Discover the fascinating world of yarn winding as we explore its various types and techniques, perfect for both beginners and seasoned enthusiasts.
Are you a yarn enthusiast who loves to experiment with different types of yarn for your knitting or crocheting projects? Then, you must be aware of the importance of yarn winding. Yarn winding is a crucial step in preparing your yarn before starting any project, as it helps to organize and manage the strands of yarn.
In this blog post, we will explore the various types of yarn winding techniques that can help you achieve different effects in your projects. From center-pull balls to cakes and skeins, we will cover it all! So, grab your favorite cuppa and let’s dive into the world of yarn winding!
What Is Winding
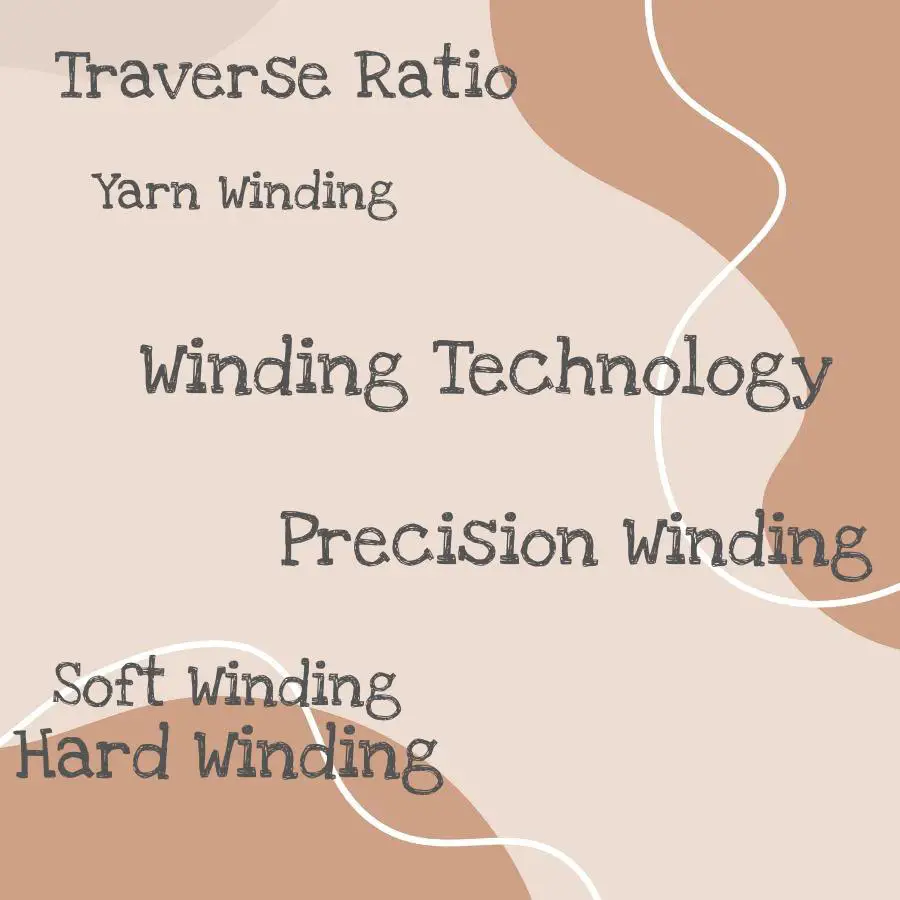
Winding is the process of transferring yarn from one package to another, which makes it easier to handle and use in knitting or crocheting projects. The primary purpose of winding is to organize the strands of yarn into a more manageable form that can be easily used without tangling or knotting.
There are two types of winding: soft and hard.
Soft Winding involves creating a loose ball-shaped package that allows for easy unwinding while working on your project. Soft-wound packages are typically used for hand-knitting, as they allow you to pull out just enough yarn without causing any tangles or knots.
Hard Winding creates tightly wound cylindrical packages with flat ends known as cones, tubes, bobbins, spools among others depending on their shape and size. Hard-wound packages are commonly used in industrial settings where large quantities of thread need to be dispensed quickly and efficiently.
