Discover the various types of yarn faults and learn how to identify and prevent them in order to enhance the quality of your knitting projects.
Are you tired of finding knots, tangles, and other yarn faults in your projects? As a yarn enthusiast, I know how frustrating it can be to encounter these issues. But don’t worry! In this article, we’ll explore the most common types of yarn faults and how to avoid them.
From slubs to shedding, we’ll cover it all so you can create flawless projects every time. So grab your hook or needles and let’s dive into the world of yarn faults!
Thick and Thin Places
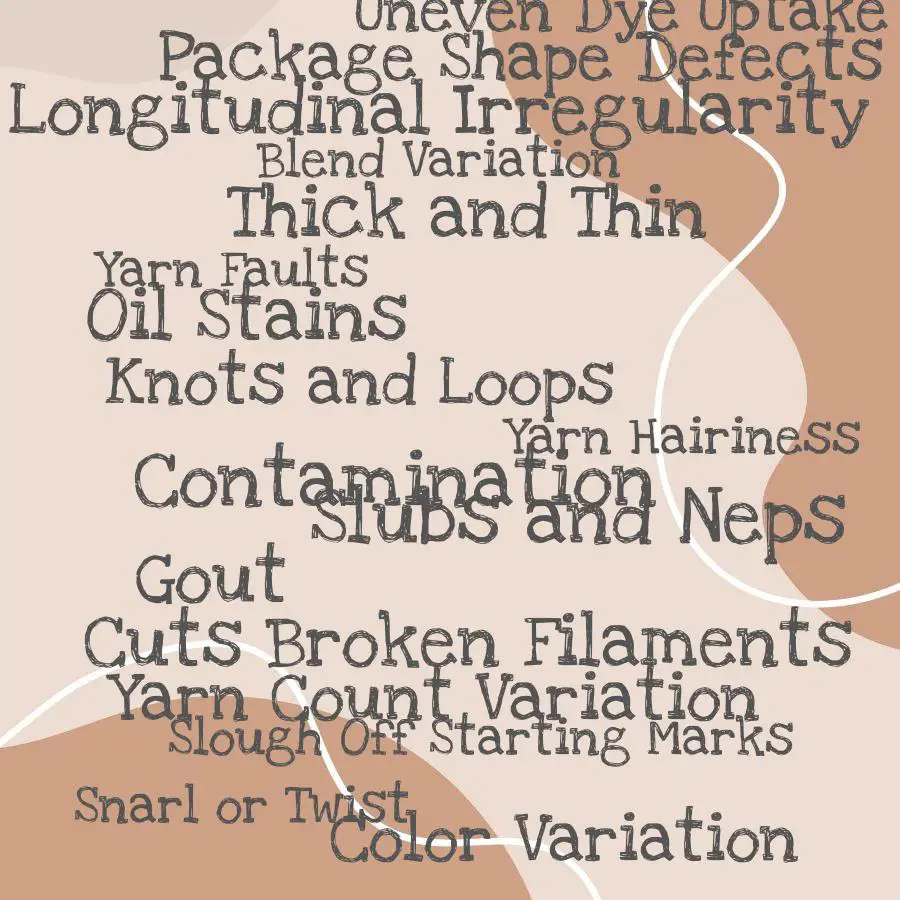
Thick and thin places are common yarn faults that can occur during the spinning process. These areas of uneven thickness can cause issues in your knitting or crocheting projects, such as lumps or holes.
Thick places are sections of yarn that have a larger diameter than the rest of the strand, while thin places have a smaller diameter.
To prevent thick and thin places from occurring, it’s important to choose high-quality yarns with consistent thickness throughout. However, if you do encounter these faults in your project’s yarn, there are ways to work around them.
One solution is to adjust your tension when working with thicker or thinner sections of the strand. For example, if you come across a thick place in your project’s yarn while knitting or crocheting stitches tightly together may help even out its appearance.
Another option is to use textured stitches like bobbles or popcorns over thicker areas so they blend into the fabric more seamlessly. Similarly for thinner spots using lace patterns will make those parts less noticeable by creating an openwork effect on those parts.
