Discover the fascinating world of yarn spinning systems as we delve into various types and their unique characteristics in this informative blog post.
Do you ever wonder how the yarn that you love to crochet or knit with is made? The process of yarn spinning is a fascinating one, and there are several different systems used to create the various types of yarn we use in our crafts. Understanding these spinning systems can help you choose the perfect yarn for your project and even inspire new creative ideas.
In this article, we’ll explore some of the most common types of yarn spinning systems and their unique characteristics. So grab your hook or needles, settle in with your favorite beverage, and let’s dive into the world of yarn spinning!
Types of Yarn Spinning Systems
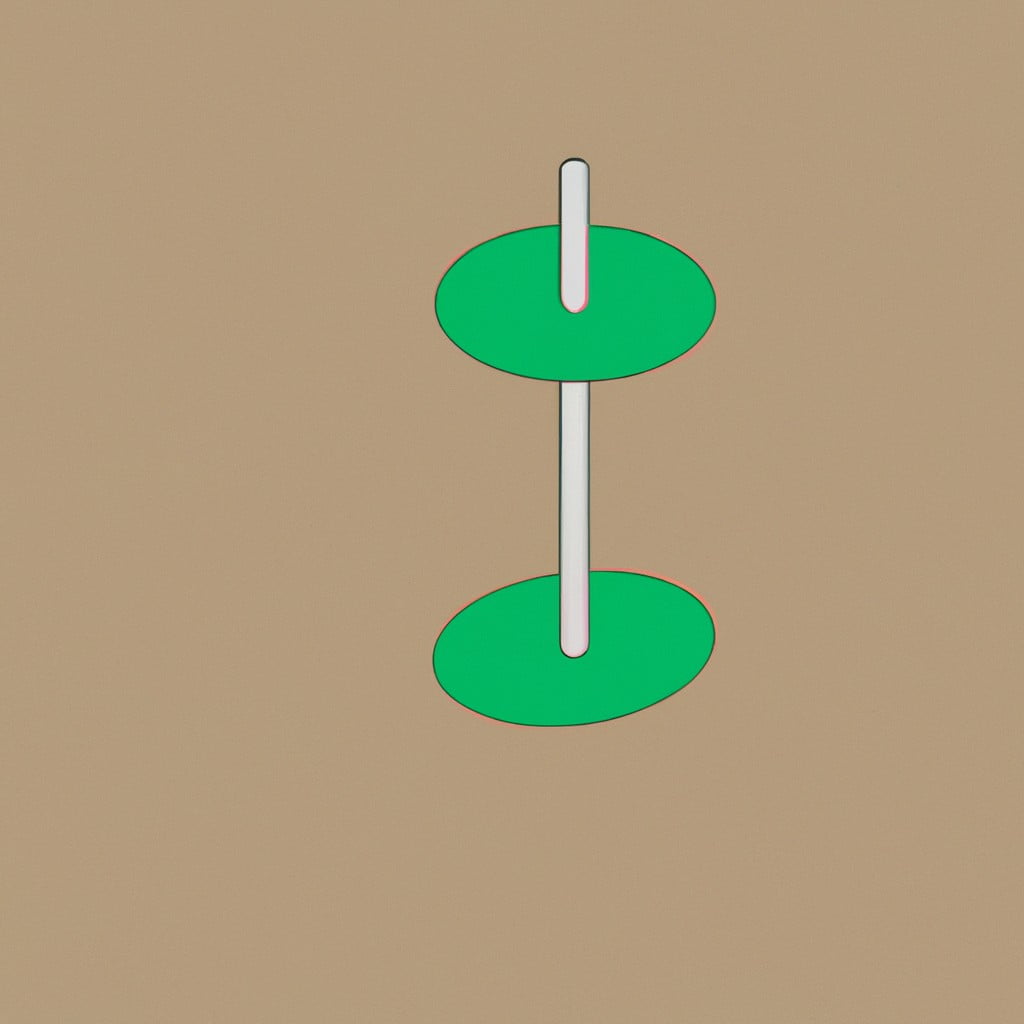
Ring Spinning is one of the most common types of yarn spinning systems. It involves twisting fibers together using a ring and bobbin mechanism to create a continuous strand of yarn.
This process produces strong, durable yarn that is ideal for everyday use in garments and home decor items.
Rotor Spinning, also known as open-end spinning, uses a rotor to spin fibers into yarn. The rotor spins at high speeds while drawing in fiber from the feeding system before twisting it into thin strands that are wound onto bobbins or cones.
