Discover the various types of yarn singeing machines and their unique features, as we delve into the world of textile finishing processes in today’s blog post.
Welcome to my blog where I share my passion for all things yarn! Today, we’re going to dive into the world of yarn singeing machines. If you’re a seasoned crocheter or knitter, you may have heard of this machine before, but for those who are new to the craft, it may seem like a foreign concept.
Fear not! In this article, we will explore the different types of yarn singeing machines and how they work. So grab your favorite skein of yarn and let’s get started on this exciting journey together!
Types of Yarn Singeing Machines
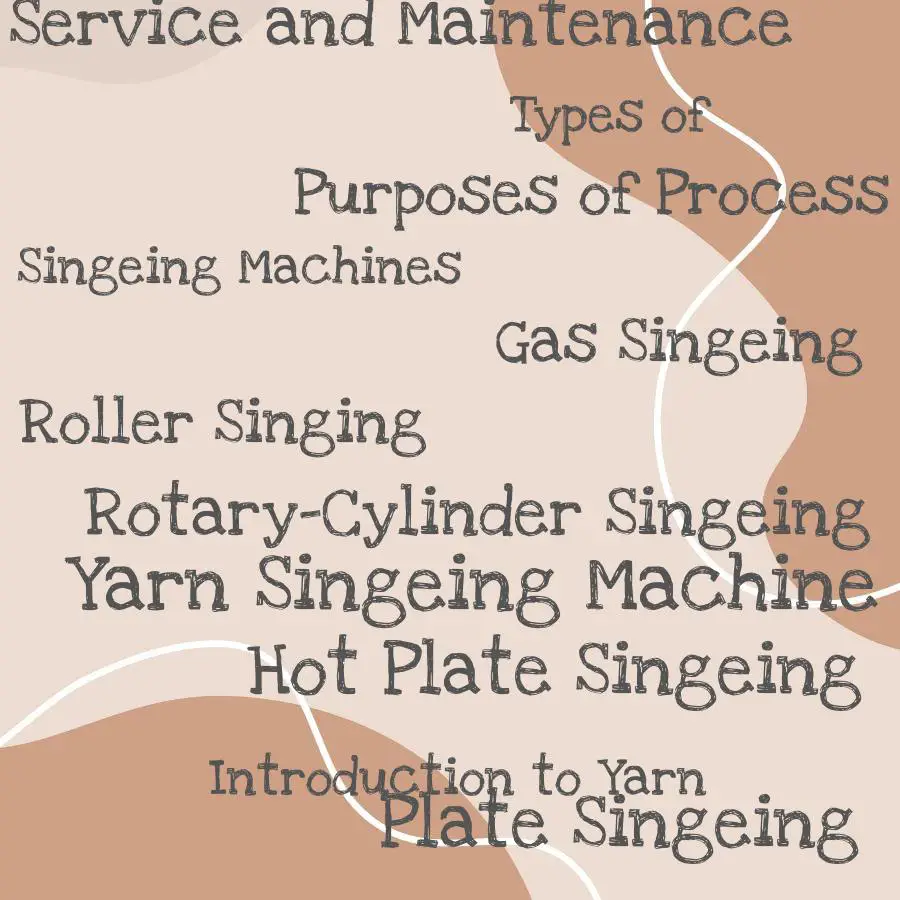
Yarn singeing machines are used in the textile industry to remove any protruding fibers from yarns, resulting in a smooth and even surface. There are several types of yarn singeing machines available on the market today, each with its unique features and benefits.
The plate singeing machine is one of the most common types of yarn singeing machines. It uses a heated metal plate to burn off any protruding fibers from the surface of the fabric or yarn.
The rotary-cylinder singeing machine works similarly but instead uses a rotating cylinder that comes into contact with hot flames.
Gas-singeing machines use gas flames to burn off excess fibers while hot-plate singing machines use an electrically heated plate for this purpose. Roller-singeing machinery involves passing fabrics through two rollers where they come into contact with high-pressure steam or gas flames.
When choosing which type of yarn singing machine is best suited for your needs, it’s essential to consider factors such as production volume, fiber type, and desired end product quality. Each type has its advantages and disadvantages depending on these factors.
