Discover the diverse types of yarn used in denim production, as we unravel their unique characteristics and applications in creating your favorite jeans.
Denim is a versatile fabric that has been a fashion staple for decades. From jeans to jackets, denim is everywhere.
But have you ever wondered about the yarn used to create this iconic fabric? There are actually several types of yarn that can be used in denim production, each with its own unique characteristics and benefits. In this article, we will explore the different types of yarn used in denim and how they contribute to the final product’s look and feel.
Whether you’re an avid crafter or just curious about textile production, this article will provide insight into one of the most beloved fabrics in fashion history. So grab your knitting needles or crochet hook and let’s dive into the world of denim yarn!
Types of Yarn in Denim
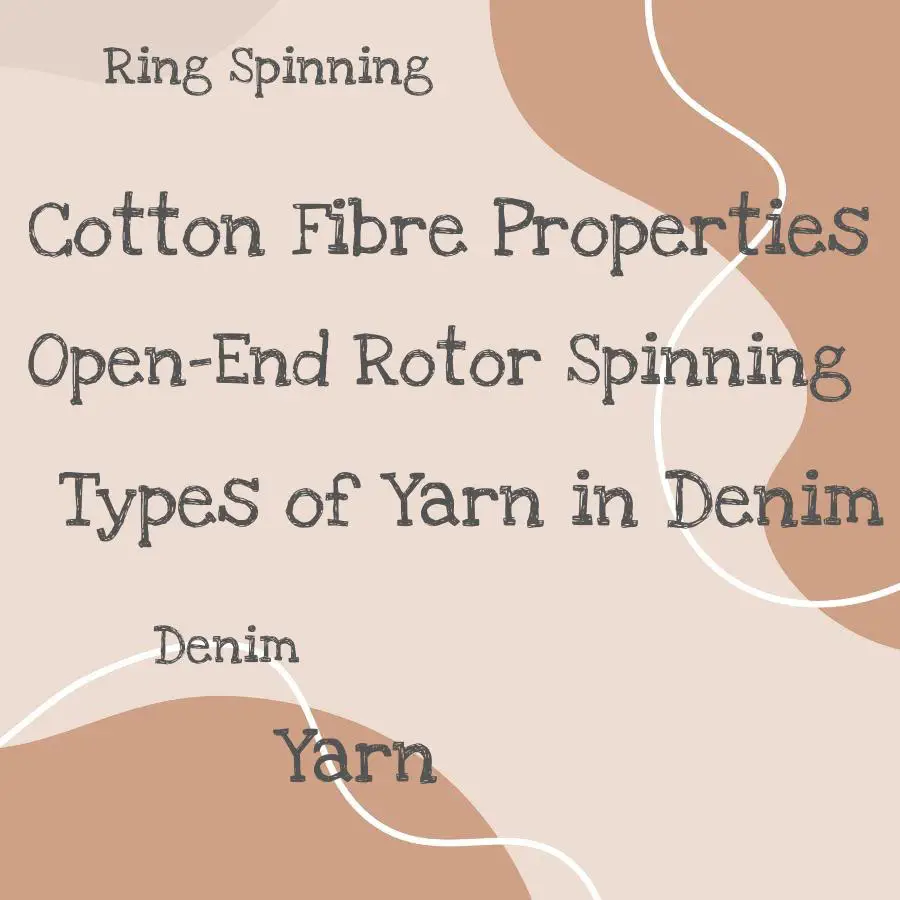
Denim yarns come in different types, each with its unique characteristics and applications. The most common types of yarn used in denim production are cotton, polyester, and Tencel.
Cotton is the most popular type of fiber used to make denim because it is durable and comfortable to wear. Polyester fibers are added to cotton for stretchability or durability purposes while Tencel fibers provide a soft feel that drapes well.
Another factor that affects the quality of denim fabric is the spinning system used during production. There are two main spinning systems: ring spinning and open-end rotor spinning.
Ring-spun yarns have a smoother texture than open-end rotor spun ones due to their higher twist levels which result in stronger threads with less hairiness on their surface compared to those produced by an open-end rotor spinner machine.