Air-Jet Spinning utilizes compressed air to twist fibers together rapidly, creating fine threads with excellent strength and elasticity. This method can produce large quantities of high-quality synthetic or natural fiber blends quickly.
Wet Spinning involves dissolving raw materials such as cellulose or protein-based polymers in solvents before extruding them through spinnerets into coagulating baths where they solidify into filaments which are then twisted together to form single-ply or multi-ply threads.
Dry Spinning works similarly but without using solvents; instead, polymer chips are melted down under heat until they become liquid enough for extrusion through spinnerets followed by cooling on contact with air streams forming filaments which get twisted later on during processing stages. Gel-Spinning creates ultra-strong synthetic fibers by stretching gel-like substances made from polymers dissolved in solvent solutions over long distances while maintaining their orientation along the lengthwise axis resulting in highly aligned molecular structures within each filament produced.
Direct-Spinning combines wet-spinning techniques with melt-spun processes allowing direct conversion from molten polymer feedstock directly spun out via spinnerettes producing multifilament bundles suitable for further processing steps like texturizing etcetera. Solution-Spinning employs similar principles used during wet-spinning but instead relies upon chemical reactions between different components present within solution mixtures leading up towards formation fibrous structures after exposure time periods.
Melt-Spinning Process is a technique that involves melting polymer chips and extruding them through spinnerets to create continuous filaments. This process can produce high-quality synthetic fibers with excellent strength, durability, and elasticity.
Understanding the different types of yarn spinning systems available can help you choose the perfect yarn for your project. Each system has its unique characteristics that affect the quality and properties of the resulting yarn.
Ring Spinning
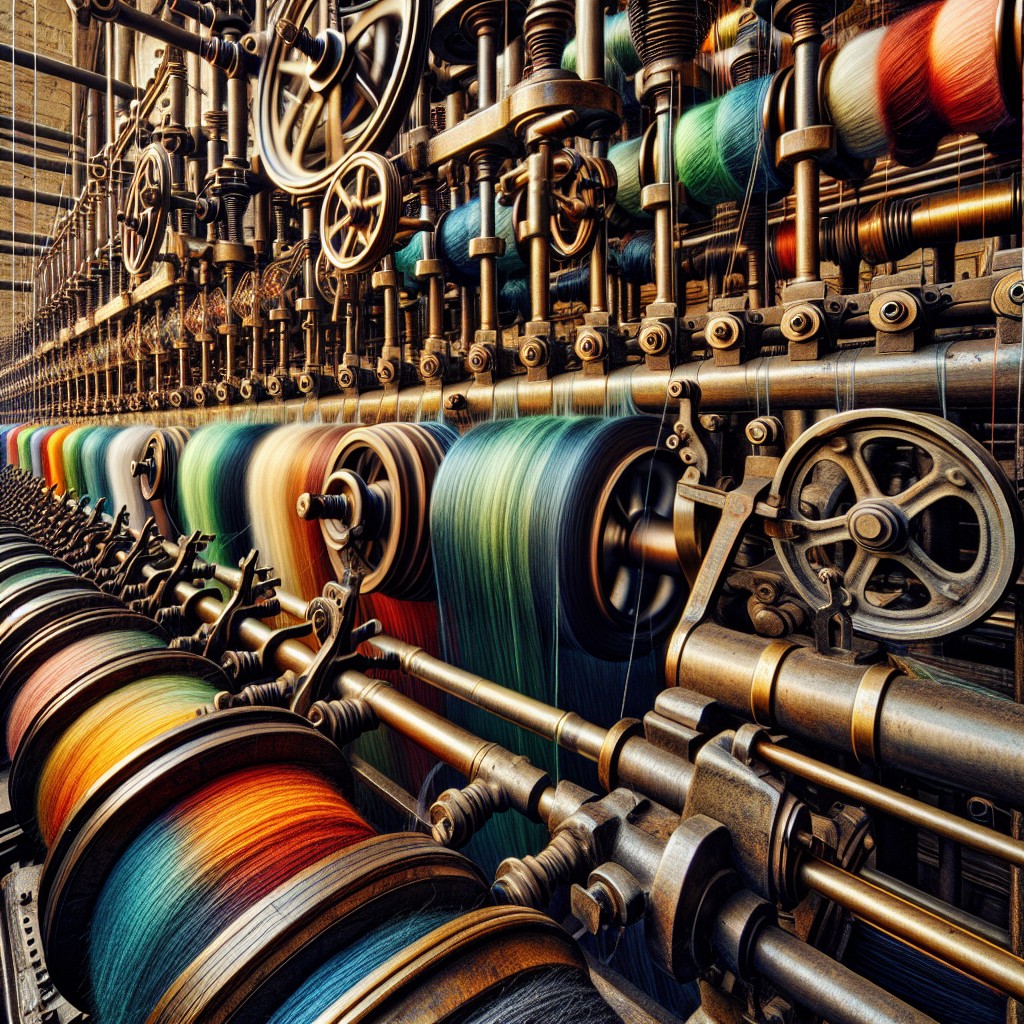
It involves pulling fibers through a small metal ring, which twists them together to form a continuous strand of yarn. This process creates strong and durable yarns that are ideal for use in clothing, home textiles, and other applications.