Soft Winding
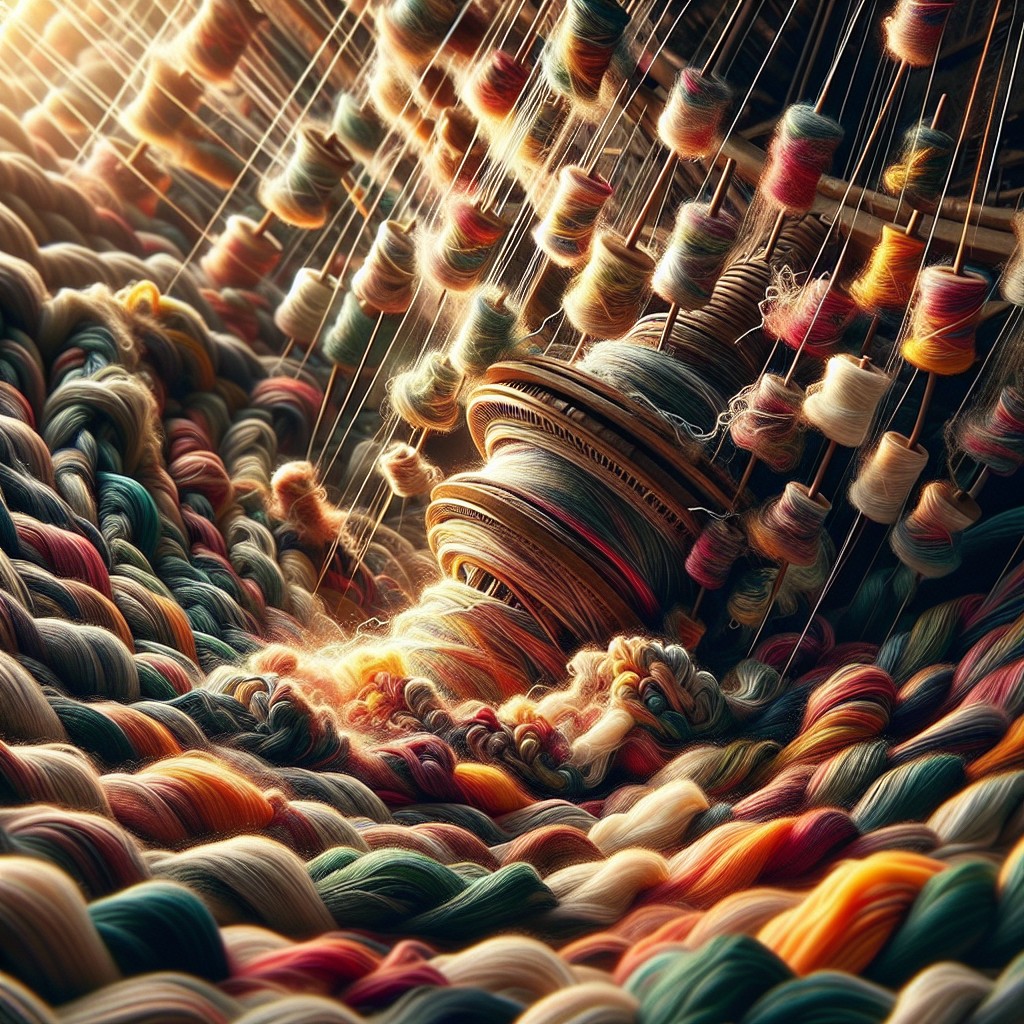
This type of winding is achieved by using low tension during the winding process, which results in a package with less density and more air between the layers of yarn. Soft wound packages are ideal for knitting or crocheting projects that require a softer texture, such as baby blankets or scarves.
One advantage of soft-wound packages is that they can be easily unwound from the center without tangling or knotting. This makes them convenient to use for both hand-knitting and machine-knitting processes.
However, there are some common defects associated with soft-wound packages such as loose edges, uneven tension distribution across layers leading to variations in diameter along length etc., which can affect their quality if not addressed properly during production.
To ensure high-quality output while producing soft wound yarns it’s important to maintain optimal parameters like traverse speed ratio (TSR), take-up speed ratio (USR), package build-up rate etc., throughout production.
Hard Winding
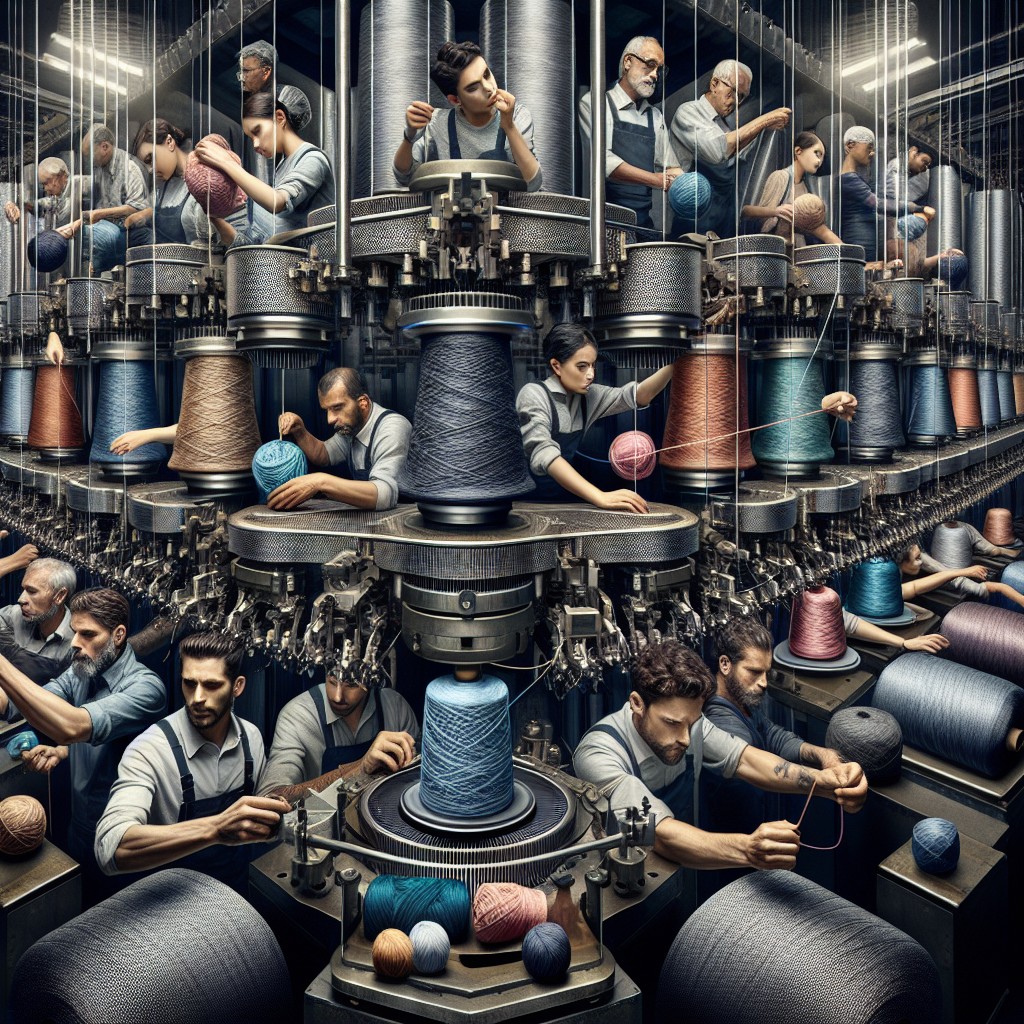
This method is commonly used for synthetic and filament yarns, as they require more tension during the winding process to prevent tangling and snarling. Hard-wound packages are also preferred when the yarn needs to be transported over long distances or stored for extended periods.