Yarn Numbering
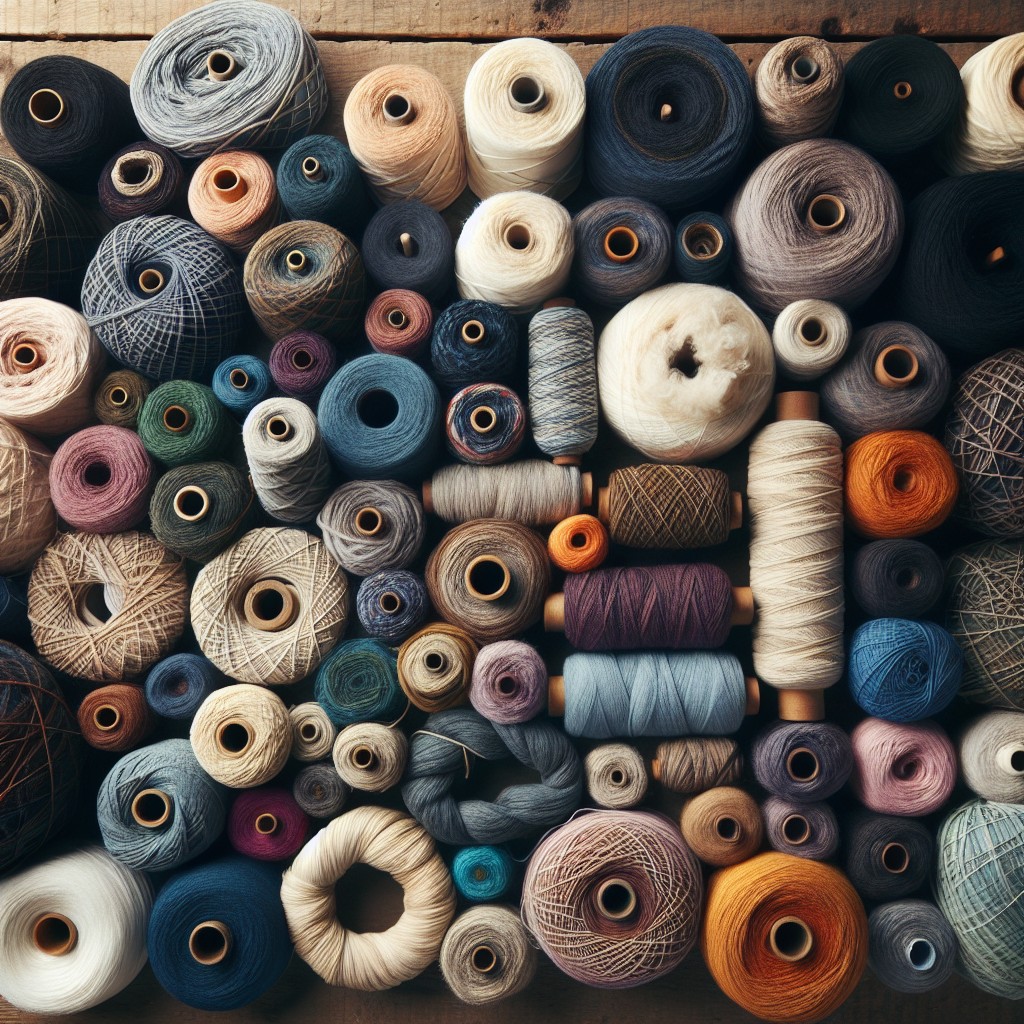
It refers to the thickness or fineness of the yarn used in creating denim fabric. The numbering system for yarns varies depending on the country and region, but it generally follows a standard convention.
In North America, yarns are numbered based on their weight per unit length (yards or meters). This system is known as “cotton count” and is denoted by a number followed by “S.” For example, 10S cotton means that 840 yards weigh ten pounds.
In contrast, Europe uses metric systems such as Tex and Nm (metric number). Tex measures grams per kilometer while Nm measures kilometers per gram.
A higher Nm value indicates finer yarn than lower values.
Understanding Yarn Numbering helps manufacturers determine which type of thread to use when producing different types of denim fabrics with varying weights and textures.
