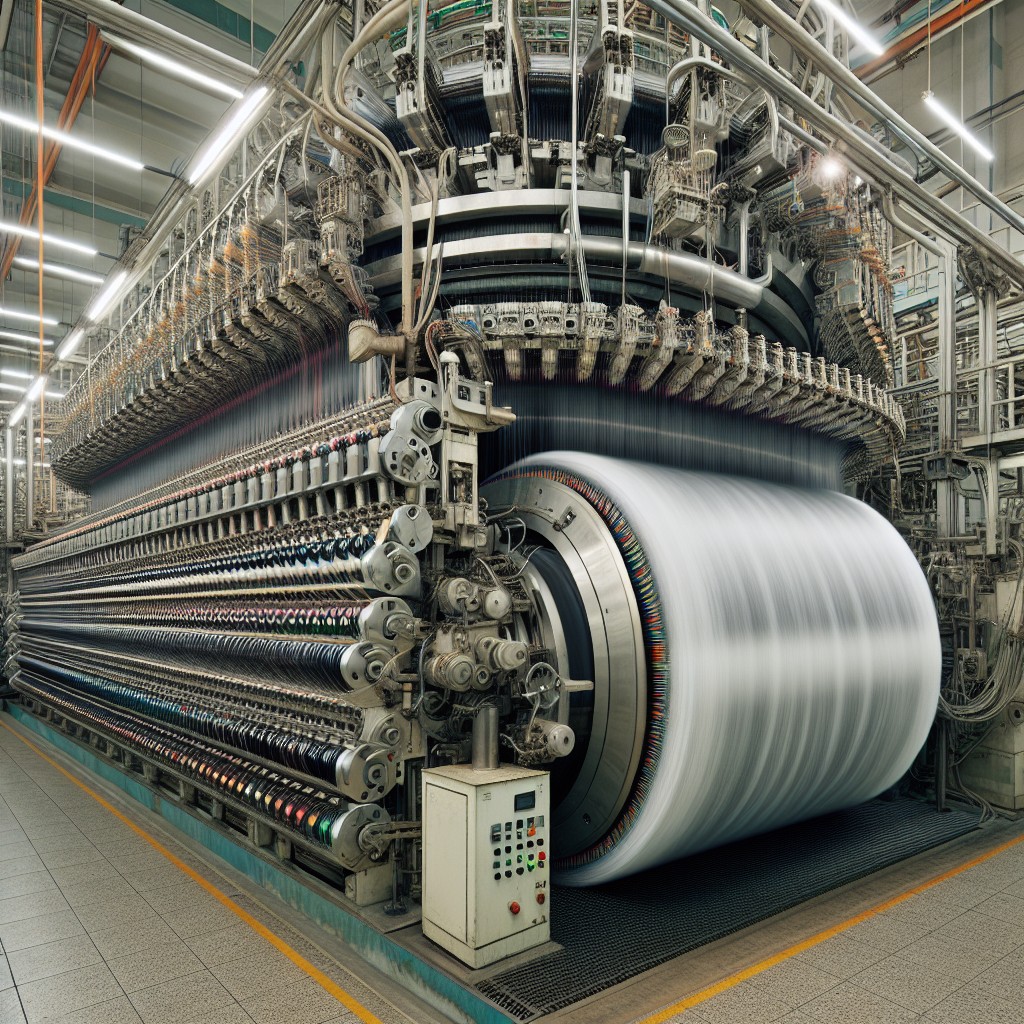
The beam can be made of metal or plastic and is designed to withstand high temperatures and pressures. This type of machine is commonly used for dyeing large quantities of yarn at once, making it ideal for textile manufacturers.
The Beam Dyeing Machine works by loading the yarn onto the beam, which then rotates slowly in a circular motion while being submerged in hot water containing dyes. The temperature and pressure are carefully controlled throughout the process to ensure even distribution of color on every strand.
One advantage of using this type of machine is that it allows for precise control over various parameters such as temperature, pressure, speed, etc., resulting in consistent quality output with minimal defects. Since beams can hold more than one package at once (up to 1000 kg), they are highly efficient when dealing with large volumes.
Jigger Dyeing Machine
It is mainly used for dyeing fabrics such as cotton, polyester, and blended fabrics. The jigger machine operates by passing the fabric through a series of rollers that squeeze out excess water and apply pressure to ensure even color distribution.
One of the advantages of using jigger machines is their ability to handle large quantities of fabric at once, making them ideal for bulk production. They are known for their high efficiency in achieving consistent color results with minimal wastage.