The hard-winding process involves applying high tension on the yarn while it’s being wound onto a cylindrical package. The resulting package has smooth edges with no loose ends, making it easier to handle during further processing.
However, there are some drawbacks associated with hard-wound packages too. They can cause abrasion in knitting machines due to their tightness and may lead to breakage of delicate fibers like silk or wool if not handled carefully.
Terminologies Related to Winding Technology
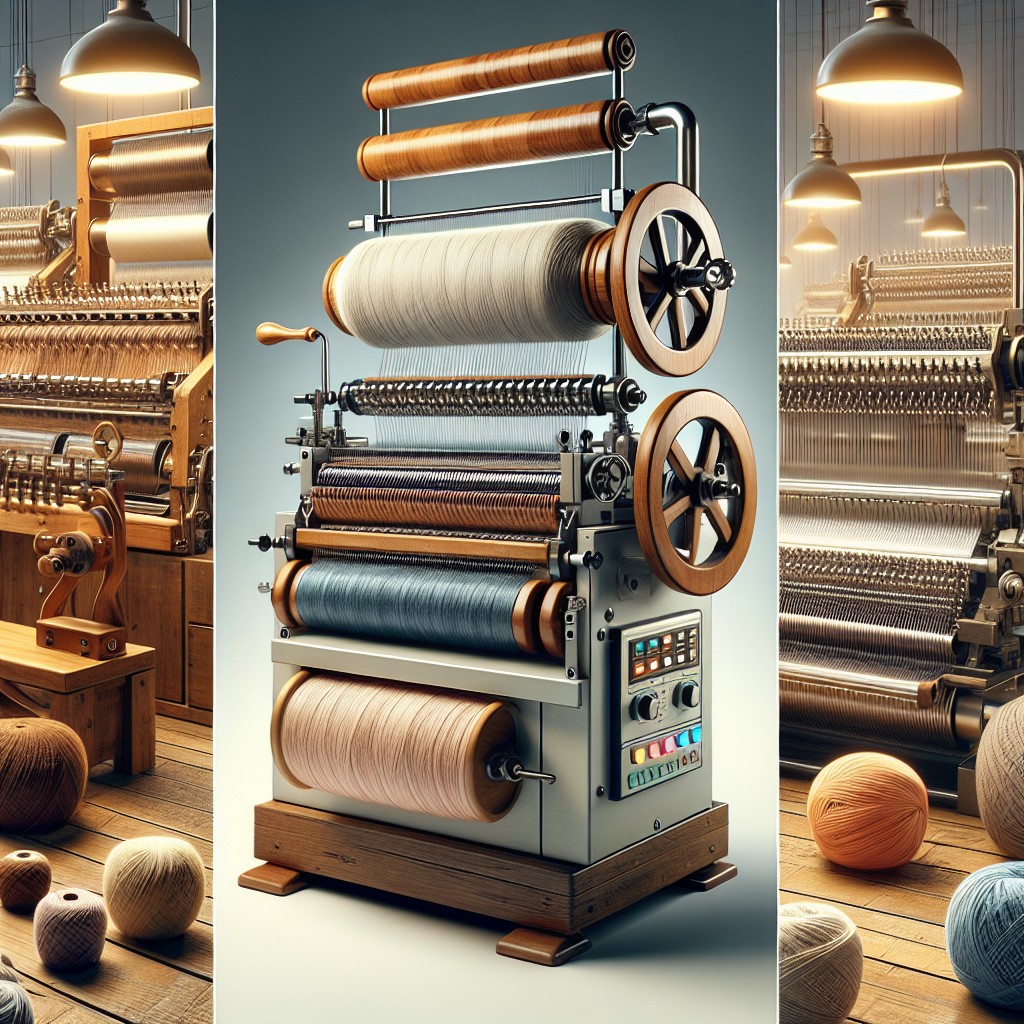
These terms will help you better understand the process and make informed decisions when selecting a particular type of yarn or technique.
Winding Angle: It is defined as the angle between the package axis and traverse guide movement direction.
Crossing Angle: The crossing angle is formed by two adjacent coils’ axes in a cross-wound package.
Coil Angle: Coil angle refers to an individual coil’s inclination with respect to its longitudinal axis in precision winding.
Winding Ratio: It is defined as Package Speed/Traverse Speed.