Yarn Spinning Systems
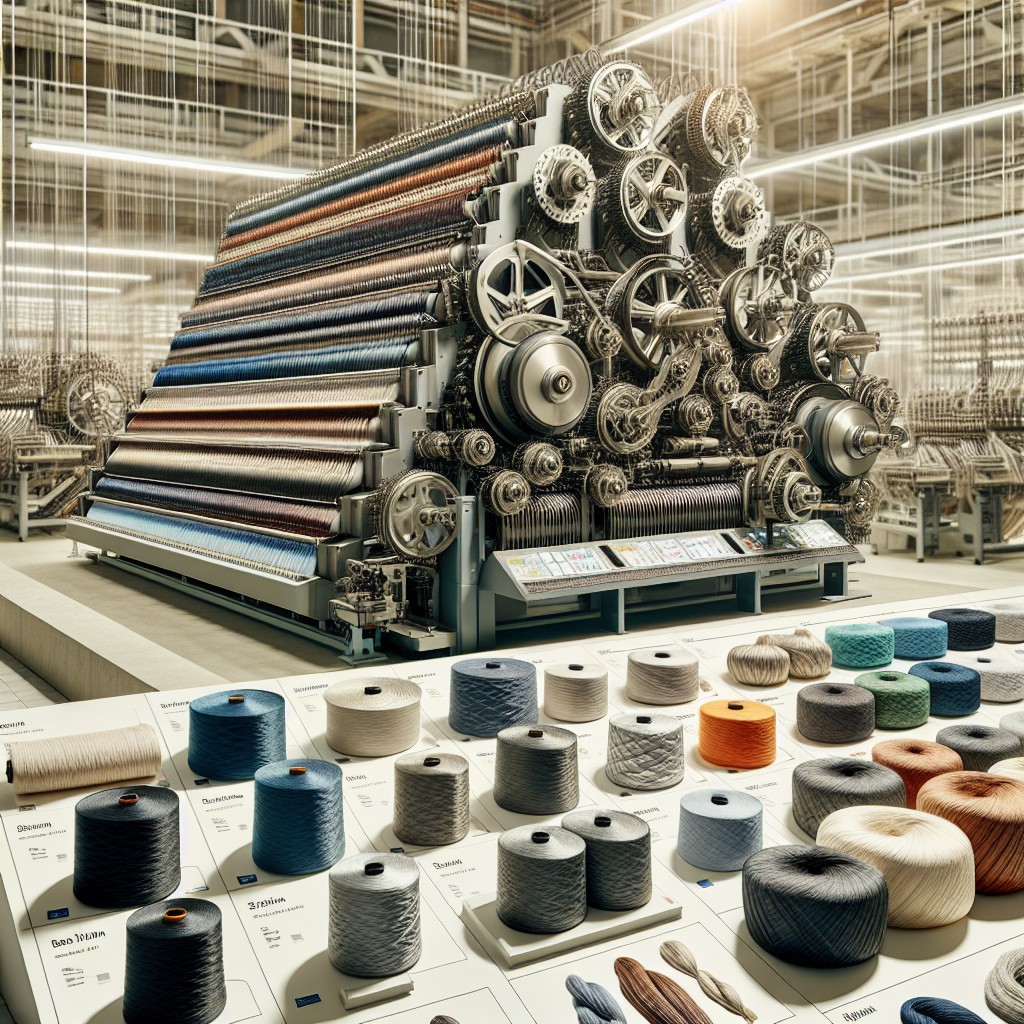
The two most commonly used spinning systems are Ring Spinning and Open-End Rotor Spinning.
Ring spinning is a traditional method that has been used for centuries to produce high-quality yarns with excellent strength and durability. In this process, the fibers are twisted together using a ring frame machine, which creates strong, smooth yarns.
On the other hand, Open-End Rotor Spinning is relatively new compared to ring spinning but has gained popularity due to its efficiency in producing large quantities of denim yarn at lower costs than ring-spun methods.
In rotor-spinning machines, fibers are fed into an opening roller where they get separated before being drawn through an air vortex created by rapidly rotating rotors that twist them together into single strands of uniform thickness.
Both Ring-Spun and Open-End Yarn Combinations can be utilized depending on specific requirements such as cost-effectiveness or quality standards needed for different types of denims like stretch or elastic denims.