However, it’s important to note that jigger machines require skilled operators who can adjust various parameters such as temperature and pressure levels based on different types of fabrics being dyed. Improper adjustments can lead to uneven coloring or damage to the fabric.
Solvent Dyeing Machine
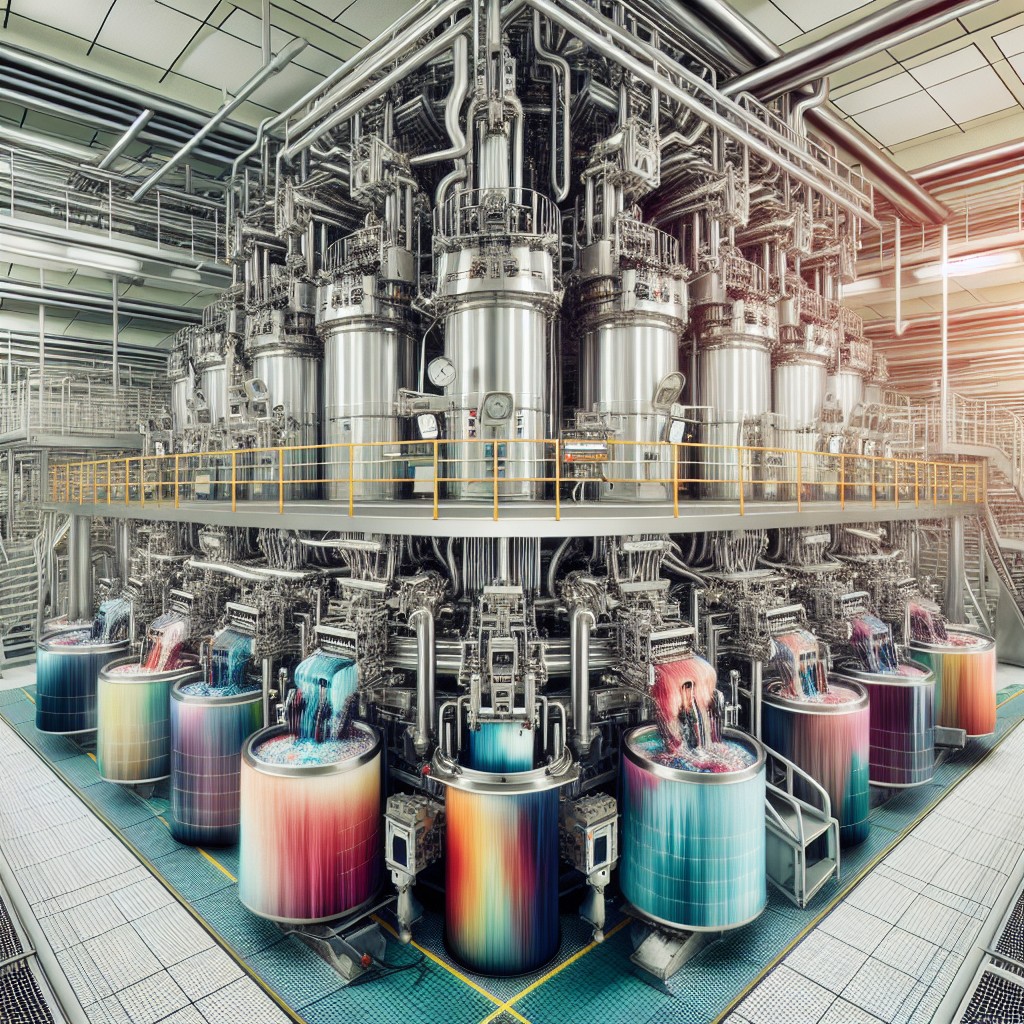
This method is particularly useful for synthetic fibers such as polyester, which are difficult to color using traditional water-based methods. Solvent dyeing machines use organic solvents like acetone or methanol, which can penetrate the fiber more easily than water-based dyes.
One advantage of solvent dyeing machines is that they require less energy and time compared to other types of yarn-dyeing machines. The process also produces less wastewater since there’s no need for rinses after the dying process.
However, it’s important to note that solvent dyes have some disadvantages too; they tend not be as environmentally friendly due to their chemical composition and may pose health risks if not handled properly during operation.
Padded Mangle Dyeing Machine
It works by passing the fabric through a series of rollers, which apply pressure to ensure even distribution of the dye or finish. The padding process also helps to improve color fastness and reduce creasing in the finished product.