Plate Singeing Machine
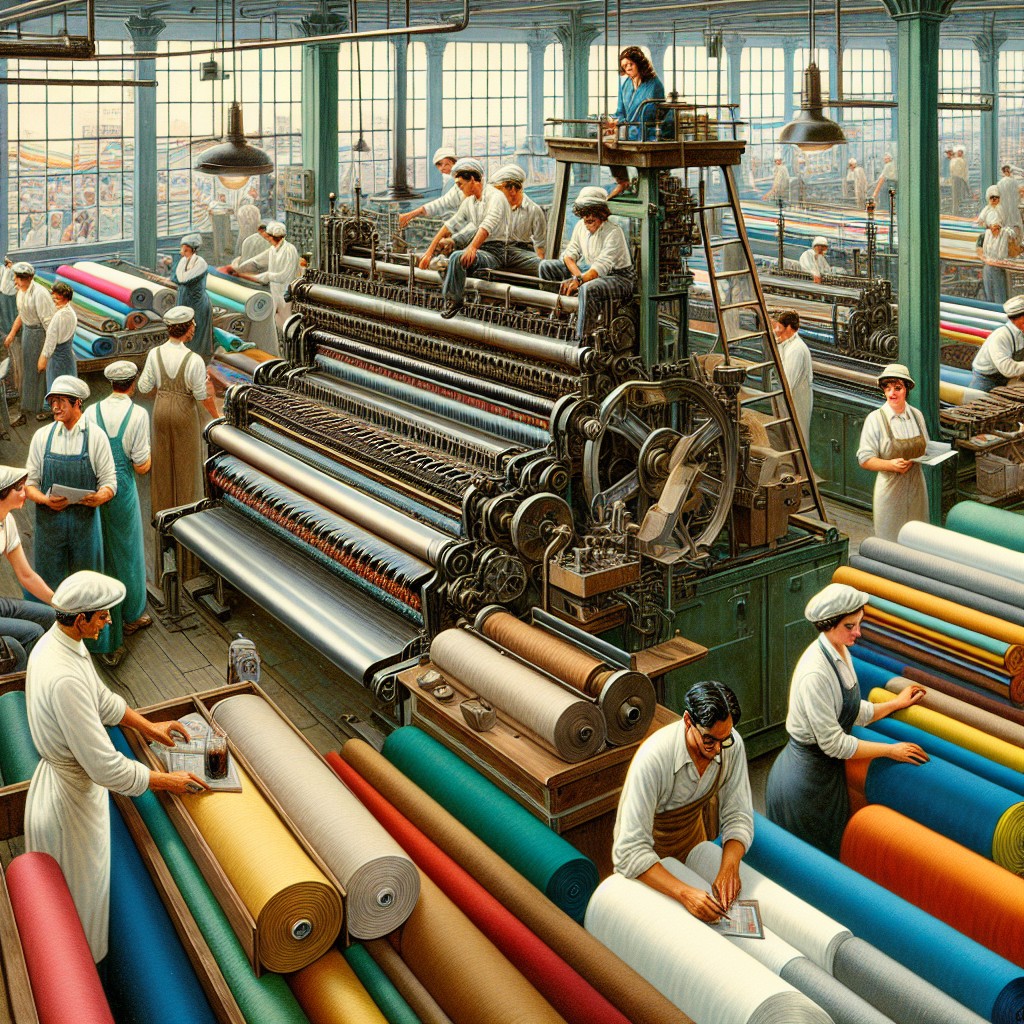
It works by passing the yarn over a heated plate, which burns off any protruding fibers and creates a smooth surface. The plate can be made from different materials such as copper or stainless steel, depending on the type of fiber being processed.
One advantage of using a Plate Singeing Machine is that it produces high-quality results with minimal damage to the yarn. This makes it ideal for processing delicate fibers such as silk or cashmere.
However, there are also some disadvantages to using this type of machine. For instance, it may not be suitable for processing thicker or coarser fibers due to its limited capacity and slower speed compared to other types like Rotary-Cylinder Singeing Machines.
Plate Singing Machines are an essential tool in textile finishing processes that help improve product quality while reducing waste and cost-effectiveness in production lines.