Open-End Rotor Spinning
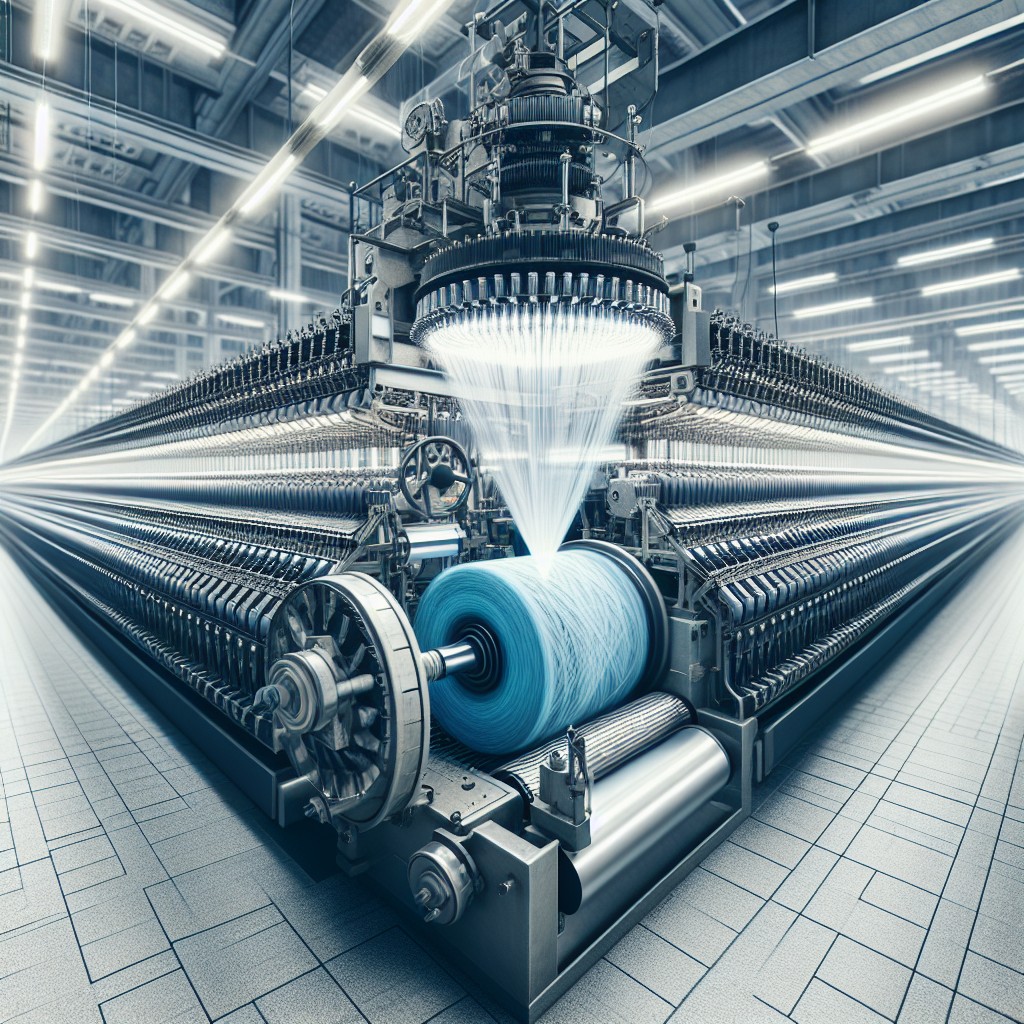
This process involves feeding the fibers into a rotor, which then twists and spins them together to create the yarn. Unlike ring spinning, open-end rotor spinning does not require a spindle or bobbin to hold the fiber during twisting.
One of the benefits of open-end rotor spinning is its speed and efficiency. The process can produce large quantities of yarn quickly, making it ideal for mass production environments like denim factories.
However, there are also some drawbacks to this method compared with ring spinning. Open-end rotor spun yarns tend to be less uniform than their ring-spun counterparts due to variations in twist levels throughout each strand.
These types of yarns may have lower strength and abrasion resistance than those produced through other methods.
Ring Spinning
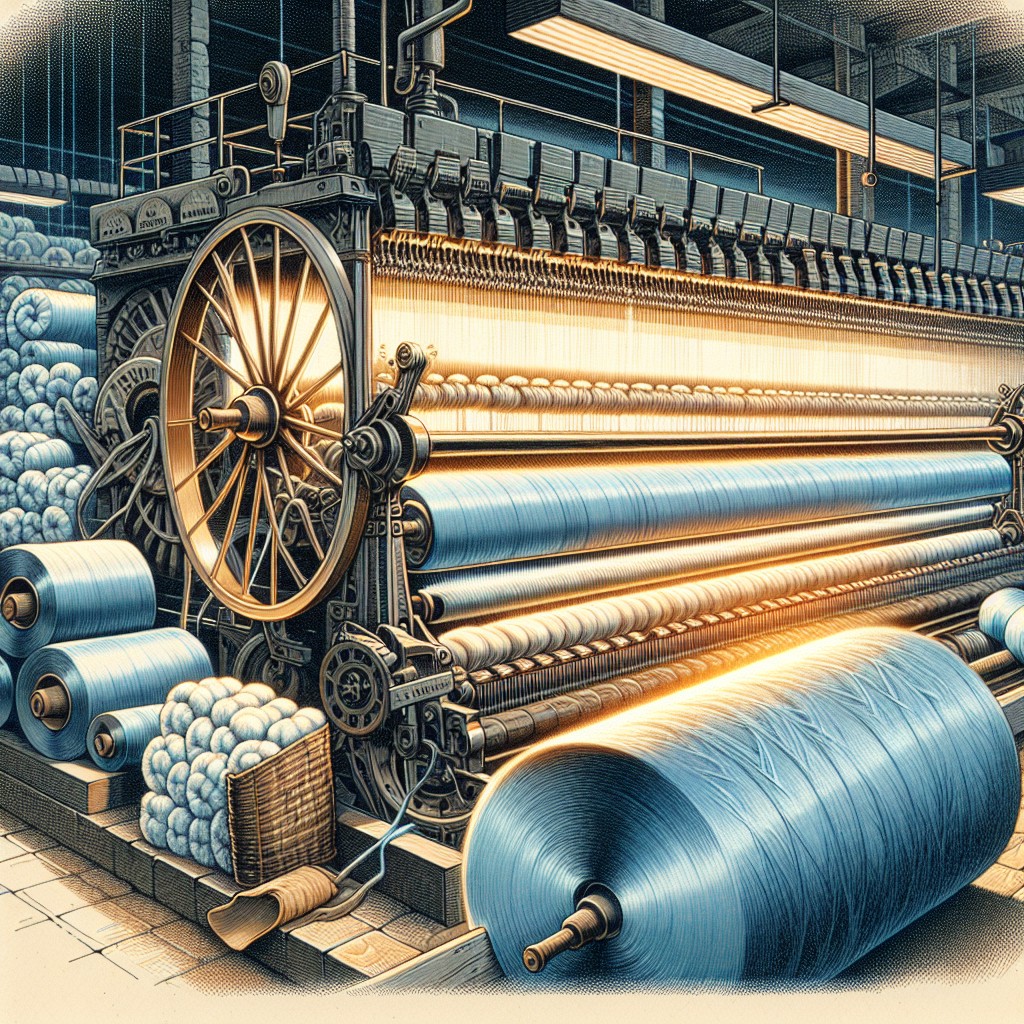
This process involves twisting and thinning cotton fibers into a continuous strand, which is then wound onto bobbins for use in weaving or knitting. The resulting yarn has a smooth surface and high strength, making it ideal for creating durable denim fabrics.
During ring spinning, the cotton fibers are first carded to remove any impurities and align them in parallel strands. These strands are then drawn out into long ropes called slivers before being fed through rollers that twist them together tightly.
One of the benefits of ring-spun yarns is their ability to create unique textures such as slub or neppy effects by varying fiber length during processing. They can be made with different levels of twist depending on desired fabric properties like softness or durability.
While other methods like open-end rotor spinning have gained popularity due to their efficiency at producing large quantities quickly, many still prefer ring-spun denim because it offers superior quality and texture that cannot be replicated by other means.
Understanding how different types of yarn contribute to the final product’s look and feel can help you make informed decisions when selecting materials for your next project.
Ring & Open-End Yarn Combinations