Slubs and Neps
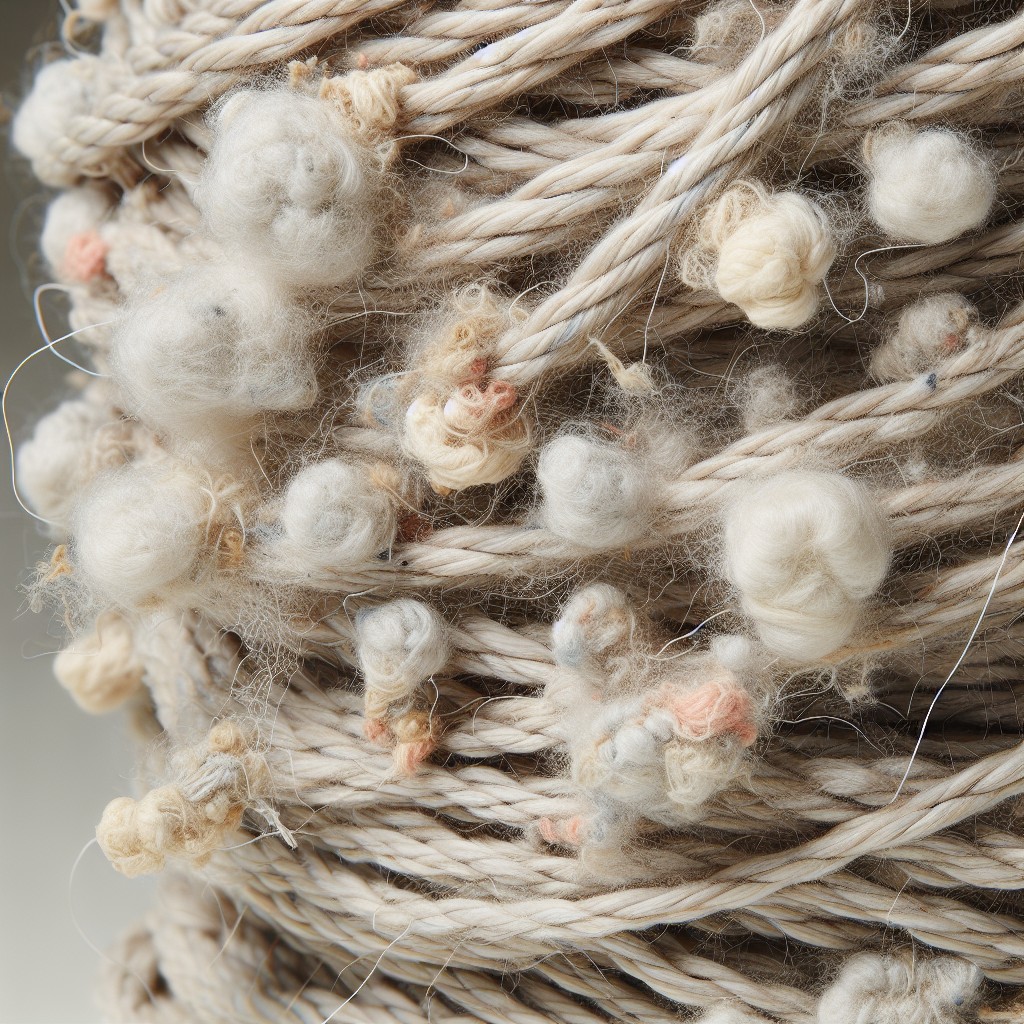
Slubs are thick areas in the yarn that occur when there is a sudden increase in thickness, while neps are small knots or bumps on the surface of the yarn. These faults can be caused by a variety of factors, including uneven spinning or contamination during production.
To prevent slubs and neps from appearing in your projects, it’s important to carefully inspect your yarn before you begin knitting or crocheting. Look for any thick spots or bumps on the surface of the skein and remove them if possible.