One advantage of ring spinning is its versatility – it can be used with a wide range of fiber types including cotton, wool, silk and synthetic fibers like polyester or nylon. This method produces consistent quality yarns with excellent strength properties.
However, there are some drawbacks to using ring spun yarns as well. The process can be slow compared to other methods such as rotor or air-jet spinning which may not make it suitable for high volume production environments where speed is critical.
Rotor Spinning
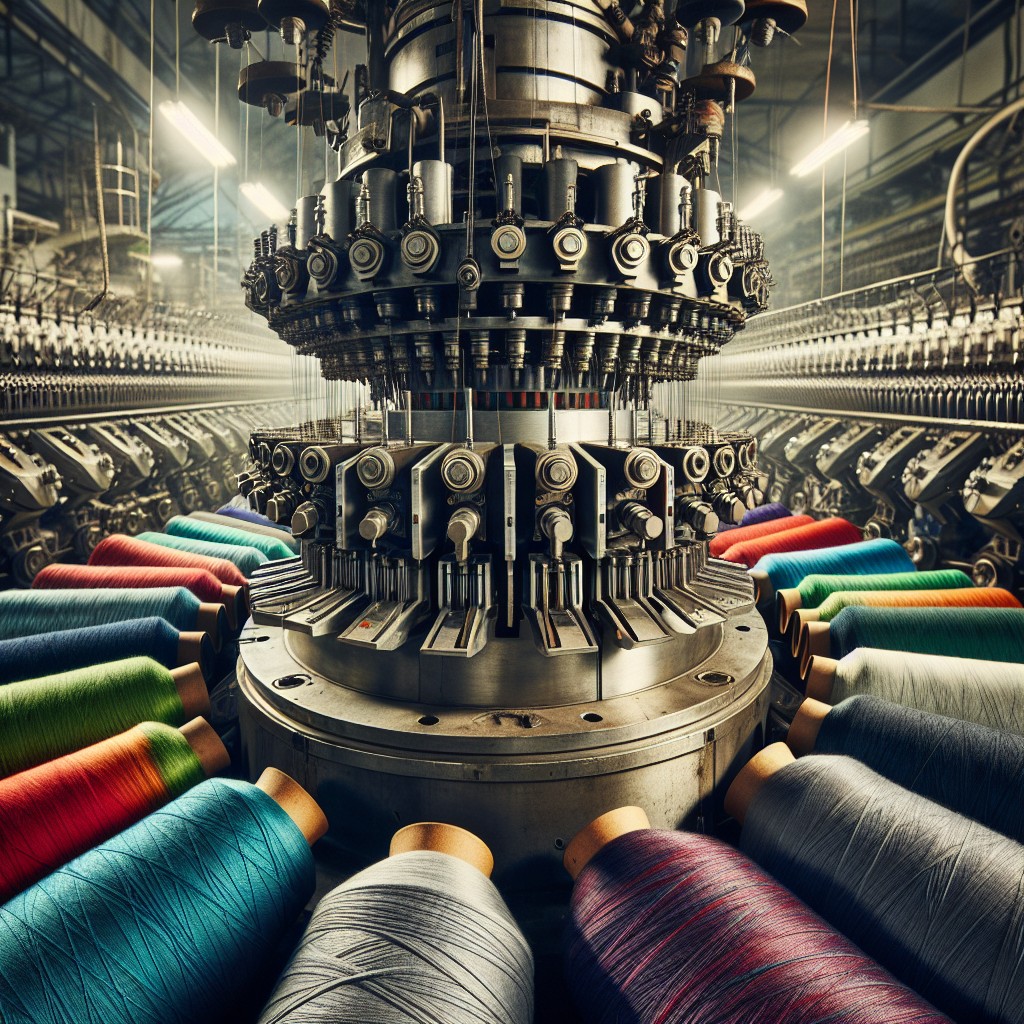
This system works by feeding fibers into the machine, where they are twisted and spun into yarn as they pass through a rapidly rotating rotor. The resulting yarn has an irregular texture and is often used for making denim fabrics.