This method involves combining both ring-spun and open-end spun yarns to create a unique texture that is both durable and comfortable. The combination of these two types of yarn allows for the creation of a fabric that has the strength and durability associated with ring-spun cotton, while also having the softness and breathability typically found in open-end spun cotton.
The process involves using one or more strands of ring-spun cotton as well as one or more strands of open-end spun cotton during weaving. By doing this, manufacturers can achieve different textures depending on how many strands they use for each type.
This technique is often used to create denim fabrics with varying degrees of stretchiness, which have become increasingly popular over recent years due to their comfort factor. It’s an excellent way for manufacturers to add value by creating unique textures without sacrificing quality.
Twist
It refers to the number of turns per inch in a yarn and can be either S-twist or Z-twist. The twist direction determines how the fibers will hold together during spinning and weaving.
In denim production, twist plays a crucial role in creating different types of fabrics with unique textures and finishes. For instance, high-tension twisting creates compact yarns that produce sturdy fabrics suitable for workwear or heavy-duty jeans.
On the other hand, low-tension twisting produces softer yarns with more significant spaces between fibers resulting in lighter-weight denims ideal for summer wear or fashion-forward styles.
Moreover, twisted slub-yarns are used to create crosshatch/streak/rain effects on denim fabric surfaces by varying their density across warp/weft directions.
Basic Cotton Fibre Properties
Understanding its basic properties is essential to understanding how different types of yarn are created and how they contribute to the final product’s look and feel. Cotton fibers come from cotton plants, which produce fluffy white bolls that are harvested and processed into raw cotton.
The length, strength, fineness, maturity level, coloration (natural or bleached), trash content (non-lint materials), micronaire value (a measure of fineness based on air permeability) all affect the quality of cotton fibers.