If you do encounter slubs or neps while working with your yarn, don’t panic! There are several techniques you can use to minimize their appearance. One option is to simply knit through them as usual; this will create an interesting texture that can add character to your project.
Alternatively, you may choose to remove any particularly large slubs by cutting them out with scissors (being careful not to cut too much). For smaller imperfections like neps, gently pulling at them with a crochet hook may help smooth out their appearance.
Contamination
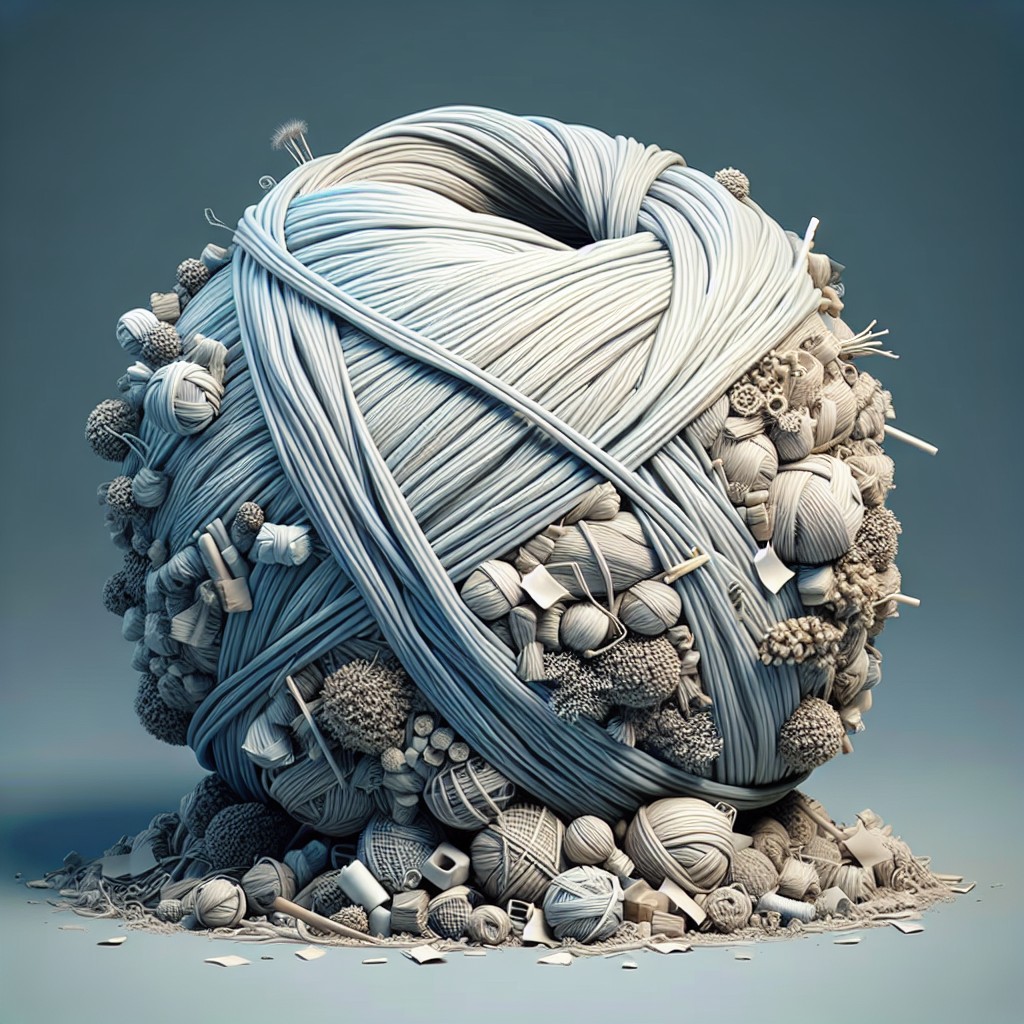
It occurs when foreign materials such as dirt, dust, or other fibers get mixed with the yarn during production. Contaminated yarn can cause discoloration and weaken the strength of your project.
To prevent contamination, it’s important to inspect your skeins before starting a new project. Look for any visible debris or unusual colors in the yarn.