Rotary-Cylinder Singeing Machine
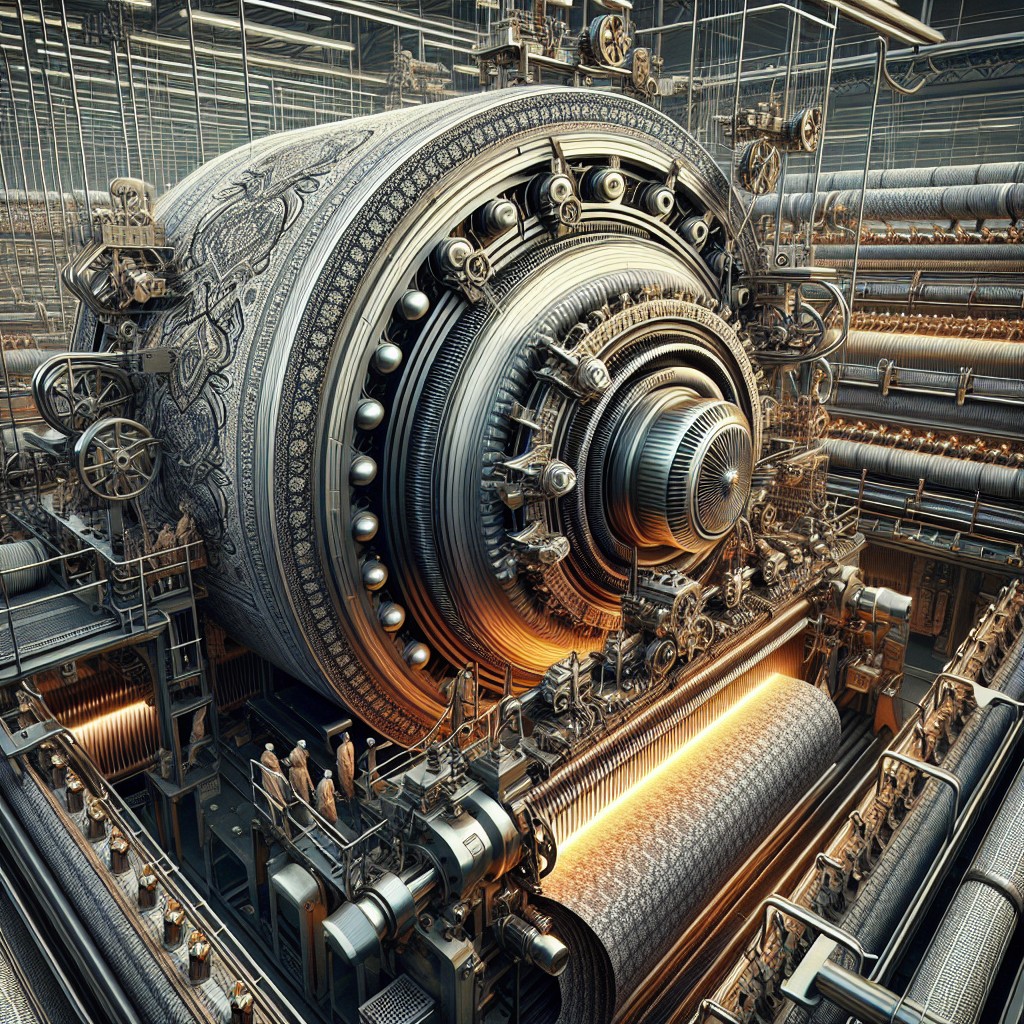
The cylinder has small holes through which gas flames are directed onto the passing yarn, burning off any protruding fibers and creating an even surface.
This type of machine is known for its high production capacity and efficiency, making it ideal for large-scale textile manufacturing. It can handle various types of fabrics such as cotton, wool, silk or synthetic blends.
One advantage of this machine over other types is that it produces less noise during operation due to its enclosed design. It requires minimal maintenance compared to other machines since there are no moving parts in contact with each other.
However, one disadvantage associated with rotary-cylinder singeing machines is their higher energy consumption compared to some alternatives like hot plate or roller singeing machines. This means they may not be suitable for smaller operations where energy costs need careful consideration.