In denim production specifically, longer staple lengths tend to be preferred as they create stronger yarns with fewer protruding ends that can cause fuzziness or pilling over time. Mature fibers tend to have a higher degree of twist than immature ones due to their increased rigidity.
Summary Statistics for Ring-Spun Yarn Properties
The process of creating ring-spun yarn involves twisting the fibers together tightly, resulting in a smooth and even texture. But what are the specific properties of this type of yarn? Let’s take a look at some summary statistics for ring-spun yarn properties.
According to industry standards, ring-spun cotton denim typically has an average count range between 6s-20s (the higher the number, the finer/thinner the thread). The twist factor/multipliers used for these types of denims can vary depending on factors such as fiber length and desired fabric weight.
In terms of physical characteristics, ring-spun cotton denim tends to have high tensile strength (resistance to breaking under tension) and abrasion resistance (ability to withstand wear from rubbing or friction). It also has good moisture absorption properties which make it comfortable against skin.
Twist Factor/Multipliers Used for Denim Yarns
It determines the strength, durability, and appearance of the final product. The twist factor refers to the number of turns per inch in a yarn’s structure.
In general, higher twists result in stronger and more durable fabrics.
For denim yarns specifically, there are different twist factors used depending on the desired outcome for each fabric type. For example, ring-spun cotton denim typically has a lower twist factor than open-end rotor spun cotton denim due to its softer feel.
In addition to determining strength and durability, the twist also affects how light reflects off of each individual fiber within a strand – this can create unique visual effects such as slubs or streaks that give some denims their characteristic look.
Yarn Count Conversion Tables
The yarn count refers to the number of yards per pound of a particular type of yarn. In denim production, different types of counts are used depending on the desired fabric weight and texture.
Yarn counts can be confusing for those who are new to textile production or unfamiliar with industry standards. That’s where conversion tables come in handy! These tables provide a quick reference guide for converting between different types of yarn counts.
For example, if you’re working with a 10-count cotton denim but want to switch to a 2/20-count Tencel blend, you can use a conversion table to determine how many strands or plies will be needed for your project.
By understanding these conversions and utilizing them effectively during production processes such as warping or weaving preparation stages; manufacturers can ensure that they achieve their desired results without wasting time or resources on trial-and-error methods.
Elastic Denim Yarns
These yarns contain a small percentage of spandex or elastane, which gives them stretch and recovery properties. This means that jeans made with elastic denim yarns can be more comfortable and form-fitting than traditional non-stretch jeans.
The use of elastic denim yarns has become increasingly popular in recent years, as consumers demand more comfort from their clothing without sacrificing style. However, it’s important to note that not all stretch denims are created equal – some may have too much elasticity or not enough recovery, leading to sagging or bagging over time.
To ensure the best quality stretch denims, manufacturers must carefully balance the amount of elastane used in their elastic denim yarns with other factors such as twist level and cotton fiber properties. By doing so, they can create durable yet comfortable fabrics that meet consumer demands for both fashion and function.
Crosshatch / Streak / Rain Denims
Crosshatch denim is characterized by a subtle crisscross pattern on the fabric’s surface, while streak denim features long lines running vertically down the length of the fabric. Rain denim has a distinctive mottled appearance that resembles raindrops falling on water.
These effects are achieved through various yarn spinning techniques and dyeing processes. For example, crosshatch patterns can be created by using different colored warp and weft yarns or varying their twist levels during spinning.
Streaks can be produced through uneven dye penetration or by using slub yarns with thicker sections at regular intervals.
Rain denims typically use reactive dyes to achieve their unique look as they allow for better color absorption into specific areas of the fabric than other types of dyes.
Crosshatch/streak/rain denims offer an exciting alternative to traditional solid-colored jeans while still maintaining all the durability and versatility associated with classic blue jeans.
Chinos
They were originally designed for military use but quickly became a fashion staple due to their versatility and comfort. Chinos are typically made from cotton twill fabric, which is woven using a diagonal pattern that gives it its characteristic texture.
When it comes to denim production, chino-style denim has become increasingly popular in recent years. This type of denim is made using the same weaving technique as traditional chinos but with added stretch fibers for increased flexibility and comfort.
Chino-style denim can be used to create a variety of garments, including jeans, jackets, and shorts. It’s also available in different colors besides blue such as khaki or beige tones.
Tencel Denim
It is made from wood pulp and produced using a closed-loop system, which means that the chemicals used in production are recycled rather than released into the environment. Tencel denim offers all the benefits of traditional denim, such as durability and versatility, while also being more sustainable.