Traverse Ratio (or Pitch): Traverse ratio defines how many times one complete traverse cycle covers on one layer of wound material along with its lengthwise direction.
Wind per Double Traverse (WPDT): WPDT indicates how much thread has been wound onto each bobbin during each double traverse cycle.
Traverse Length (TL): TL represents how far across from side-to-side your machine moves while making one pass over your fabric or thread spool during sewing operations.
Winding Angle
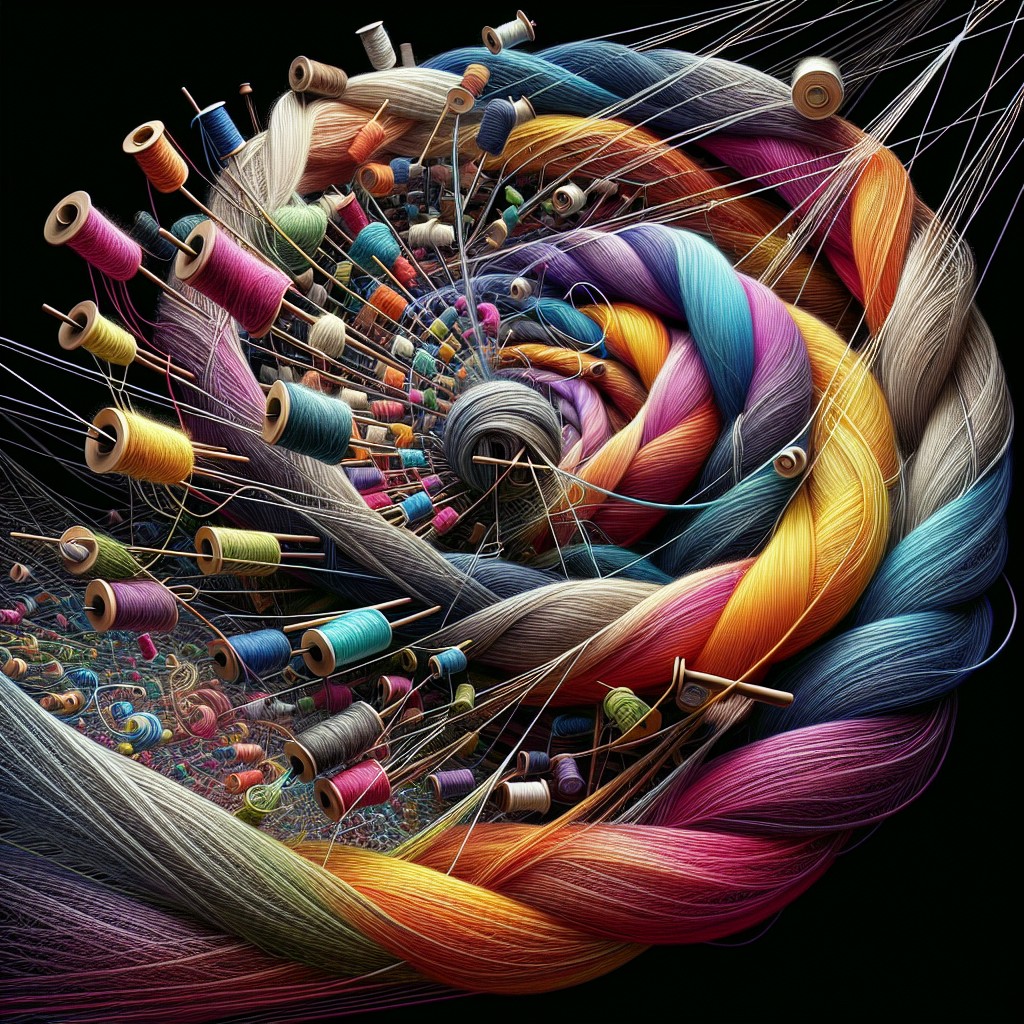
It refers to the angle between the yarn and the package’s axial direction during winding. The Winding Angle plays a crucial role in determining how tightly or loosely wound your yarn will be on your package.
The Winding Angle can vary depending on several factors, such as machine speed, tension settings, and type of material being wound. A higher winding angle results in tighter packing of fibers while a lower one leads to looser packing.
In general, it is recommended that you maintain a consistent Winding Angle throughout your project for uniformity and consistency. However, some projects may require variations in this parameter for specific effects or patterns.
Understanding how different parameters affect each other can help you achieve better control over your final product’s quality when using various types of yarns with different counts or textures.
Crossing Angle
It refers to the angle between the yarn path and the package surface, which affects package density, shape, and stability. The crossing angle can be adjusted by changing various parameters such as traverse length or speed.
In soft winding techniques like ball-winding or cake-winding, a small crossing angle is preferred to achieve a stable center-pull ball or cake without any tangles. On the other hand, hard winding techniques like cone-winding require larger angles for better package density and shape.
It’s crucial to select an appropriate crossing angle based on your project requirements and type of yarn used. A wrong choice may result in defects such as uneven tension distribution across packages leading to poor quality fabric production.
Coil Angle
It refers to the angle between adjacent coils on a package, which can be measured using a protractor or calculated mathematically. The coil angle affects several properties of wound packages such as density, stability, and unwinding behavior.
In soft winding techniques like ball-winding or cake-winding, a larger coil angle is preferred as it results in softer packages with better elasticity. On the other hand, hard winding techniques like cone-winding require smaller coil angles for producing stable and compact packages suitable for high-speed weaving machines.