If you notice any issues, contact the manufacturer immediately to resolve them.
In addition to checking for contamination before use, it’s also essential to store your unused skeins properly in a clean and dry environment away from potential contaminants like pets or food particles.
Knots and Loops
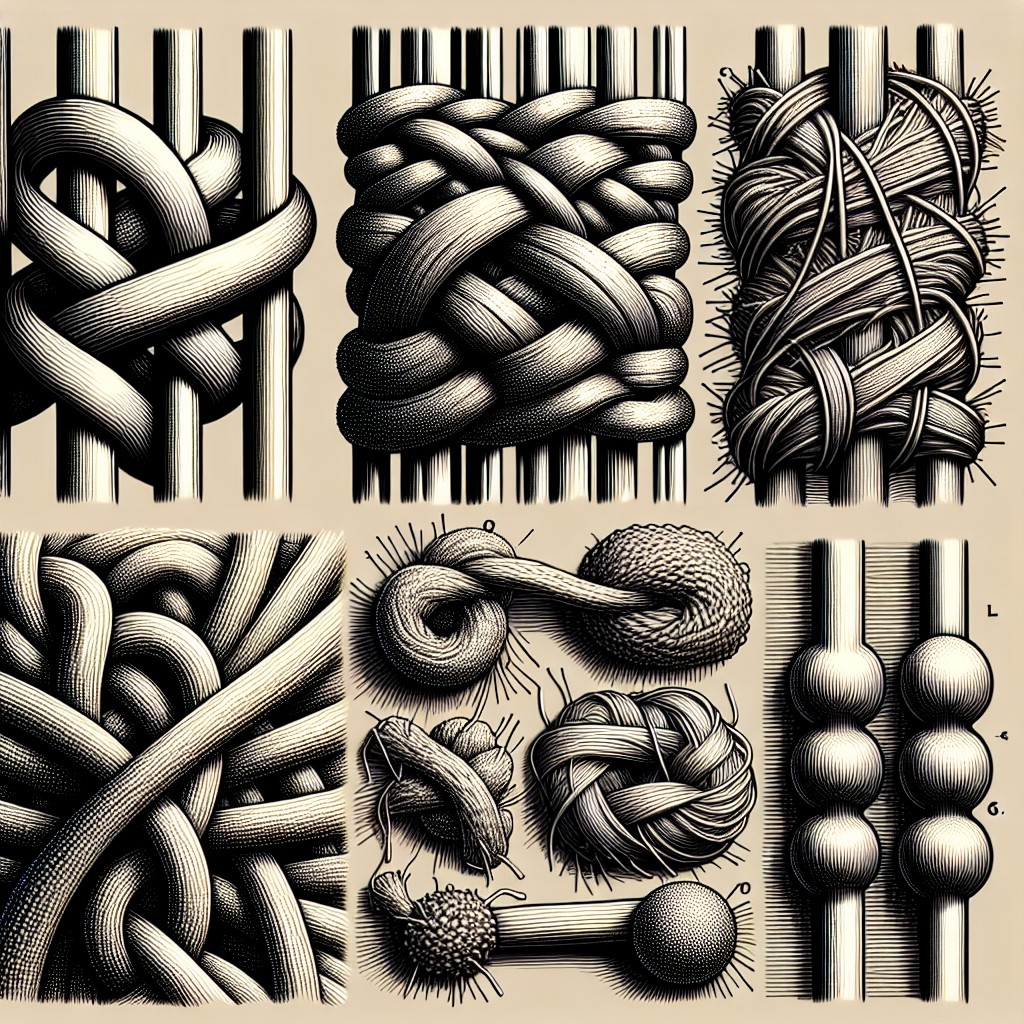
Knots occur when the yarn is spun together, resulting in a knot or lump in the middle of your project. Loops, on the other hand, happen when there is an extra loop of yarn that has not been properly twisted into place.
To prevent knots and loops from ruining your projects, it’s important to inspect your skeins before starting a new project. Look for any visible knots or lumps by running your fingers through the skein.