In addition to its environmental advantages, Tencel denim also boasts excellent moisture management properties. This means it can absorb moisture quickly and release it just as fast, making it ideal for hot weather or active wear.
Another benefit of Tencel denim is its softness compared to traditional cotton-based denims. The fibers are smoother than cotton fibers resulting in softer fabric with less pilling over time.
Stretch Denims
This type of denim is made by adding spandex or elastane fibers to the cotton yarn during spinning, which gives it its characteristic stretchiness. The amount of spandex added can vary depending on how much stretch is desired in the final product.
One advantage of using stretch denim is that it allows for greater freedom of movement, making it ideal for jeans that are meant to be worn all day long. It also helps prevent sagging and bagging over time, ensuring your jeans maintain their shape even after multiple washes.
However, there are some downsides to using this type of yarn in production as well. Stretch denims tend to be more expensive than regular denims due to their additional materials cost and require special care when washing them at home.
Union Denim
This blend creates a fabric that is both durable and stretchy, making it ideal for jeans that need to withstand daily wear and tear. Union denim also tends to be more affordable than 100% cotton denim since the synthetic fibers are less expensive.
The use of synthetic fibers in union denim has been controversial among some purists who believe that only natural materials should be used in textile production. However, many manufacturers argue that the addition of synthetics can improve the performance and longevity of their products.
Despite this debate, union denims have become increasingly popular over recent years due to their versatility and affordability. They come in various weights ranging from lightweight summer fabrics up to heavy winter-weight options suitable for colder climates.
Poly Denim
This blend creates a fabric that is more durable and resistant to wrinkles than traditional cotton denim. Poly denim also has excellent stretch and recovery properties, making it ideal for form-fitting jeans or other garments.
The addition of polyester fibers can alter the look and feel of the final product, giving it a smoother texture with less visible grain than pure cotton denims. However, poly-denim still maintains its classic indigo coloration while providing additional benefits such as moisture-wicking capabilities.
Polyester blends are often used in combination with spandex or elastane to create stretchy fabrics commonly found in skinny jeans or jeggings. These materials provide comfort without sacrificing style.
Poly-denim offers an attractive alternative for those looking for durability combined with flexibility in their clothing choices.
Poly Stretch Denim
It’s made by blending cotton with synthetic fibers like polyester and spandex, which gives the fabric its stretchy properties. This blend makes poly stretch denim an excellent choice for creating comfortable and form-fitting jeans that move with your body.
The addition of synthetic fibers also increases the durability of poly stretch denim, making it resistant to wear and tear. This means that your favorite pair of jeans will last longer without losing their shape or color.
Polyester is known for its ability to hold dye well, so poly-stretch denims come in a wide range of colors from deep indigo blues to bright hues like reds or greens. The added benefit here is that these dyes are less likely to fade over time compared to other types of yarns used in denim production.
Spandex adds elasticity while maintaining breathability; this allows you freedom when moving around without feeling restricted as you would with regular non-stretch fabrics.
Linen Vintages
In denim, linen is often added to create a vintage look and feel. Linen vintages are created by blending cotton with linen fibers during the spinning process, resulting in yarns with unique characteristics.
Linen fibers have a distinctive texture and sheen that can add depth and dimension to denim fabrics. When blended with cotton, they create yarns that are stronger than pure cotton but still retain their softness.
In addition to adding visual interest, linen vintages also offer practical benefits such as increased breathability and moisture-wicking properties. This makes them ideal for creating lightweight summer denim garments or jeans designed for active wear.
Incorporating linen into denim production adds an element of sophistication while maintaining the fabric’s durability and versatility.
Value Engineering
The goal is to identify areas where costs can be reduced without sacrificing quality or performance. This approach has become increasingly popular in recent years as manufacturers look for ways to remain competitive while still producing high-quality products.
One way value engineering can be applied to denim production is by adding recycled waste material into the yarns. By doing this, manufacturers are able to reduce their overall material costs while also reducing waste and promoting sustainability.
Another method of value engineering involves controlling yarn realization, which refers to how much usable yarn is produced from a given amount of raw cotton fiber. By optimizing this process, manufacturers can minimize waste and increase efficiency, ultimately leading to cost savings.
Addition of 10% Recycled Waste
One way that manufacturers are reducing their environmental impact is by incorporating recycled waste into their yarns. By adding 10% of recycled waste material, such as cotton or polyester fibers, to the yarn mix during spinning, manufacturers can reduce overall resource consumption and minimize textile waste.
This approach not only benefits the environment but also creates unique textures and colors in denim fabrics. The addition of recycled materials can create a speckled effect in the fabric’s surface or add subtle variations in color throughout.