The choice of coil angle depends on various factors such as yarn count, fiber type, machine speed among others. A wrong selection can lead to defects like uneven tension distribution across the package surface or formation of hard edges at sharp corners.
Winding Ratio
It is calculated as the ratio of surface speed to winding speed and plays a crucial role in determining package density, shape, and size. The Winding Ratio can be adjusted according to specific requirements for different types of yarns.
For instance, if you are working with fine or delicate threads such as silk or laceweight wool, you may need a higher Winding Ratio to achieve better tension control and prevent breakage during knitting or crocheting. On the other hand, thicker fibers like cotton may require lower ratios for optimal results.
Understanding how Winding Ratios work can help you choose appropriate techniques when preparing your yarn before starting any project. By selecting an ideal ratio based on your type of fiber and desired outcome, you can ensure that your finished product has consistent quality throughout its length.
Traverse Ratio
It is calculated by dividing the package’s circumference by the traverse length, which refers to how far a guide moves back and forth while laying down each layer of yarn on top of another.
The Traverse Ratio plays a crucial role in determining several properties such as density, strength, and elongation. A higher Traverse Ratio results in denser packages with less air entrapment between layers.
On the other hand, lower Traverse Ratios result in softer packages with more air entrapment between layers.
When selecting your Winding Technique for your project or production line, it’s important to consider factors like Yarn Count and Type before deciding on an appropriate Traverse Ratio range suitable for achieving desired effects.
Wind Per Double Traverse
It is calculated as a ratio of length wound to double traverse length, and it affects both package density and unwinding behavior. A higher WPT results in denser packages with better unwinding characteristics, while lower WPT leads to softer packages but poorer unwinding performance.
The choice of WPT depends on various factors such as yarn count, fiber type, winding speed, machine type and manufacturer’s recommendations. For instance, finer counts require higher WPTs than coarser counts due to their low strength-to-weight ratio.
Similarly, synthetic fibers like polyester or nylon need more turns than natural fibers like cotton or wool because they have less frictional resistance.
Traverse Length
It is defined as the distance traveled by a guide or package holder from one end to another during one traverse cycle. The traverse length affects various properties of wound packages such as density, shape, and stability.
The choice of Traverse Length depends on several factors such as yarn count, package size and shape requirements for downstream processes like knitting or weaving. A longer Traverse Length results in fewer layers per unit length but increases productivity while reducing labor costs.
On the other hand, a shorter Traverse Length produces more layers per unit length resulting in higher package density with better stability but at lower productivity levels due to frequent stoppages required for changing bobbins.
Patterning
This technique involves changing the speed or tension of the winding process at specific intervals, resulting in a patterned appearance on the finished product. Patterning can be done manually or through computer-controlled machines, depending on your preference.
Manual patterning involves adjusting machine settings by hand during production to achieve desired effects. On the other hand, computer-controlled machines use pre-programmed patterns that are uploaded into their system for automatic execution.
Patterning is an excellent way to add visual interest and texture to your projects without having to change yarns frequently. It’s also perfect for creating stripes or color blocks with multiple colors of yarn.
When selecting a patterning method, consider factors such as type of yarn being used and intended end-use application. For instance, some types of patterning may not be suitable for delicate fibers like silk or cashmere due to potential damage caused by high tension levels during winding.
Ribboning
It happens when the yarn is wound too tightly, causing it to flatten and form a ribbon-like shape. This can be caused by several factors such as high winding speed, low tension, or improper package formation.
To prevent ribboning from occurring in your projects, it’s important to ensure that you are using the correct type of yarn for your project and selecting an appropriate winding technique. For instance, precision winding techniques like step-pitch precision or digicone may help reduce this defect.
Maintaining proper tension throughout the entire process can also help prevent ribboning from happening. You should also make sure that there are no gaps between each layer of yarn on your package as this could cause uneven pressure distribution leading to flattening of some areas.
Picture Zones
Picture zones refer to the areas on the package where there is a change in color or texture of the yarn. These changes can occur due to variations in dye lots, fiber blends, or even defects.
Precision winders use picture zones as reference points for controlling and adjusting their machines during production.
In addition to helping with quality control, picture zones also play an essential role in patterned knitting and crocheting projects. By strategically placing these areas within your project’s design layout, you can create unique patterns that add visual interest and depth.
However, it’s important to note that not all types of winding techniques produce clear picture zones. For instance non-precision random-wound packages may have irregularities throughout their length making them unsuitable for patterned projects requiring uniformity.
Non-Precision Winding
It is commonly used for low-quality yarns and fabrics, where the appearance of the final product is not important. In non-precision winding, the yarn is wound randomly onto a package without any regard to tension or alignment.
While non-precision winding may seem like an easy and straightforward process, it can result in several defects such as uneven tension across the package, loose ends sticking out from the sides of packages (known as “wild edges”), and poor unwinding properties.
Despite its drawbacks, non-precision winding has some advantages over other types of techniques. For instance, it requires less time to set up machines for this method compared to precision methods like step-patterning or digicone-winding.
Since there are no specific patterns involved in this technique; therefore fewer machine parts are required which reduces maintenance costs.
Random Winding
This method of winding is used when the package’s appearance does not matter, and the primary goal is to achieve maximum density. The yarn path in this type of winding can be irregular, which results in a less organized package compared to precision or step precision winding.