Compared to ring spinning, which produces smoother and stronger yarns, rotor-spun fibers have lower twist levels but higher productivity rates. Rotor-spun cotton also tends to be more absorbent than ring-spun cotton due to its rougher surface texture.
One advantage of using this type of system is that it can process various types of fiber materials such as wool, acrylics, polyester blends among others at high speeds with minimal waste compared to other methods like wet-spinning or dry-spinning processes.
Air-Jet Spinning
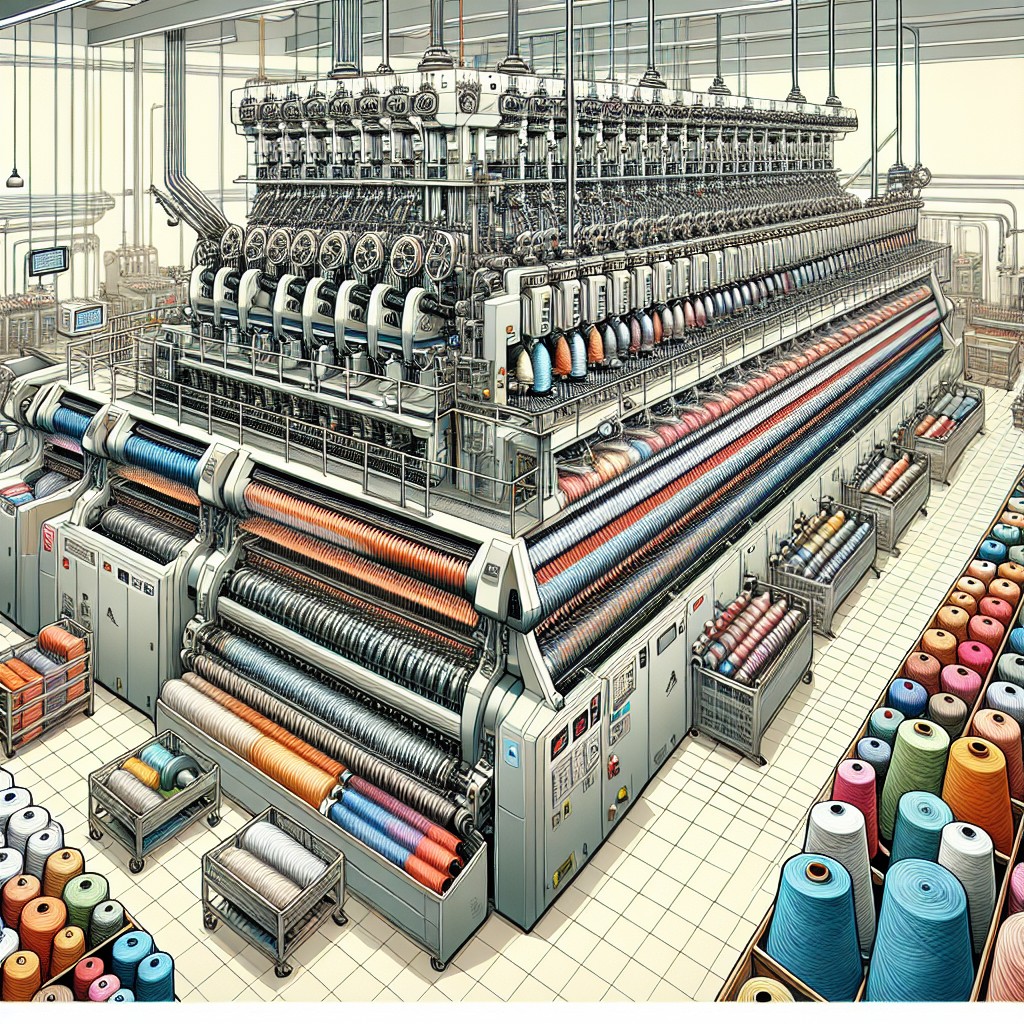
This process creates a lightweight, soft, and durable yarn that is perfect for knitting or crocheting garments with excellent drape.
Unlike ring spinning, which involves twisting the fibers using mechanical means, air-jet spinning relies on compressed air to create the necessary force. The fiber bundle is fed into an airstream where it’s twisted by turbulent airflow before being wrapped onto a bobbin.