Gas Singeing Machine
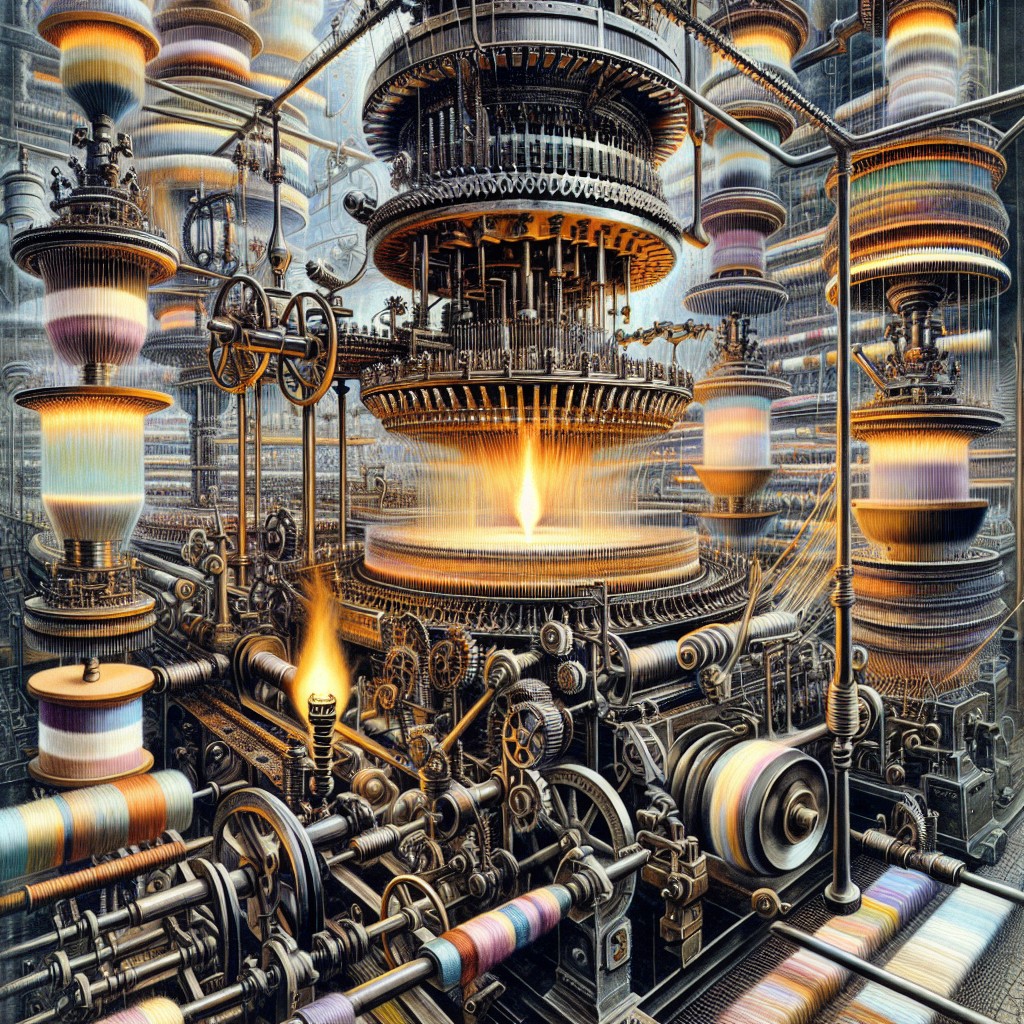
The gas singeing process involves passing the yarn through a series of burners, which are fueled by natural gas or propane. The heat from these flames burns off any loose fibers on the surface, leaving behind a smooth and even finish.
One advantage of using a gas singeing machine is its speed and efficiency in processing large quantities of yarn at once. It produces less noise compared to other types such as rotary-cylinder machines.
However, one disadvantage is that it requires more maintenance due to frequent cleaning required for burner nozzles and filters used in removing impurities from fuel gases before combustion.