If you find one, carefully untangle it before continuing.
If you do encounter a knot while working on a project, don’t panic! Simply cut out the knot and rejoin the two ends using one of several methods such as weaving in ends or splicing techniques like Russian join.
Longitudinal Irregularity
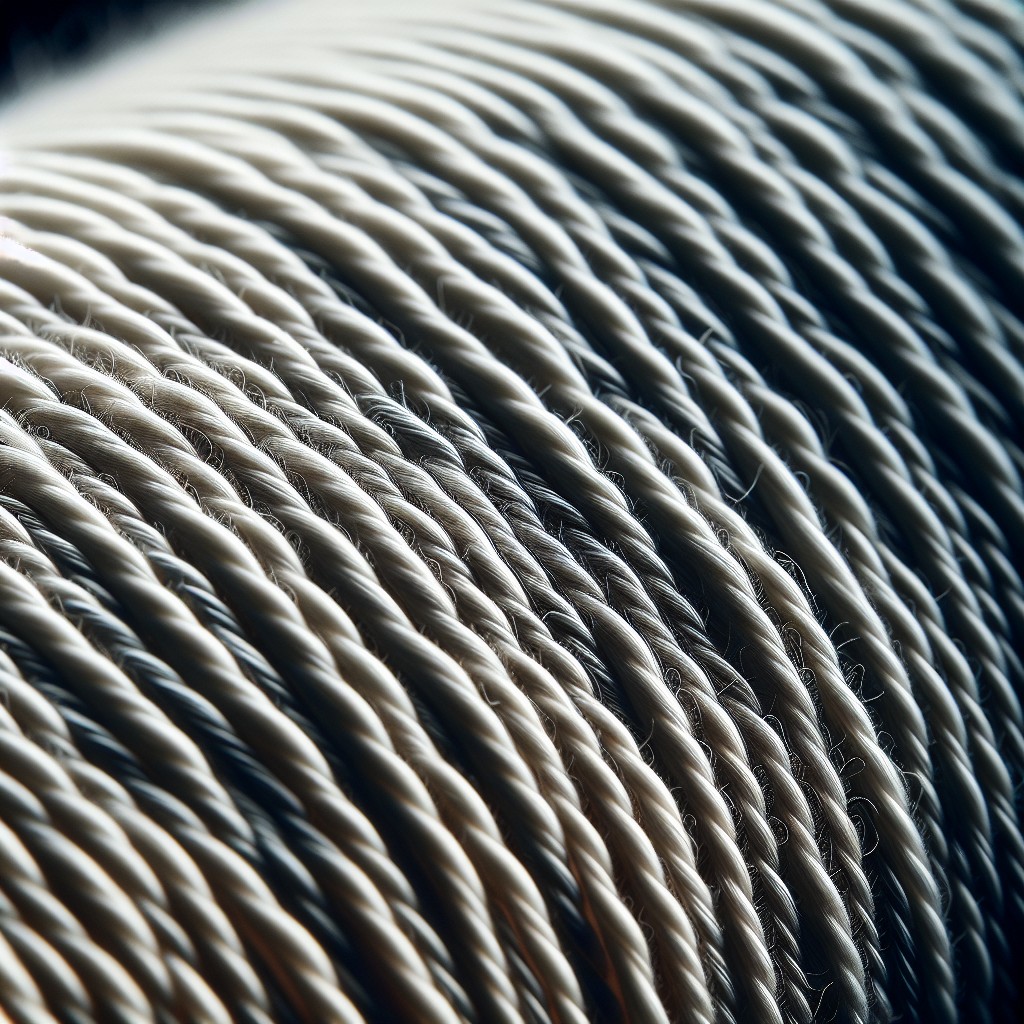
This defect causes variations in thickness along the length of the yarn, resulting in an uneven appearance and texture when knitted or crocheted.
One way to prevent longitudinal irregularity is to ensure that the spinning machine’s tension is consistent throughout production. Inspecting your skeins before purchasing them can help you avoid this issue altogether.