One advantage of using a padded mangle machine is its ability to handle delicate fabrics such as silk, wool, and cotton without causing damage or distortion. This makes it an ideal choice for high-end fashion designers who require precise color matching on their fabrics.
Another benefit is its efficiency in handling large quantities of fabric at once while maintaining consistent quality throughout each batch. This saves time and reduces production costs compared to other methods that may require multiple runs through different machines.
However, like any machinery, there are some limitations with this type of equipment as well. For instance, it may not be suitable for certain types of synthetic fibers due to their low absorbency rate or sensitivity towards heat during processing.
IR Beaker Dyeing Machine
This method allows for precise temperature control and uniform heating, resulting in consistent and accurate dyeing results. The machine can accommodate multiple beakers at once, making it ideal for small-scale production or research purposes.
One advantage of using an IR Beaker Dyeing Machine is its ability to save time and energy compared to traditional methods such as stove-top heating. This type of machine requires minimal maintenance due to its simple design.
However, it’s important to note that while an IR Beaker Dyeing Machine offers many benefits in terms of efficiency and accuracy, it may not be suitable for larger-scale production due to its limited capacity. As with any machinery used in textile manufacturing processes, proper training on safety protocols should also be observed when operating this equipment.
Jigger Lab Dyeing Machine
It works by passing the yarn or fabric through a series of rollers, which are immersed in the dye bath. The rollers then squeeze out excess water and evenly distribute the dye onto the material.
One advantage of using Jigger Lab Dyeing Machines is their ability to produce consistent results with minimal variation between batches. This makes them ideal for testing new dyes or color combinations before scaling up to larger production runs.
Another benefit of Jigger Lab Dyeing Machines is their versatility, as they can be used to dye various types of materials such as cotton, wool, silk and synthetic fibers.
However, it’s important to note that this type of machine requires careful monitoring during operation since any deviation from recommended settings could result in uneven coloring or damage to delicate fabrics.
Oscillating Lab Dyeing Machine
This machine works by immersing the sample in a bath of hot water and dye solution while simultaneously agitating it with an oscillating motion. The agitation helps to ensure even distribution of the dye throughout the sample.
One advantage of using an oscillating lab dyeing machine is its ability to produce consistent results on small samples. This makes it ideal for testing new color formulations or experimenting with different types of dyes without having to use large quantities of materials.
Another benefit is that this type of machine requires less water and energy compared to other types such as jet or beam machines, making it more environmentally friendly.
However, one downside is that due to its smaller size and capacity limitations, larger production runs may not be feasible on this type of equipment.
Package/Cop/Cheese Dyeing Machine
This machine can handle large quantities of yarn at once, making it an ideal choice for manufacturers who need to produce high volumes of dyed yarn quickly and efficiently.
The Package/Cop/Cheese Dyeing Machine works by winding the yarn onto a cylindrical package or cone-shaped cheese before immersing it into the dye bath. The packages are then loaded onto spindles inside the dye vessel, which rotates slowly to ensure even distribution of color throughout each package.
One advantage of this type of machine is its versatility – it can be used with various types and sizes of packages depending on specific production needs. Some models come equipped with features such as automatic dosing systems and programmable controls that allow for precise control over temperature, pressure, and other variables during the dye process.
Package/Cop/Cheese Dyeing Machines offer an efficient solution for producing large quantities of dyed yarn while maintaining consistent quality standards.
Hank Dyeing Machine
These machines use a series of tanks filled with water and dye to immerse the hanks in the solution. The process involves soaking the hanks in hot water and then adding dyes to achieve desired colors.
One advantage of using a Hank Dyeing Machine is that it allows for even distribution of color throughout each individual strand, resulting in consistent coloring across all strands. This makes it an ideal choice for those who want their finished product to have uniformity.
Another benefit is its ability to handle delicate fibers such as silk or wool without causing damage or tangling during the process. This machine has low energy consumption compared with other types making it more environmentally friendly.
Warp Dyeing Machine
The machine is equipped with a creel, which holds the warp yarns in place while they are being dyed. The warp threads pass through a series of rollers and guides before entering the dye bath, where they absorb the color.
One of the advantages of using a warp dyeing machine is that it allows for precise control over color placement on each individual thread. This can be especially useful when creating complex patterns or designs in woven fabrics.
There are several types of warp dyeing machines available, including those that use high-pressure jets to force water and dyes into the fibers and those that rely on immersion techniques to achieve even coverage.