Random Winding has its advantages and disadvantages. One advantage of this technique is that it allows for faster production rates since there are no specific requirements for pattern or tension control during the process.
However, one disadvantage could be that it may lead to more waste due to uneven distribution on the package.
This type of winding works best with coarse counts where appearance doesn’t matter as much as functionality such as carpet backing or industrial fabrics like burlap sacks.
Drum Winding
This method is commonly used in industrial settings where large quantities of yarn need to be wound quickly and efficiently. The drum rotates at high speeds, allowing for consistent tension control and precise placement of the yarn on the package.
One advantage of drum winding is its ability to produce packages with uniform density throughout their length, which makes them ideal for use in weaving or knitting machines. This method can handle various types and counts of yarn without causing any damage or breakage.
However, there are some limitations associated with this technique as well. Drum-wound packages tend to have hard edges due to the pressure exerted by the machine during production.
To prevent these defects from occurring, it’s essential to adjust parameters such as traverse speed and tension carefully.
Wild Winding
This type of winding is perfect for creating unique and eye-catching designs, especially when using variegated or self-striping yarns. The wild-wound skeins have a distinctive look with varying thicknesses throughout the length of the strand.
To achieve this effect, wild winding machines use multiple spindles to wind several strands simultaneously onto one package. The machine randomly changes the speed and tension on each spindle, resulting in different levels of tightness between each strand.
While this technique produces beautiful results, it can also create some challenges during knitting or crocheting projects due to its uneven texture. However, many crafters enjoy working with these types of skeins as they add character to their finished products.
Precision Winding
This method involves winding the yarn onto a package at a constant tension and speed, resulting in uniform density throughout the package. Precision-wound packages are ideal for use in high-speed knitting or weaving machines as they reduce machine downtime due to fewer breaks and improve fabric quality.
The precision-winding process requires specialized equipment that can control various parameters such as traverse ratio, wind per double traverse, and crossing angle. The machines used for precision winding have sensors that detect any variations in tension or speed during the process to ensure consistent quality.
One of the advantages of precision winding is its ability to produce patterned packages with different colors or types of yarn wound together without causing tangles or knots. This feature makes it possible to create unique designs on fabrics without interrupting production flow.
Step Precision Winding
This technique ensures consistent tension and density throughout the entire package, resulting in high-quality yarn with minimal defects. Step Precision Winding is particularly useful for producing fine and delicate yarns that require precise tension control.
The process involves dividing the winding cycle into multiple steps, each with its own set of parameters such as traverse speed, take-up speed, and tension control. The computer controls these parameters to ensure that each layer of yarn is wound evenly without any overlaps or gaps.
One advantage of Step Precision Winding over other types of winding techniques is its ability to produce packages with uniform density from start to finish. This means there are no soft spots or hard edges in the package which can cause problems during subsequent processing stages like warping or weaving.
Digicone Winding
It is a precision winding method that produces cone-shaped packages with high density and low unwinding tension. The Digicone package has an inverted cone shape, which allows for better yarn control during the unwinding process.
This type of winding technology uses computer-controlled machines to wind the yarn onto cones at precise angles and densities, resulting in consistent quality throughout the package. The Digicone machine can also produce different types of patterns on the surface of the package, such as stripes or dots.
The benefits of using Digicone-wound packages are numerous: they have higher packing density than traditional cylindrical cones; they reduce waste by allowing more yarn to be wound onto each cone; they minimize downtime due to fewer changeovers required between cones; and their unique shape makes them easier to handle during transportation.
When selecting a suitable winding technique for your project needs, it’s essential first to consider factors like fiber type (natural vs synthetic), count (thickness), twist level (low vs high) before deciding on whether you need soft or hard-wound packages.
Hybrid Winding
It involves using a combination of different types of yarns, such as cotton and polyester, to create unique textures and patterns in your projects. Hybrid winding allows you to achieve the best possible results by combining the strengths of each type of yarn.
The process involves first randomly winding one type or color onto a bobbin before switching over to another type or color for precision-winding on top. This creates an interesting blend between two different types/colors while maintaining consistency throughout your project.
Hybrid-wound balls are perfect for those who want their finished product to have some texture without being too busy or overwhelming visually. They also work well when creating multi-colored items like blankets, scarves, hats etc., where you can use multiple colors in one ball without having them all mixed up together.
Conotronic Winding
This technique ensures consistent quality in the wound package, making it ideal for high-speed knitting or weaving machines. The Conotronic system can handle various types of fibers, including cotton, wool, silk, and synthetic materials.
The Conotronic system has several advantages over other types of precision winding techniques. It offers higher productivity due to its ability to wind at high speeds while maintaining excellent package quality.
It reduces waste by minimizing defects such as hard edges or soft centers.
However, like any other technology-driven process in textile manufacturing industries; there are some challenges associated with using this technique effectively. One significant challenge is ensuring proper maintenance and calibration of the electronic components used in this method regularly.
Random Vs Precision Vs Step-Precision Winding
Each technique has its own unique characteristics that can affect the final outcome of your project.
Random winding is a simple and straightforward technique where the yarn is wound onto a bobbin or spool without any specific pattern or order. This method produces irregularly shaped packages with varying densities throughout the package.
Precision winding involves using machines that wind yarn onto bobbins in an orderly manner at high speeds. The result is uniform packages with consistent density throughout each layer.
Step-precision winding takes precision one step further by allowing for more control over tension during the process. This results in even denser packages than those produced by precision-winding machines.