One of the benefits of this system is its speed; it can produce large quantities of yarn in less time than other methods. Because there are no moving parts involved in creating tension on the fiber bundle during twisting like ring-spinning machines have – there’s less wear-and-tear on equipment over time!
Wet Spinning
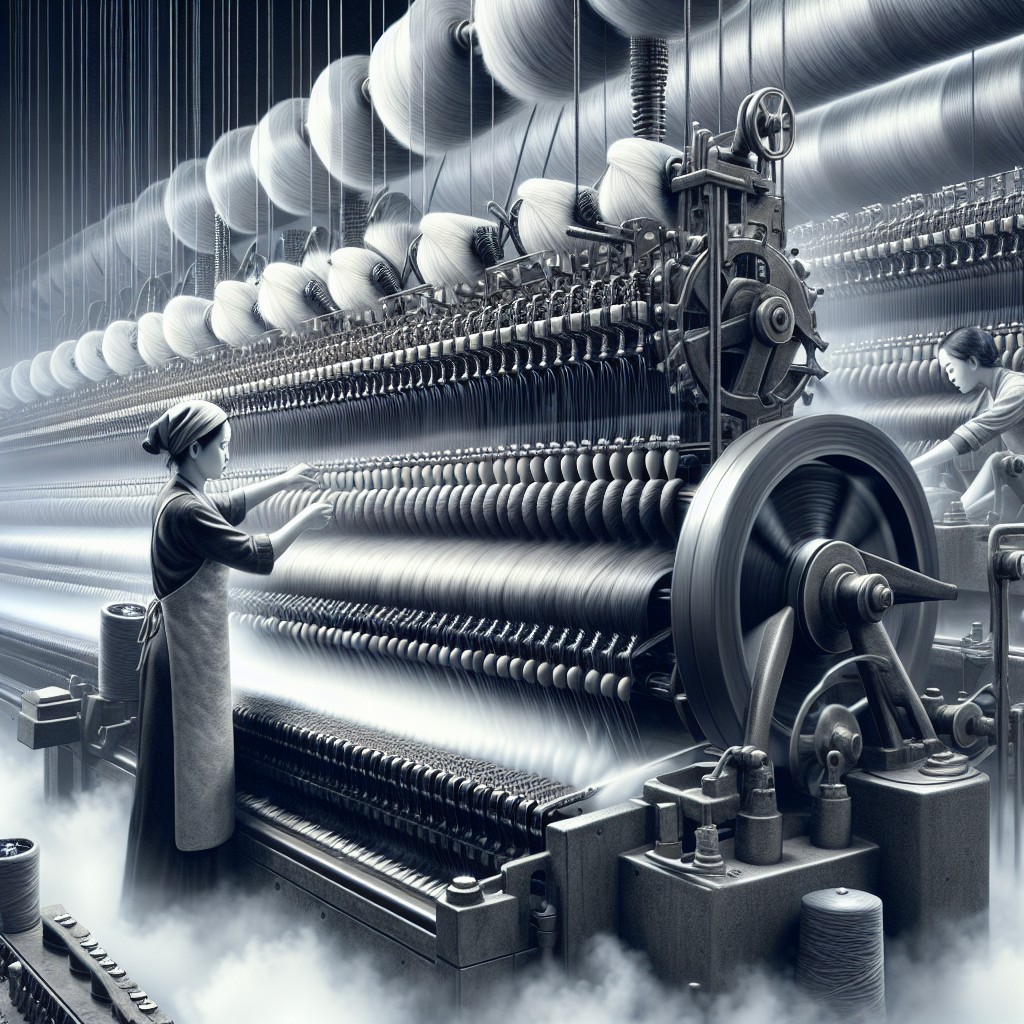
This method is commonly used to produce fibers such as rayon, acetate, and spandex. The wet spinning process allows for the production of high-quality fibers with excellent strength and durability.
During wet spinning, the dissolved polymer solution is forced through small holes called spinnerets into a chemical bath where it solidifies into long continuous filaments. The filaments are then washed to remove any residual chemicals before being dried and wound onto bobbins or cones ready for use.
One of the advantages of wet spinning over other methods like dry or melt-spinning is that it can be used with polymers that cannot withstand high temperatures without degrading. Wet-spun fibers also tend to have better dye uptake properties than those produced by other methods.
Dry Spinning
In this process, the polymer solution is first dissolved in a solvent to create a viscous liquid. The liquid is then forced through tiny holes called spinnerets into warm air chambers where it solidifies into fibers.