Moreover, this technique has been adopted by many leading brands worldwide who have pledged to make sustainable changes within their supply chains while still delivering high-quality products for consumers.
Incorporating 10% of recycled waste into denim yarns offers an eco-friendly solution without compromising on quality or style.
Control of Yarn Realization
It refers to the ability to control the amount of yarn produced from a given weight or length of cotton fiber. This process ensures that there is consistency in the quality and quantity of yarn used in denim production, which ultimately affects the final product’s look and feel.
To achieve this level of control, manufacturers use advanced technology such as electronic monitoring systems that measure various parameters during spinning. These include twist levels, diameter variations along with individual fibers’ lengths and strengths.
By controlling these variables throughout spinning processes like ring-spun or open-end rotor spun methods, manufacturers can ensure consistent results across batches while minimizing waste materials generated by overproduction or underproduction scenarios.
Controlling yarn realization plays an essential role in producing high-quality denim fabrics consistently.
Mock Rings
This process involves twisting open-end spun yarns at high speeds, which creates a spiral effect that mimics the look and feel of ring-spun yarn. The result is a softer, more comfortable fabric with enhanced durability and strength.
The use of mock rings has become increasingly popular in recent years as manufacturers seek to produce high-quality denim fabrics while reducing costs. By utilizing this technique, they can achieve similar results to those obtained through traditional methods but with less time and expense involved.
In addition to its cost-saving benefits, mock rings also offer environmental advantages by reducing water usage during production compared to conventional spinning techniques. As sustainability becomes an increasingly important consideration for consumers worldwide, this eco-friendly approach is likely to gain even more traction in the future.
Other Value Offerings
One such offering is the addition of recycled waste into denim yarns. By incorporating 10% recycled waste into their yarns, manufacturers can reduce their environmental impact while still producing high-quality fabrics.
Another value offering is mock rings, which mimic the look and feel of traditional ring-spun yarn but are produced using open-end rotor spinning technology. This allows for a more cost-effective production process without sacrificing quality or aesthetics.
These additional value offerings demonstrate how innovation and sustainability can go hand-in-hand in textile production.
The Global Desirability for Ring-Spun and Slub Yarns
Ring-spun yarns are made by twisting the fibers tightly together, resulting in a smoother and stronger fabric. Slub yarns, on the other hand, have an irregular thickness that creates unique texture variations in denim.
The global demand for these types of denim has led to increased production of ring-spun and slub yarns. In response to this trend, many manufacturers now offer specialized lines featuring these sought-after materials.
Ring-spun denim is particularly popular among vintage clothing aficionados who appreciate its durability and classic look. Meanwhile, slub-yarned denims are favored by those seeking more textured fabrics with characterful imperfections.
Conclusions
From ring-spun to open-end rotor spinning, each type of yarn has its unique characteristics that contribute to denim’s versatility as a fabric. The twist factor/multipliers used for denim yarns also affect their properties, such as strength and durability.
Advancements like elastic denims or Tencel Denim have expanded the possibilities for this classic fabric.
Value engineering techniques like adding recycled waste or controlling yarn realization can help manufacturers create high-quality products while reducing costs. And with global demand increasing for ring-spun and slub-yarns due to their desirable texture and appearance, it is clear that innovation will continue driving progress in this industry.
As we’ve seen throughout this article on types of yarn used in denim production – from basic cotton fiber properties to advanced manufacturing techniques – there is much more than meets the eye when it comes to creating your favorite pair of jeans!.
FAQ
What kind of yarn is used in denim?
Answer: Denim is made using short-staple spun yarns, which are formed from fibers with a staple length of fewer than 2.5 inches, typically around an inch long, with yarn size being a key factor in denim development and manufacturing.
What thickness yarn for denim?
The typical thickness of yarn for denim ranges from Ne 4s (heavy) to Ne 12s (similar to tablecloth fabric).
What are the raw materials for denim jeans?
The raw materials for denim jeans are cotton fibers, which are woven using a twill weave to create the iconic diagonal ribbing of denim material.
How does the yarn type affect the durability of denim fabric?
The yarn type affects the durability of denim fabric by determining its strength, thickness, and overall quality, which contributes to the longevity of the material.
Are there sustainable yarn options for producing eco-friendly denim?
Yes, there are sustainable yarn options for producing eco-friendly denim, such as using recycled and organic cotton, Tencel, and hemp.
Which yarn characteristics contribute to the different textures of denim?
The yarn characteristics that contribute to the different textures of denim include the fiber content, yarn thickness, and twist.