If you do encounter longitudinal irregularities while working on a project, there are a few ways to address it. You could try adjusting your needle size or stitch pattern to accommodate for any changes in thickness.
Alternatively, if only certain sections of your skein are affected by this defect, consider cutting out those areas and joining new lengths together using Russian joins or other techniques.
Yarn Hairiness
It occurs when fibers protrude from the surface of the yarn, creating a fuzzy or hairy appearance. This can be caused by several factors, including poor spinning techniques and low-quality fibers.
To prevent yarn hairiness, it’s important to choose high-quality yarns made from long-staple fibers such as wool or silk. These types of fibers are less likely to break and create fuzz on the surface of your project.
You should avoid using blunt needles or hooks when working with hairy yarns as they tend to catch on loose strands and exacerbate hairiness issues. Instead, opt for sharp-tipped tools that will glide smoothly through each stitch without snagging any stray hairs along the way.
Snarl or Twist
This occurs when the fibers in the yarn become twisted, causing it to knot up on itself. The result is a tangled mess that can be difficult to work with.
To prevent snarls and twists, it’s important to pay attention to how you’re handling your yarn while working on your project. Avoid pulling too tightly or allowing the yarn to twist around itself as you work.
If you do encounter a snarl or twist in your project, don’t panic! Take a deep breath and gently untangle the affected area using your fingers. If necessary, use scissors or a seam ripper to carefully cut away any knots without damaging the rest of your work.
Blend Variation
This can happen due to poor blending during production or mixing different batches of fibers. Blend variation can result in uneven dye uptake and color variations throughout your project, making it look unprofessional.
To avoid this issue, always check the label for fiber content before purchasing your yarn and try to buy from reputable brands that have strict quality control measures in place. If you notice any blend variation while working with a particular skein or ball of yarn, consider alternating between two balls every few rows to help distribute any differences evenly throughout your project.
By being aware of these types of faults and taking steps to prevent them, you’ll be able to create beautiful projects without worrying about unexpected bumps along the way!
Package Shape Defects
These occur when the yarn is wound onto a cone or spool and the winding process isn’t done correctly. The result can be uneven tension, which leads to bumps or lumps in the yarn that can cause problems during knitting or crocheting.
To prevent this issue, it’s important to check your cones or spools before purchasing them. Look for any visible deformities such as bulges, dents, and other irregular shapes that could indicate poor winding quality.
If you do encounter package shape defects while working with your yarn, try rewinding it onto another cone/spool by hand using even tension throughout the process. This will help smooth out any bumps and make for a more consistent texture in your finished project.
Cuts and Broken Filaments
This can occur during the spinning process, when the fibers are being twisted together to form the yarn. If a fiber breaks or is cut, it can weaken the overall structure of the yarn and cause it to break more easily during use.
To prevent this issue, look for high-quality yarns that have been spun carefully with minimal cutting or breaking of fibers. You should also inspect your skeins before starting a project to ensure there are no visible cuts or breaks in any of them.
If you do encounter this problem while working on a project, try splicing in new lengths of yarn instead of knotting them together.
Yarn Count Variation
This occurs when the thickness of the yarn varies throughout a skein or ball. It can be caused by inconsistencies in spinning, twisting, or plying during manufacturing.
To avoid this issue, it’s important to check the label for information on the weight and yardage of each skein before starting your project. You should also inspect each skein carefully for any variations in thickness before beginning to knit or crochet.
If you do encounter a variation in yarn count while working on your project, don’t panic! Simply adjust your tension accordingly and continue with caution until you reach an area where the thickness stabilizes again.
Color Variation
This occurs when there are inconsistencies in the dyeing process, resulting in different shades or hues within a single skein or batch of yarn. Color variation can be subtle, such as slight differences in tone, or more noticeable with distinct patches of color.
To prevent this issue from occurring, it’s important to purchase enough yarn for your project from the same dye lot and manufacturer. If you’re unsure about how much you’ll need for a particular project, it’s always better to err on the side of caution and buy extra.