Choosing which type of technique to use depends on various factors such as fiber content, intended use for finished product and desired appearance among others. It’s important to note that while random-wound balls may look aesthetically pleasing they might not be suitable for all projects due to their unevenness which could lead to inconsistencies when knitting or crocheting.
On other hand Precision Winding provides consistency but may come at higher cost compared Random Winding.
Selecting Winding Technique
The type of yarn and its count play a crucial role in determining the appropriate winding method. For instance, soft-wound packages are ideal for delicate yarns such as silk or cashmere, while hard-wound packages work well with coarser fibers like wool or cotton.
Another important consideration is the end-use of your project. If you’re making a scarf or shawl that requires frequent unraveling and reworking, then center-pull balls may be more suitable than cakes or skeins.
Different types of winding techniques can produce varying effects on your finished product. Precision winding creates smooth and even tension throughout the entire length of yarn while random winding produces an irregular texture that adds character to your project.
Type of Yarn
Different types of yarn require different levels of tension and winding angles to achieve optimal results.
For example, delicate or slippery fibers like silk or bamboo may require a softer winding technique that prevents stretching and breakage. On the other hand, sturdier fibers like wool or cotton can handle more tension during winding without compromising their quality.
Thicker yarns may need larger winders with wider spindles to accommodate their bulkiness while finer threads can be wound on smaller spindles for better control over tension.
Understanding your specific type of fiber is essential when selecting your preferred method for achieving an organized ball or cake that will make knitting and crocheting easier.
Yarn Count
It refers to the thickness of a strand of yarn and is measured in various units, such as Denier, Tex, or Metric Count. The higher the count number, the finer and thinner the yarn will be.
When winding your own skeins or balls of yarn at home using a swift and ball winder machine (or by hand), it’s important to know what type of count you’re working with so that you can adjust accordingly. For example, if you’re working with a thicker count like bulky weight (#5) or super bulky (#6), then winding them into center-pull balls may not be practical due to their size.
On the other hand, if you’re dealing with finer counts like lace weight (#0) or fingering weight (#1), then precision winding techniques may be necessary for optimal results in your projects.
FAQ: Hybrid, Digicone, Conotronic Differences
Hybrid, Digicone, and Conotronic are some popular types that you might have come across while exploring different yarns.
Hybrid Winding is a combination of precision and random winding techniques that offer excellent package density with minimum defects. It is suitable for high-speed machines and can handle a wide range of yarn counts.
Digicone Winding produces cone-shaped packages with uniform density throughout its length. This technique ensures minimal unwinding tension during knitting or weaving processes.
Conotronic Winding uses an electronic traverse system to produce cylindrical packages with consistent density from start to end without any pattern defects.
Understanding these differences will help you select the right type of winding technique based on your project requirements and machine capabilities.
FAQ: Soft Wound Package Defects
However, like any other technique, soft winding can also result in some defects that may affect the quality of your project. Here are some frequently asked questions about soft wound package defects:
Q: What is a “soft edge” defect? A: A “soft edge” defect occurs when the edges of the package become loose and fluffy due to insufficient tension during winding.
Q: How can I prevent “soft edges” from occurring? A: To prevent this type of defect, it’s important to ensure that there is enough tension on the yarn during winding. You should also check for any irregularities in your machine or equipment that could be causing uneven tension.
Q: What causes “hard centers” in my soft-wound packages? A: A hard center occurs when there is too much pressure applied to the center core during winding. This can cause compression and make it difficult to pull out yarn from inside.
FAQ: Hard Edges
This is known as “hard edges” in winding terminology. Hard edges can be caused by various factors such as high tension during winding, improper package shape or size, or even due to the type of fiber used in making the yarn.
One way to prevent hard edges is by adjusting your winding machine’s parameters such as traverse speed and tension settings according to your specific type of yarn. Another solution could be using a different package shape like cylindrical instead of conical for better control over edge hardness.
FAQ: Preventing Hard Edges
These hard edges can cause issues such as yarn breakage, uneven tension, and poor quality of the final product. However, there are several ways to prevent hard edges from occurring in your wound packages.
One way to prevent hard edges is by adjusting the traverse speed of your winding machine. A slower traverse speed will allow for more even distribution of yarn across the package and reduce stress on individual strands.
Another method is to adjust the tension settings on your machine. Too much tension can cause excessive stretching and lead to hard spots in your wound package.
It’s also important to ensure that you’re using high-quality yarn with consistent thickness throughout each strand. Inconsistent thicknesses within a single strand can create weak points that may result in breaks or knots when winding onto a package.
Lastly, regular maintenance checks on equipment such as guides and rollers should be performed regularly since worn-out parts could contribute significantly towards creating defects like Hard Edges.
Quality Control in Winding Section
It ensures that the final product meets all quality standards and specifications. Quality control measures are implemented at every stage of the winding process, from raw material selection to finished product packaging.
The first step in quality control is selecting high-quality raw materials for production. The yarn manufacturer must ensure that only top-grade fibers are used to produce their products.
During production, various parameters such as tension, speed, and temperature must be monitored closely to ensure consistency throughout each batch produced. Any deviation from set parameters can result in defects such as unevenness or breakage during processing or use by customers.
After production comes inspection where a trained team checks for defects like knots, slubs (thick spots), thin places (thin spots), neps (tiny balls of fiber) among others before packaging takes place.