Continuous Loose Stock Dyeing Machine
This machine operates continuously and can handle large quantities of fiber at once. The continuous process ensures uniform color distribution throughout the fibers.
The Continuous Loose Stock Dyeing Machine works by feeding the loose stock into a chamber where it undergoes various stages of treatment before being dyed. The fiber passes through several compartments where it is pre-treated with chemicals to remove impurities and prepare it for dyeing.
Once the pre-treatment stage is complete, the fiber moves on to be dyed in another compartment using high-pressure jets that ensure even penetration of color throughout each strand. Afterward, excess water from rinsing gets removed via centrifugal force before drying takes place.
Discontinuous Loose Stock Dyeing Machine
This machine operates in batches, which means that the fibers are dyed in small quantities at a time. The process involves loading the loose stock into perforated baskets and then immersing them into the dye bath for a specific period of time.
One advantage of using this type of machine is its flexibility when it comes to handling different types and qualities of fibers. It can handle delicate natural fibers like silk, wool, and cashmere without causing damage or breakage during processing.
Another benefit is its ability to produce consistent color results with minimal variation between batches due to precise temperature control throughout each cycle.
However, one downside could be longer processing times compared to other machines due to batch-wise operation. Also, there may be limitations on how much material can be processed per batch depending on basket size capacity.
Fabric Dyeing Machine
These machines can handle a wide range of fabrics, including cotton, silk, wool and synthetic materials. The process involves loading the fabric onto rollers or beams that move through the machine while being submerged in a vat of hot water and dye solution.
One advantage of using a fabric dyeing machine is that it allows for consistent color throughout the entire batch. This is especially important for textile manufacturers who need to produce large quantities of uniform colored fabrics.
There are different types of fabric dyeing machines available on the market today such as beam dyers which use high-pressure jets to force water and chemicals into tightly wound rolls or beams; jigger dyers which involve passing cloth over two rollers immersed in vats containing dyes; pad-batch systems where material passes through several stages before being rinsed out with fresh water after each stage etc.
Lab Dyeing Machine
It is designed for testing and developing new colors, shades, and patterns on a smaller scale before moving to mass production. Lab dyeing machines are also useful for research purposes as they allow scientists to study the effects of different dyes and chemicals on textiles.
One advantage of using lab dyeing machines is that they require less water, energy, and raw materials compared to their larger counterparts. This makes them more cost-effective while reducing waste in the process.
Another benefit of using lab dyeing machines is that they offer greater flexibility when it comes to experimenting with different types of fibers such as wool or silk. They can also be used for yarns or fabrics made from natural or synthetic materials.
Yarn Dyeing Machine
It can be used for both natural and synthetic fibers, including wool, cotton, silk, polyester and more. Yarn dyeing machines come in different sizes and shapes depending on the volume of yarn to be dyed.
One popular type of yarn dyeing machine is the Jet Dyeing Machine which uses high-pressure jets to force water through the fabric or fiber being dyed. This method ensures even distribution of color throughout the material while minimizing waste.
Another common type is Winch Dyeing Machine which involves immersing skeins or hanks into a vat filled with hot water mixed with dyes. The winch then rotates slowly ensuring that all parts are evenly exposed to heat and color.
Beam Dye Machines are also widely used in textile industries as they allow for large quantities of fabric or fiber to be processed at once by winding them onto beams before being immersed into vats containing dyes.
Fiber Dyeing Machine
This machine can be used for both small-scale and large-scale production. The process involves immersing the fibers in a solution containing the desired colorant under controlled conditions of temperature and pressure.
The fiber dyeing machines come in different types depending on their design features. Some common types include jet dyeing machines, beam dyeing machines, winch/ jigger/ paddle dyers among others.
Jet Dye Machines are suitable for high-speed processing with low liquor ratios while Beam Dye Machines are ideal for handling delicate fabrics that require gentle treatment during processing.
Winch/Jigger/Paddle Dyers use an open bath system where fabric moves through the dyebath by means of rollers or paddles while immersed in hot water containing dyes.
Types of Dyeing and Finishing Defects
These defects can range from minor issues such as uneven color distribution to more severe problems like fabric damage or shrinkage. Some common types of dyeing and finishing defects include bleeding, fading, staining, pilling, snagging, and creasing.
Bleeding occurs when excess dye is not properly removed from the fabric during washing or rinsing. This results in color transfer onto other fabrics or surfaces.
Fading happens when dyes lose their intensity over time due to exposure to sunlight or harsh chemicals.
Staining occurs when foreign substances come into contact with the textile surface causing discoloration that cannot be removed by normal washing methods.