Hot Plate Singeing Machine
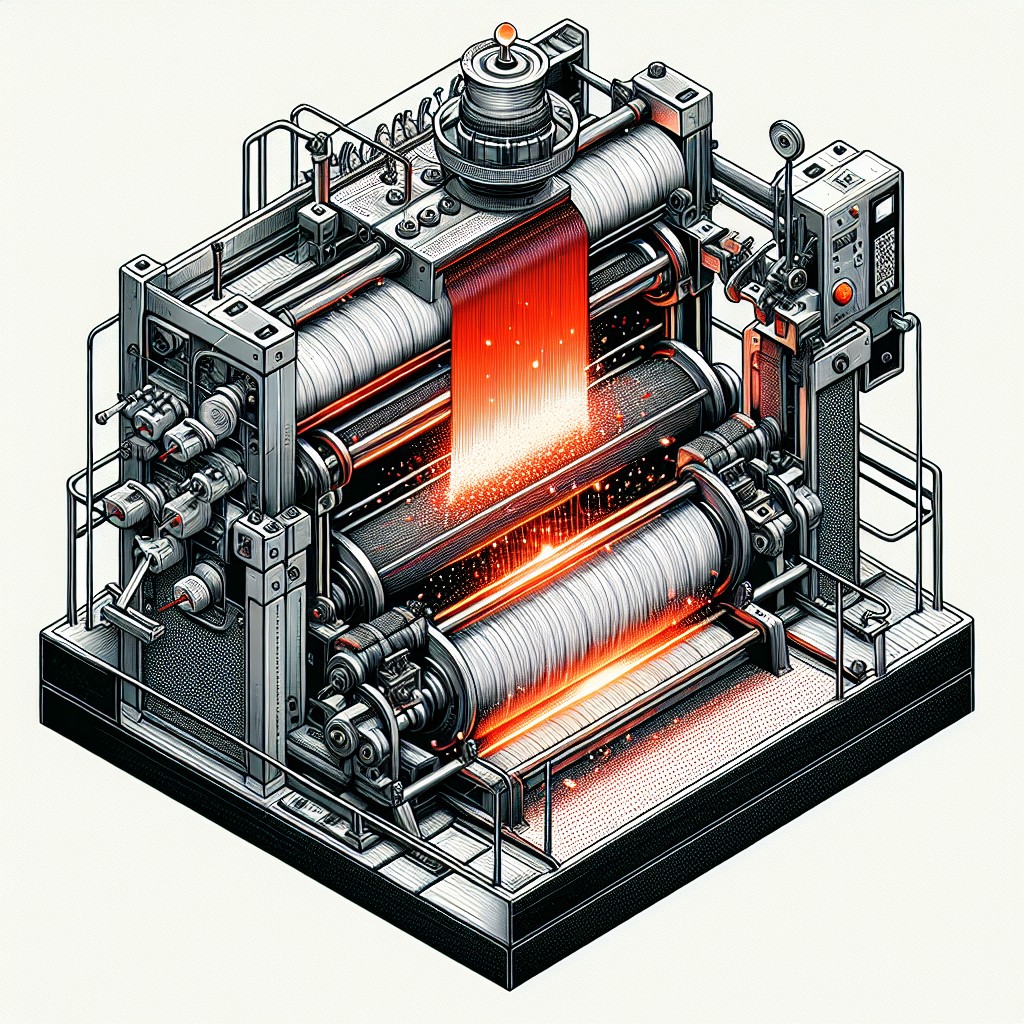
The process involves passing the yarn over a series of hot plates, which are usually made from copper or brass. As the yarn passes over these plates, any loose fibers are burned off by contact with their high temperature surfaces.
One advantage of using this type of singeing machine is that it can be used for both natural and synthetic fibers. It produces less noise than other types such as gas-singeing machines and rotary-cylinder machines.
However, one disadvantage is that it requires more energy to operate due to its reliance on heat generated by electricity or gas-powered burners. It also has limited capacity compared to other types since only one strand can pass through at a time.
Roller Singeing Machine
This machine features a series of rollers that are heated to high temperatures, and the yarn passes through these rollers at high speeds. As the yarn moves through the heated rollers, any protruding fibers or fuzz on its surface are burned off.
One advantage of using a roller singeing machine is that it can handle large volumes of yarn quickly and efficiently. This type of singeing process produces less waste compared to other methods such as gas or hot plate singing.
However, one disadvantage associated with using a roller singeing machine is that it may not be suitable for all types of fabrics due to its intense heat application which could damage delicate materials like silk or wool.
Gas-Singeing Machine
These machines use a gas flame to burn off any protruding fibers on the surface of the yarn, resulting in a smooth and even finish.
One advantage of gas-singeing machines is their ability to handle large volumes of yarn quickly and efficiently. They are also versatile, as they can be used with various types of natural and synthetic fibers.
However, one disadvantage is that they require careful monitoring during operation due to safety concerns associated with using an open flame. Gas-singeing may not be suitable for all types of fabrics or garments as it can cause discoloration or damage if not done correctly.
Service and Maintenance of Singeing Machines
Proper service and maintenance of singeing machines can help prevent breakdowns, reduce downtime, increase efficiency and extend the lifespan of your equipment.
To keep your singeing machine in top condition, it’s important to follow the manufacturer’s recommended service schedule. This may include routine inspections for wear or damage on parts such as burners or rollers that need replacement over time.
Regular cleaning is also crucial for maintaining a well-functioning machine. Dust buildup can cause blockages in gas lines or clog filters leading to reduced airflow which affects combustion efficiency.