Soft Winding Production Parameters
The process involves winding the yarn onto a package with low tension and high density, resulting in an easy-to-use product that can be unwound without any tangling or knotting. To achieve this effect, several production parameters must be considered during the soft-winding process.
The first parameter is tension control. Soft-wound packages require low tension to maintain their fluffiness and prevent damage to delicate fibers such as wool or silk.
Tension control devices are installed on modern winders that automatically adjust the speed of rotation based on feedback from sensors placed at various points along the winder.
Another important parameter is package density control. Soft wound packages have higher densities than hard wound ones because they need more material per unit length due to their lower packing efficiency (less fiber per volume).
Density can be controlled by adjusting traverse pitch (distance between adjacent coils) and/or take-up speed.
It’s essential to monitor temperature during production since heat generated by friction between fibers may cause shrinkage or deformation of some materials like nylon or polyester if not kept under check.
Soft Winding Production Calculation
The production of soft wound packages involves several parameters that need to be calculated accurately for optimal results. These parameters include traverse length, wind per double traverse, and package density.
Traverse length refers to the distance traveled by the yarn guide from one end of the package to another during winding. It is an essential parameter as it determines how tightly or loosely packed your yarn will be on your bobbin or cone.
Wind per double traverse (WPT) refers to how many times you wrap your yarn around a bobbin or cone before moving onto another layer. WPT affects both package density and quality; therefore, it’s crucial that you calculate this parameter correctly.
Package density measures how much space your wound-up material occupies on a given surface area; hence its importance in determining product quality.
Hard Winding Production Parameters
The hard-wound package has a cylindrical shape with flat ends, which makes it easy to stack and transport. To achieve the desired hardness of the package, several parameters need to be considered during production.
The first parameter is tension control. Tension should be kept constant throughout the winding process as fluctuations can lead to uneven yarn distribution on the package surface or even breakage of yarns.
Another important parameter is traverse speed, which determines how fast or slow each layer of yarn will be wound onto the bobbin core. A slower traverse speed results in more layers per unit length and thus denser packages with higher hardness levels.
The third critical factor in hard-winding production is pressure control between layers; this ensures uniformity across all sections while preventing any air pockets from forming inside them that could cause defects such as soft spots or bulges when unwound later on downline processes like warping machines where they’re stretched out before being woven into fabric sheets!.
Flow Chart of Soft Winding
The process involves winding the yarn onto a package with low tension and high density, resulting in a soft and flexible product that can be easily unwound during knitting or crocheting. To better understand this process, let’s take a look at the flow chart of soft winding.
The first step in this process is to select the appropriate type of machine for your specific needs. Once you have selected your machine, it’s time to prepare it by cleaning and lubricating all necessary parts.
Next comes loading of bobbins on creel followed by threading them through various guides before entering into drafting zone where they are drafted as per required count & twisted if needed. After drafting comes pre-tensioning which helps reduce snarls while running at higher speeds later on.
Then we move towards actual Soft Winding stage where bobbin gets mounted on spindle & traverse starts moving back n forth creating layers over each other till desired diameter achieved. Once finished with Soft Winding stage then final operation includes doffing off package from spindle followed by labeling/tagging/boxing etc depending upon customer requirements.
Flow Chart of Hard Winding
It is commonly used for weaving and warp knitting applications where the yarn needs to be strong and stable. The process involves passing the yarn through tensioners, guides, and a series of rollers before it is wound onto a cylindrical package.
The flow chart of hard winding starts with unwinding the cones or bobbins on creel stands. The yarn passes through tensioners that ensure consistent tension throughout the process.
Then it goes through guide bars which direct it towards an oscillating comb that spreads out any entangled fibers.
Next, the yarn enters into contact with several sets of rollers arranged in different configurations depending on machine type (single-end or double-end). These rollers are responsible for controlling both traverse speed as well as package density by applying pressure to each layer being added onto itself until reaching desired thickness level without causing damage due excessive compression force applied during this stage.
After passing all these stages successfully without defects such as broken ends or knots forming along its length while maintaining uniformity across layers within each wrap around cylinder surface area – resulting in high-quality output product ready for further processing downstream!.
FAQ
What are the different types of winding packages?
Answer: The different types of winding packages are parallel winding, near parallel winding, and cross winding.
What is the difference between quill winding and regular winding?
The difference between quill winding and regular winding is that quill winding involves transferring yarn from a larger package to a smaller quill without a yarn clearing zone for inspection, while regular winding includes the inspection of yarn.
What is the winding process of yarn?
The winding process of yarn involves creating large cone-shaped packages from smaller yarn packages (ring cops), enabling their use in subsequent machinery while also correcting spinning faults such as neps, hairiness, and waxes.
What is the type of winding process?
The winding process is the transferring of yarns from ring, bobbin, hank into a suitable package, which can be electrical or mechanical, involving warp winding (cone, cheese, flanged bobbin) and weft winding (pirn, cop).
What are the benefits of precision winding in yarn production?
Precision winding in yarn production offers benefits such as improved yarn quality, reduced breakage, and increased efficiency in downstream processes.
How does the tension control in yarn winding affect the final product quality?
The tension control in yarn winding significantly impacts the final product quality by ensuring uniform tension, which results in consistent texture and strength throughout the material.
What factors should be considered when selecting a yarn winding machine?
When selecting a yarn winding machine, consider factors such as winding speed, tension control, bobbin compatibility, machine size, and cost.