Pilling refers to small balls of fiber forming on the surface of a textile after repeated use/washing cycles which makes it look old and worn out quickly than expected.
Snagging is caused by sharp objects catching on fibers resulting in pulled threads which may lead eventually lead holes being formed.
Creasing happens due improper folding/storage techniques leading permanent wrinkles/markings appearing on textiles.
Cleaning Method of High Temperature and High Pressure Dyeing Machine
One of the most critical aspects of maintaining these machines is cleaning them regularly. Over time, dirt and debris can accumulate in the machine’s nooks and crannies, leading to reduced efficiency or even breakdowns.
To clean a high-temperature and high-pressure dyeing machine effectively, you need to follow specific steps carefully. First off, make sure that all valves are closed before starting the cleaning process.
Then drain any remaining water from the machine before adding a mixture of hot water (around 80°C) with an alkaline detergent.
Next up is running a wash cycle at around 130°C for about two hours while monitoring pressure levels closely throughout this period. Afterward, drain out all used detergent solution from your system by opening up each valve one after another until there’s no more liquid left inside it.
Influencing Factors of Color Measurement Accuracy of Dyed Textiles
The slightest variation in shade or hue can make a significant difference in the final product’s quality and appeal. Several factors can influence color measurement accuracy, including lighting conditions, observer variability, instrument calibration errors, sample preparation methods and environmental factors such as temperature and humidity.
Lighting conditions play a vital role in determining how colors are perceived by the human eye. Different light sources have varying spectral distributions that affect how colors appear under them.
Therefore it is essential to use standardized lighting conditions for accurate color measurements.
Observer variability refers to differences between individuals’ perception of colors due to variations in their visual acuity or personal preferences; this factor can be minimized through proper training of observers involved with measuring dyeing textiles’ shades.
Importance of Laboratory Dyeing Machine Dyeing
They allow for the testing of different dyes, chemicals, and processes on a small scale before implementing them in large-scale production. This helps to reduce waste, save time and money while ensuring that the final product meets quality standards.
The importance of laboratory dyeing machine dyeing cannot be overstated as it allows manufacturers to test various parameters such as temperature, pressure, pH levels among others without risking damage or loss of materials. Lab dyed samples can be used to predict how a particular color will look on different fabrics or fibers before committing resources towards full-scale production.
Laboratory dyeing machines play a crucial role in ensuring that textile products meet industry standards while reducing costs associated with trial-and-error methods during large-scale productions.
Common Dyeing Methods of Chemical Fiber
They have become increasingly popular in the textile industry due to their durability, versatility, and affordability. However, dyeing chemical fiber can be a bit challenging as they do not absorb dyes easily like natural fibers such as cotton or wool.
There are several common methods used for dyeing chemical fiber including solution-dyeing method, stock-dyeing method and yarn-dyeing method.
The solution-dyeing method involves adding pigments to the polymer before it is extruded into filaments or spun into yarns. This process ensures that the color penetrates through every part of the fiber resulting in a uniform color throughout.
Stock dyeing involves immersing loose staple fibers in a dyebath before they are spun into yarns or woven into fabrics. This technique allows for better penetration of dyes compared to other methods but may result in uneven colors if not done correctly.
Yarn dyeings involve dying individual strands of thread prior to weaving them together which results in more vibrant colors with less bleeding than fabric dying techniques. Understanding these different types of common methods used for coloring synthetic materials will help you choose which one is best suited for your project needs while ensuring optimal results when working with Chemical Fiber textiles.
FAQ
Which machine is used for yarn dyeing?
The machine used for yarn dyeing is the Laboratory Dyeing Machine SIMPLEX, which operates at high pressure and temperature in air-pad mode.
How many types of dyeing machines are there?
There are 4 types of dyeing machines according to textile material: Fiber dyeing machine, Yarn dyeing machine, Fabric dyeing machine, and Garment dyeing machine.
What are the key features of various yarn dyeing machines?
Key features of various yarn dyeing machines include efficiency, flexibility, automation, material compatibility, and precise control over temperature and dyeing process.
How do different yarn dyeing machines affect the final product quality?
Different yarn dyeing machines affect the final product quality by varying in factors such as dye penetration, color uniformity, and process efficiency.
What factors should be considered when choosing a yarn dyeing machine for a textile operation?
When choosing a yarn dyeing machine for a textile operation, consider factors such as the machine’s dyeing capacity, energy efficiency, automation level, versatility in dyeing different types of yarn, and ease of maintenance.