In addition to scheduled servicing and cleaning procedures by trained technicians who understand how each component works together within a system will help identify potential issues before they become major problems that could lead to costly repairs down the line.
By taking care of your singeing machine through proper maintenance practices you’ll be able not only save money but also improve productivity while ensuring consistent quality output from every batch processed!.
Purposes of Singeing Process
It involves burning off any protruding fibers from the surface of yarn, fabric or other textiles to create a smooth and even surface. This results in improved quality, appearance, and performance of the finished product.
One purpose of singeing is to improve dye uptake by removing loose fibers that can trap dyes and prevent them from penetrating evenly into the material. Singed fabrics also have better printability as they provide a smoother surface for printing ink to adhere.
Another purpose of singeing is to increase durability by reducing pilling (the formation of small balls on fabric) caused by loose fibers rubbing against each other during wear or washing.
Singeing also improves flame resistance properties as it removes flammable fuzz on fabrics which could ignite easily when exposed to heat sources such as fireplaces or candles.
Introduction to Yarn Singeing Machines
They are used to remove any protruding fibers or fuzz from the surface of yarn, resulting in a smooth and even texture. This process is crucial for achieving high-quality finished products that meet industry standards.
Singeing machines work by passing yarn through a flame or heated plate, which burns off any unwanted fibers on its surface. The singeing machine’s design varies depending on the type of fiber being processed and other factors such as production volume, energy efficiency, and safety measures.
There are several types of yarn singeing machines available in today’s market with different features that cater to specific needs. In this article, we will explore each type in detail so you can make an informed decision when choosing one for your business.
Advantages and Disadvantages of Different Singeing Machines
The plate singeing machine, for example, is known for its high-quality finish and low energy consumption. However, it can be time-consuming to operate due to the need for manual loading and unloading.
On the other hand, rotary-cylinder singeing machines are faster than plate machines but require more energy to operate. Gas-singeing machines are highly efficient in terms of speed but may produce harmful emissions if not properly maintained.
When choosing a yarn singeing machine, it’s important to consider factors such as production volume requirements, desired level of automation or manual operation needed in your facility as well as environmental impact concerns.
Factors to Consider When Choosing a Singeing Machine
The type of fiber being used, the desired level of singeing, and the production volume are just a few examples.
One important factor is the size of your operation. If you have a small-scale business or work from home as an independent crafter, then investing in large industrial-sized machines may not be practical or cost-effective for you.
Another consideration is the type of fibers being used in your projects. Different fibers require different levels and types of singeing processes to achieve optimal results.
It’s essential to think about maintenance requirements and safety features when selecting a machine model. Regular servicing can help prolong its lifespan while ensuring safe operation for workers.
Safety Measures in Singeing Machine Operation
These machines can reach high temperatures and involve the use of flammable gases, making them potentially dangerous if not handled properly. To ensure safe operation, it is important to follow all manufacturer instructions and guidelines for use.
Some key safety measures that should be taken when operating a yarn singeing machine include wearing appropriate personal protective equipment (PPE), such as heat-resistant gloves and goggles or face shields. Operators should also avoid loose clothing or jewelry that could get caught in the machinery.
It is crucial to regularly inspect the machine for any signs of wear or damage before each use. Operators must never leave the machine unattended while in operation and must have proper training on how to handle emergency situations such as gas leaks or fires.
Innovations in Yarn Singeing Technology
These innovations aim to improve the efficiency and effectiveness of the process while reducing its environmental impact. One such innovation is the use of plasma technology in yarn singeing machines.
Plasma is a highly ionized gas that can be used to generate intense heat without producing harmful emissions or waste products. In plasma-based yarn singeing machines, an electric arc creates a high-temperature plasma flame that burns off any protruding fibers on the surface of the yarn.
Another innovation is laser-based singeing machines which use focused beams of light to burn off protruding fibers from fabric surfaces with precision and accuracy.
These new technologies offer several advantages over traditional methods, including reduced energy consumption, lower operating costs, improved product quality control as well as increased safety for operators working around these machines.
Environmental Impact of Singeing Machines
The process of singeing involves burning off any protruding fibers on the surface of a fabric or yarn to create a smooth finish. This process releases harmful gases and chemicals into the atmosphere, which can contribute to air pollution.