If you do encounter color variation while working on your project and find that it bothers you aesthetically – don’t worry! There are ways to work around this issue by strategically placing areas with similar colors together so that any variations blend seamlessly into one another.
Uneven Dye Uptake
This type of fault occurs when the dye is not absorbed evenly by the fibers, resulting in areas of lighter or darker shades within the same skein.
One way to prevent uneven dye uptake is to choose high-quality yarns from reputable brands that have strict quality control measures in place. It’s important to follow care instructions carefully and avoid exposing your finished projects to harsh chemicals or direct sunlight.
If you do encounter uneven dye uptake while working on a project, there are some steps you can take to minimize its impact. One option is blending different skeins together so that any variations in color are less noticeable.
Alternatively, if only small sections of your work are affected by this issue then consider incorporating them into textured stitches like cables or lacework where they will blend more naturally.
Oil Stains
These can occur during the manufacturing process when lubricants are used to help the fibers move smoothly through machines. While necessary, these oils can sometimes leave unsightly stains on your yarn that are difficult to remove.
To prevent this issue, look for high-quality yarns that have been properly processed and washed before being sold. If you do encounter an oil stain on your project, try using a gentle detergent or degreaser specifically designed for removing grease and oil stains from fabrics.
Remember, identifying and preventing these types of faults in your yarn will not only improve the appearance of your projects but also make them more durable over time.
Slough Off
This can result in an unsightly appearance and weaken the overall structure of your project. Slough off can be caused by several factors, including poor quality fiber, improper spinning techniques, or excessive tension during winding.
To prevent slough off from occurring in your projects, it’s important to choose high-quality yarns with strong fibers that are less likely to break away. Make sure you’re using proper tension while working with your yarn and avoid over-handling it as much as possible.
If you do encounter sloughing-off while working on a project don’t panic! You may be able to salvage some parts by carefully trimming any loose fibers without damaging the rest of your work. However if there is too much damage then unfortunately sometimes unraveling and starting again might be necessary.
Starting Marks
Starting marks occur when the yarn is initially wound onto the cone or spool during manufacturing. The machine that winds the yarn may have an oil leak, causing spots on the first few yards of yarn.
While starting marks are not necessarily harmful to your project, they can be unsightly and affect its overall appearance. To prevent them from showing up in your work, try cutting off a small section at the beginning of each new skein or ball before using it in your project.
Gout
This results in an uneven distribution of fiber, causing some areas to be thicker than others. Gout can also cause knots and loops to form in your project, making it difficult to work with.
To prevent gout from occurring, it’s important to choose high-quality yarns that have been spun correctly. Look for smooth and consistent strands without any lumps or bumps.
If you do encounter gout while working on a project, try gently pulling apart the affected area and smoothing out any knots or tangles.
Remember that identifying different types of yarn faults takes practice but once you know what to look for, you’ll be able to create beautiful projects every time!.
FAQ
What are Classimat faults in yarn?
Classimat faults in yarn refer to the objectionable and thick faults categorized into 23 groups by the USTER Classimat-ii, with A4, B4, C3, C4, D3, D4 as objectionable faults, A3, B3, C2, D2 as short thick faults, and E and G as long thick faults.
In which process yarn faults are removed?
Answer: Yarn faults are removed in the yarn clearing process, where a yarn clearer is used to eliminate thick places, thin places, and foreign matter, resulting in improved yarn quality and better cloth.
What is yarn irregularity classification?
Yarn irregularity classification refers to the variation in fineness or mass per unit length along a yarn, expressed as U% or CV%.
What are the common causes of yarn faults in the spinning process?
Common causes of yarn faults in the spinning process include raw material quality, mechanical issues, worker skills, and environmental factors.
How do yarn fault detection technologies contribute to the improvement of yarn quality?
Yarn fault detection technologies contribute to the improvement of yarn quality by identifying and eliminating imperfections during the production process.
What are the various methods employed to prevent and resolve yarn faults during the manufacturing process?
Various methods employed to prevent and resolve yarn faults during the manufacturing process include regular equipment maintenance, process optimization, quality control, and employee training.