One advantage of dry spinning over other methods like wet spinning or melt-spinning processes is that it allows for greater control over fiber diameter and structure. This makes it possible to produce high-quality yarns with specific properties such as strength, durability, and softness.
Dry-spun yarns are commonly used in various applications including clothing fabrics like sportswear and outdoor gear due to their moisture-wicking capabilities. They are also used in industrial settings for filtration systems because they can be engineered with specific pore sizes.
Understanding the different types of yarn spinning systems can help you choose the perfect material for your project based on its unique characteristics.
Gel Spinning
This process involves dissolving polymer materials in a solvent to create a gel-like substance, which is then extruded through small holes and stretched into fibers. The resulting fibers are incredibly strong and durable, making them ideal for use in applications such as bulletproof vests, ropes, and cables.
One of the advantages of Gel Spinning is its ability to produce ultra-high molecular weight polyethylene (UHMWPE) fiber with exceptional strength-to-weight ratios. These UHMWPE fibers have been used extensively in military applications due to their lightweight yet robust nature.
Another benefit of Gel Spinning is its versatility when it comes to creating different types of fiber structures. By adjusting the spinning parameters such as temperature or humidity levels during production, manufacturers can tailor the properties of the final product according to specific needs.
Gel Spinning offers an innovative approach for producing high-performance yarns with superior strength characteristics compared to traditional methods like ring or rotor spinning systems.
Direct Spinning
In this method, fibers are fed directly into the drafting zone and twisted to form a continuous strand of yarn. Direct spinning is commonly used for producing high-quality cotton and woolen yarns.
One advantage of direct spinning is that it produces stronger, more uniform strands than other methods because there are fewer opportunities for breakage or inconsistencies in thickness. Since there’s no need to prepare fibers before they’re spun into thread or cordage as with other systems like ring-spinning or rotor-spun techniques – it saves time and money on processing costs.
However, one disadvantage of direct spinning can be its limited versatility when compared with some other types such as air-jet spinnings which allow greater flexibility in terms of fiber selection (e.g., synthetic vs natural) due to their ability to handle finer denier filaments better than most traditional methods including wet/dry/gel-based approaches alike.
Solution Spinning
In this method, the polymer solution is extruded through a spinneret into a coagulation bath where it solidifies and forms fibers. This spinning system produces high-quality yarns with excellent strength and durability.
The Solution Spinning process has been widely used in the production of synthetic fibers such as nylon, polyester, rayon, and acrylic. It allows for precise control over fiber diameter and properties by adjusting factors such as solution concentration, temperature, flow rate during spinning.
One advantage of Solution Spinning is that it can produce continuous filaments which are ideal for weaving fabrics without any seams or breaks in the material. These filaments can be textured to mimic natural fibers like silk or wool.
In recent years there have been advancements made in Solution Spinning technology including electrospun nanofibers which have unique properties due to their small size (less than 1000 nm). These ultra-fine fibers find applications in areas such as tissue engineering scaffolds and drug delivery systems.
Melt-Spinning Process
This process involves melting the polymer and then extruding it through small holes in a spinneret to create continuous filaments. The filaments are then cooled and solidified, resulting in long strands of fiber that can be used for various applications.
The Melt-Spinning Process is commonly used to produce nylon, polyester, and other synthetic fibers that are widely used in clothing, upholstery fabrics, carpets, ropes as well as industrial materials such as tire cords or conveyor belts.
One advantage of melt-spinning over other spinning methods is its ability to produce high-quality yarns with consistent properties at high production rates. This process allows for the creation of custom blends by combining different polymers during the melting stage.
Textile-Reinforced Concrete
It is made by combining cement with fibers, such as glass or carbon, to create a strong and durable material that can be used for various applications. The use of textile-reinforced concrete offers several advantages over traditional reinforced concrete, including increased flexibility and reduced weight.
One of the most significant benefits of using textile-reinforced concrete is its ability to withstand high levels of stress without cracking or breaking. This makes it an ideal choice for structures that are exposed to extreme weather conditions or heavy loads.
Another advantage of this innovative material is its versatility in design options due to its lightweight nature compared with traditional reinforced concrete which allows architects more freedom when designing buildings and other structures.
Biotextiles Manufacturing
These textiles can be used in wound dressings, surgical implants, drug delivery systems, and more. The process involves combining biocompatible materials with advanced weaving techniques to produce fabrics that are both strong and flexible.