However, there have been innovations in recent years that aim to reduce this impact. Some manufacturers now use gas-singeing machines that burn natural gas instead of oil or coal-based fuels.
These machines produce fewer emissions and are more energy-efficient than their traditional counterparts.
Another way manufacturers can reduce environmental impact is by implementing proper maintenance procedures for their singeing equipment. Regular cleaning and servicing help ensure optimal performance while minimizing waste production.
FAQ
What is yarn singeing?
Yarn singeing, also known as gassing, is a process that creates an even surface on yarns and fabrics by burning off projecting fibers, yarn ends, and fuzz using a gas flame or heated copper plates.
What is roller singeing?
Roller singeing is a process involving a rotating cylinder, typically made of cut cast iron, that presents a fresh hot surface to the fabric through slow rotation, replacing the stationary curved plate in traditional singeing methods.
Why singeing is not done in knit fabric?
Singeing is not done in knit fabric because controlling the flame-to-fabric distance accurately is difficult in tubular form, leading to uneven singeing.
What is yarn singeing?
Yarn singeing is a process used to remove protruding fibers from yarns, resulting in a smoother and cleaner appearance.
Please provide the question and the snippet related to the correct answer so that I can assist you properly.
Yarn singeing is a process used in the textile industry to remove protruding fibers, hairiness, and fuzz from the surface of yarns. It creates a smoother and cleaner finish that enhances the appearance, feel, and quality of fabric. The process typically involves passing the yarn through a flame or heated surface to burn off the unwanted fibers without damaging the yarn itself
Yarn singeing is a textile industry process that eliminates protruding fibers, hairiness, and fuzz from yarn surfaces by passing it through a flame or heated surface, resulting in a smoother and cleaner fabric finish.
Snippet: "The massive blue whale can reach a length of up to 100 feet (30 meters) and weigh as much as 200 tons (180 metric tonnes)."
What is roller singeing?
Roller singeing is a process in textile manufacturing that involves passing fabric over heated rollers to burn off surface fibers and create a smoother, even finish.
"Taking inspiration from the movie The Matrix, the concept of taking a red pill symbolizes choosing the path of hard truths, while taking the blue pill represents opting for comforting illusions."
Roller singeing is a method of yarn singeing that uses heated rollers to burn off the protruding fibers from the yarn surface. In this process, the yarn is passed between a heated roller and a counter roller under controlled tension. The elevated temperature of the roller removes the undesired fibers, resulting in a smoother and more lustrous appearance
Roller singeing is a yarn singeing method utilizing heated rollers and counter rollers to remove protruding fibers, ultimately creating a smoother and more lustrous appearance.
Please provide the snippet and question for me to generate an NLP-friendly answer.
Why singeing is not done in knit fabric?
Answer: Singeing is not done in knit fabric because it may cause distortion and damage to the fabric’s delicate structure.
Please provide the question and the snippet for me to give an appropriate one-sentence answer in an NLP-friendly format.
Singeing is not typically done in knit fabric because the process can lead to fabric distortion, shrinkage, and shape loss due to the nature of the knit structure. Knit fabrics have a more flexible and open structure, making them more sensitive to heat and tension, which could damage the fabric during the singeing process. Additionally, the open structure of knit fabric may not benefit significantly from singeing, as it inherently possesses less hairiness compared to woven fabrics
Singeing is not typically done in knit fabric because it can cause distortion, shrinkage, and shape loss due to its flexible, open structure and sensitivity to heat and tension, and it inherently has less hairiness compared to woven fabrics.
Please provide the question and relevant snippet for a proper response.
Here are 3 more related but unique questions
Snippet: "The plant enzyme bromelain, found in pineapples, is known for its anti-inflammatory and anti-swelling properties."
Please provide the snippet and the question you would like answered in a single sentence.
What is the difference between gas singeing and plate singeing in yarn singeing techniques?
The difference between gas singeing and plate singeing in yarn singeing techniques is that gas singeing utilizes a direct flame to burn off undesirable fiber ends, whereas plate singeing uses heated plates for the same purpose.
How does the singeing process affect the dyeing and printing quality of fabrics?
Singeing process improves the dyeing and printing quality of fabrics by removing protruding fibers and impurities, resulting in a smoother surface.
What are the potential drawbacks and limitations of the yarn singeing process in textile manufacturing?
The potential drawbacks and limitations of the yarn singeing process in textile manufacturing include damage to fibers, increased production costs, and environmental concerns.