One example of biotextile manufacturing is electrospinning – a technique where polymer solutions are spun into ultra-fine fibers using an electric field. These fibers can then be woven together to create complex structures such as scaffolds for tissue engineering or filters for air purification.
As technology continues to advance in this field, we can expect even more innovative uses for biotextiles in the future.
Synthetic Polymer Fibers
These fibers are made from synthetic materials such as polyester, nylon, and acrylic. They can be produced in various colors, textures, and thicknesses to suit different crafting needs.
Polyester is one of the most commonly used synthetic polymer fibers in yarn spinning. It is known for its strength and resistance to wrinkles, shrinking or stretching out of shape when washed or dried.
Polyester fiber also has excellent moisture-wicking properties that make it ideal for sportswear.
Nylon is another popular synthetic polymer fiber used in yarn production because of its high tensile strength which makes it suitable for creating strong fabrics like ropes or parachutes.
Acrylic fiber mimics wool’s softness but with added benefits such as being lightweight yet warm making it perfect for winter wearables like hats scarves gloves etcetera.
Ultra-Fine Fibers
These fibers are made using advanced spinning techniques, resulting in incredibly thin strands that can be used to create delicate and intricate designs.
One advantage of ultra-fine fibers is their softness. They feel luxurious against the skin, making them ideal for creating garments such as scarves, shawls, and sweaters.
Because they are so fine, they can be spun into longer lengths than thicker yarns without adding extra weight to your project.
Another benefit of ultra-fine fibers is their versatility. They come in a wide range of materials including wool blends or silk blends which makes them suitable for different types of projects like lacework or even baby clothes.
While these types may seem fragile due to their fineness but with proper care instructions followed during washing and drying process it will last long enough just like any other fiber.
Centrifugal Melt Electrospinning
This process involves melting the polymer and then using centrifugal force to spin it into fibers, which are then collected on a rotating drum. The resulting fibers have unique properties such as high strength, flexibility, and durability.
This method of yarn spinning has many potential applications in various industries such as aerospace, automotive manufacturing, medical devices production and more. For example, Centrifugal Melt Electrospinning can be used to create ultra-fine fibers for air filtration systems or protective clothing materials with enhanced resistance against extreme temperatures.
As we continue exploring different types of yarn spinning systems in this article series about crocheting and knitting crafts-related topics; it’s essential to understand how each system works so you can choose the right type of yarn for your project needs.
Porous Metals Production
This process involves using a metal powder and a binder to create a slurry that is then spun into fibers. These fibers are then sintered together to form a solid, yet porous, metal structure.
The resulting material has unique properties such as high strength-to-weight ratio and excellent thermal conductivity, making it ideal for use in aerospace and automotive industries.
As we can see from this example, spinning technology has far-reaching applications beyond just yarn production.
Advanced Polyimide Fibers
These fibers are known for their high strength, excellent thermal stability, and resistance to chemicals and radiation. They can be used in various applications such as aerospace, electronics, and protective clothing.
In the world of yarn spinning systems, advanced polyimide fibers offer exciting possibilities for creating new types of yarn with exceptional characteristics. The process involves converting these ultra-strong fibers into yarn through various spinning methods such as dry or wet spinning.
The resulting polyimide fiber-based yarns have outstanding mechanical properties that make them ideal for use in extreme environments where other materials may fail. For example, they can withstand temperatures up to 500°C without losing their strength or flexibility.
As technology continues to advance rapidly across different industries globally; it is expected that more innovative uses will emerge from this material’s potential capabilities.
Conversion of Fiber to Yarn
The process of converting fiber to yarn involves several steps, including cleaning and carding the fibers to remove any impurities and align them in a parallel fashion. Next, the fibers are drawn out into long strands called rovings.
The rovings are then twisted together using one of several spinning systems to create a continuous strand of yarn. Each spinning system has its unique characteristics that affect the texture, strength, and appearance of the resulting yarn.
Ring spinning is one common method where thin strands from multiple bobbins pass through rollers that twist them together as they wind onto a spindle. Rotor spinning uses an open-ended rotor with teeth on its surface that draw in loose fiber ends while rotating at high speeds.
Air-jet spinning uses compressed air streams to wrap individual staple fibers around each other rapidly while Wet Spinning involves dissolving polymer materials such as cellulose acetate or viscose rayon into liquid form before extruding it through spinnerets which solidify upon contact with water. Dry Spinning is another method where polymers dissolved in solvents like dimethylformamide (DMF) get spun by evaporating solvent molecules under controlled conditions.
Gel Spinning produces strong synthetic fibres by drawing gel-like solutions made up mostly from polyethylene chains across small holes at high speed. Direct Spinning combines both wet-spinning and dry-spinning techniques for producing acrylic fibres directly without intermediate processing stages like washing off residual chemicals after production Solution-Spinning creates ultra-fine fibres using electrospun nanofibers technology which applies electric fields between two electrodes immersed within polymer solutions containing charged particles suspended inside them.
Melt-Spinning Process melts thermoplastic polymers down until their viscosity drops low enough for extrusion through spinnerets creating filaments suitable for textile applications.
The conversion of fiber to yarn is a complex process that requires precision and expertise.
Spinning Methods Review
The most common method is called “worsted” spinning, which produces a smooth and strong yarn by aligning fibers parallel to each other before twisting them tightly. Another popular method is “woolen” spinning, which creates a softer and loftier yarn by allowing fibers to remain more jumbled before being twisted together.
Other methods include semi-worsted and semi-woolen techniques that combine aspects of both worsted and woolen processes. There are specialized techniques such as slub or boucle that create unique textures within the finished product.
Understanding these different methods can help you choose the perfect type of spun yarn for your project based on its desired texture, strength or softness requirements.
Experimental Studies
Researchers have investigated various factors such as fiber properties, processing parameters, and machine settings to optimize the quality and performance of yarns produced by different spinning methods. These studies have led to significant advancements in the field of textile manufacturing, resulting in new types of fibers with improved strength, durability, and other desirable characteristics.
For example, researchers at North Carolina State University developed a novel method for producing ultra-fine fibers using centrifugal melt electrospinning. This technique involves melting polymer pellets under high-speed rotation before extruding them through a spinneret into an electric field that stretches them into ultra-fine fibers.
The resulting fibers are stronger than those produced by traditional electrospinning methods.
Other experimental studies focus on developing biotextiles for medical applications or creating advanced polyimide fibers for aerospace engineering purposes. By exploring new materials and techniques through experimental research projects like these ones mentioned above can lead us towards more efficient production processes while also improving product quality.
Applications and Future Trends
The type of spinning system used can greatly affect the properties of the resulting yarn, such as strength, durability, and texture. For example, ring-spun cotton is a popular choice for soft and comfortable clothing items like t-shirts or bed sheets.
As technology advances in textile manufacturing processes continue to evolve rapidly; new trends emerge that could revolutionize how we produce textiles. One such trend is 3D printing with fibers which allows for intricate designs that were previously impossible using traditional methods.
Another emerging trend in yarn spinning systems is sustainable production practices. With an increasing focus on environmental responsibility across industries worldwide; there has been a growing demand for eco-friendly textiles made from recycled materials or natural fibers like bamboo or hemp.
Terminology in Spinning
Here are a few terms you may come across as you explore this fascinating craft:.
- Fiber: The raw material used to make yarn. Fibers can be natural (such as wool or cotton) or synthetic (such as acrylic or nylon).
- Drafting: The process of pulling fibers out and aligning them before they are spun into yarn.
- Twist: The amount of twist added to the fibers during spinning determines the strength and texture of the resulting yarn.
- Ply: Two or more strands of twisted fiber that have been plied together create a stronger, thicker strand called ply.
- Understanding these basic terms will help you better comprehend how each type of spinning system works and what makes each one unique. So let’s continue our exploration by diving into ring spinning!
FAQ
What are the 4 types of spinning?
The 4 types of spinning are ring-spun, rotor-spun, twistless, and wrap-spun.
What are the three types of spinning?
The three main types of spinning processes are melt spinning, dry solution spinning, and wet solution spinning.
What are the three techniques of yarn spinning?
The three techniques of yarn spinning are ring spinning, open-end (rotor) spinning, and air-jet spinning.
What are the new spinning methods?
The new spinning methods include rotor, air-jet, friction, vortex, electrostatic, core, wrap, twistless spinning, and others.
What are the main differences between the 4 types of spinning systems?
The main differences between the 4 types of spinning systems are: Ring spinning (traditional process, high quality yarn), Rotor spinning (high productivity, less yarn strength), Air-jet spinning (using air vortex, speed and flexibility), and Friction spinning (using friction drums, thicker yarn production).
How does the quality of yarn vary between different spinning techniques?
Quality of yarn varies between different spinning techniques as different techniques produce diverse fiber arrangements, twists, and properties, affecting overall yarn attributes.
What impact does the choice of spinning method have on the final textile product?
The choice of spinning method impacts the final textile product’s quality, strength, cost, and appearance.